How to optimise WWTP flow measurement for process efficiency
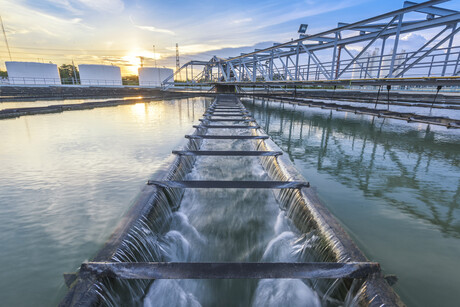
Whether a plant team is adding process measurements, replacing under-performing flow technologies, undertaking major automation upgrades, or designing new or expanded facilities, FCI has the right products for air and gas flow measurement, liquid and gas flow switching and alarms, and point level applications in municipal and industrial WWTP and WTP operations.
From wastewater aeration lines to digester gases, from potable water disinfection processes to pump flow protection, the right flow measurement instrumentation ensures optimal process operations and minimised maintenance that can save time and reduce expenses. With more than 10 unique and optimised flow measurement products, FCI has installed more air/gas flow meters and flow switch solutions in municipal wastewater and water treatment applications than any other supplier.
As a pioneer in thermal dispersion measurement technology, FCI thermal mass flow meters, thermal flow switches and level switches are the industry’s most recognised and installed throughout the world. FCI developed and remains the leader in thermal flow sensing constant power technology, has innovated techniques such as equal mass sensor and is the sole provider of the industry’s Vortab tab-type flow conditioners.
The simplicity and robustness of a thermal sensor in flow meter applications addresses many industrial technology concerns. The sensor is comprised of two platinum RTDs that are protected within thermowells. These sensors are fully welded to prevent migration of the measured gases into the instrument. One RTD is heated while the other provides a reference by measuring the process temperature. This temperature differential is directly proportional to the mass flow measurement of the process.
For example one of the industry’s newer renewable energy initiatives uses digester gas or biogas, which is measured with thermal flow meters, to help power co-generation and combined heat and power (CHP) systems. Depending upon the amount of digester gas or biogas produced at any given time, a supplemental supply of natural gas (NG) can be required. It is essential to understand the calorific value of the digester gas feed in order to supplement it with the correct amount of NG, maintaining a proper ratio to ensure the calorific value of the blended gas being fed to the engine ensures efficient, continuous operation.
In co-generation and CHP systems, thermal mass flow measurements maintain this proper ratio in order to achieve higher energy efficiencies. Capacity demand requires instrumentation with flow turndown capabilities as high as 100:1. Gas-specific calibrations ensure overall performance of the mass flow meter under actual field conditions. The use of FCI flow conditioners allows for reducing the footprint of meter runs in older crowded plants.
Precise flow measurement for ultra-pure water
Anton Paar's single straight tube L-Cor Coriolis mass flowmeters offer a reliable and...
Reducing emissions from industrial processes by effective particulate monitoring
Continuous particulate monitoring instruments play an important role in air pollution control.
TDLAS analysers: Revolutionising moisture measurement in natural gas
Tunable diode laser absorption spectroscopy (TDLAS) offers numerous advantages for moisture...