Measurement accuracy with IO-Link smart sensors
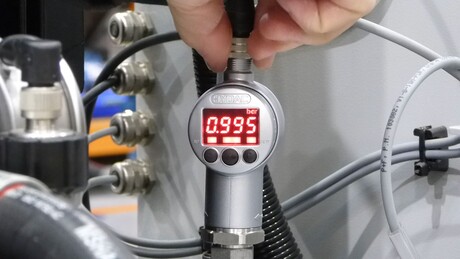
The IO-Link digital protocol ensures measurement accuracy, by reducing the number of conversions between analog and digital signals.
In pressure sensors supplied by HYDAC, a Wheatstone bridge measures deflection when fluid comes into the sensor through an orifice and pushes up against the cell. The bridge has an array of resistors so that when the cell deforms the resistance value changes.
The change in resistance value goes through an amplifier into an analog to digital converter, and from there goes to a microprocessor. The real-world value or physical property can be converted and compensated in the sensor’s microprocessor, and it is also possible to move from analog to digital and then make a conversion back into an analog value to send to a PLC.
Every time a value is converted, there is loss of accuracy in the measurement.
Often a sensor’s display may show for example 35.3 bar but the measurement comes up as 35.2 bar or 35.4 bar after the value has been transmitted to a PLC. This is because the analog to digital conversion from the sensor in the PLC depends on the quality of the analog input card and other such factors.
IO-Link effectiveness, efficiency, and accuracy
When the IO-Link smart protocol is used rather than analog transmission, a higher measurement accuracy is maintained, because the IO-Link protocol allows the sensor’s digital conversion of the physical property value to be communicated directly.
There is still the requirement to convert the analog measurement to digital and to apply temperature compensation or linearisation. However, the difference is in the way information is transmitted to the PLC via a communication chip in an IO-Link protocol and sent as a signal to the PLC.
It’s also important to note that the IO-Link protocol is based on an open standard, and IO-Link devices are produced by hundreds of vendors.
An IO-Link master is used to connect IO-Link sensors to the PLC. The IO-Link master communicates to the PLC via a fieldbus protocol such as Profinet, Modbus TCP, EtherNet/IP, EtherCAT or OPC UA.
HYDAC’s range of pressure sensor output types
The analog output types that are available in the HYDAC range of pressure sensors include 4–20 mA, 0–20 mA, 0–10 VDC, 0–5 VDC, and 0.5-4.5 VDC.
HYDAC also supplies relay switch or digital output sensors. These sensors come in two type relay types: normally open (NO) or normally closed (NC) as well as transistor outputs (PNP/NPN).
AMR pressure sensors
HYDAC has an extensive range of AMR pressure sensors on offer, including:
- EDS 3400 IO-Link pressure switch/transmitter
- EDS 820 IO-Link pressure switch
- EDS 8000 electronic pressure switch
- HDA 7446 pressure transmitter
- HPT 1400S smart IO-Link pressure sensor
To navigate the pressure sensor selection maze, please contact HYDAC on info@hydac.com.au or call 1300 449 322.
How to optimise WWTP flow measurement for process efficiency
In wastewater treatment plants, the right flow measurement instrumentation ensures optimal...
Precise flow measurement for ultra-pure water
Anton Paar's single straight tube L-Cor Coriolis mass flowmeters offer a reliable and...
Reducing emissions from industrial processes by effective particulate monitoring
Continuous particulate monitoring instruments play an important role in air pollution control.