Reducing emissions from industrial processes by effective particulate monitoring
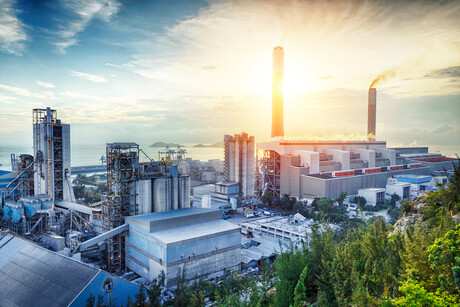
Reducing particulate emissions from industrial processes is a common goal for industrial plant operators across the industrialised world. A significant and growing number of industrial organisations understand that continuous monitoring plays an increasing role in reducing emissions since it provides the feedback to ensure dust arrestment plant continue to operate to optimum performance while reducing operating costs.
In general, dust arrestment plant is installed after industrial emission sources to reduce levels. While particulates may be controlled by electrostatic precipitators, cyclones, scrubbers and filters, the trend is to install filter type arrestment since they have higher collection efficiency, create no wastewater and can be designed to operate even at elevated temperatures. Particulate monitors are fitted after the arrestment plant to detect and monitor for malfunction or sub-optimal performance of the filter system, which if undetected will lead to increased particulate levels.
Particulate monitors can be used to pre-warn of imminent problems in filter systems by monitoring the dynamics of dust during the automatic cleaning cycle of a bag filter. High peaks in dust are associated with the cleaning of a bag row with a failing filter bag and therefore by synchronising the instrument to the cleaning control system, maintenance personnel can easily determine which bag row requires maintenance before a major incident occurs.
In addition, with large multi-compartment bagfilters, multi-probe dust monitoring systems can be used to detect and isolate the compartment causing elevated emissions which again allows emissions to be controlled.
It is now widely understood that increased particulate levels have a direct impact on human health problems and global pollution. Health problems are particularly apparent with small particles, which are absorbed by the human lungs, and particles with high carbon and metals content. Environmental regulators therefore worldwide stipulate emission limits for particulates. In addition many regulators require continuous particulate monitors to be fitted to industrial processes for the same two reasons:
- To enforce particulate emission limits in mg/m3 and kg/year.
- To provide feedback that pollution abatement equipment is working correctly.
The overall trend is that continuous particulate measurement is required in both the large stacks and those with environmentally-sensitive emissions. Other types of continuous particulate monitoring such as qualitative and filter failure detection can be required in smaller processes.
Particulate emission monitoring is a challenging technical field, not only because of the specific accuracy and performance of these monitors, but also due to the harsh environments in which they must continuously operate. To meet these challenges, Group Instrumentation have a comprehensive range of monitoring solutions to meet the broad needs of particulate emitting industries and the requirements of national regulations.
Applications generally fall within the following four categories.
Particulate measurement systems
These systems provide continuous measurement of particulate emission concentrations which, for a defined range of application conditions, have the accuracy and consistency of response to be reliably calibrated against isokinetic gravimetric test samples (Standard Reference Method, SRM). Group Instrumentation’s range of approved particulate measurement systems satisfy rigorous standards to meet our national regulatory requirements. Instruments are also available for non-regulatory measurement with similar performance to approved instruments.
Filter performance monitors
These monitors continuously monitor and display particulate emissions and indicate relative changes over time to provide valuable feedback on filter plant performance (for bag filters, cyclone filters, dryers and scrubbers). In addition, the ability to locate faulty filter media by row or compartment minimises the need to replace filtration media, reduces labour requirements for fault location and reduces process downtime.
Filter leak monitors
This category of particulate monitors track changes in emissions from particulate arrestment plant and provide a tool to minimise emissions and monitor for arrestment plant malfunction (e.g. damaged filtration media). Our range includes approved filter leak monitors where quality assurance features are required.
Dust gross filter failure detectors
These detectors track significant increases in particulate loadings to indicate failure in the arrestment plant (e.g. gross bag filter failure or cyclone overflow). Gross filter failure detector alarms typically require immediate reactive maintenance to be taken on the filter plant, as there is no pre-emptive warning or early indication of filter deterioration.
Summary
Continuous particulate monitoring instruments play an important role in air pollution control by providing industry with information to control arrestment plant as well as provide proof of emissions versus time. The regulatory approach is similar in most parts of the world with requirements for continuous measurement and qualitative monitoring of arrestment plant dependent on the type of plant and size of the process.
For more information click here.
How to optimise WWTP flow measurement for process efficiency
In wastewater treatment plants, the right flow measurement instrumentation ensures optimal...
Precise flow measurement for ultra-pure water
Anton Paar's single straight tube L-Cor Coriolis mass flowmeters offer a reliable and...
TDLAS analysers: Revolutionising moisture measurement in natural gas
Tunable diode laser absorption spectroscopy (TDLAS) offers numerous advantages for moisture...