Designing a measurement system for leak detection in hydrogen fuel cells
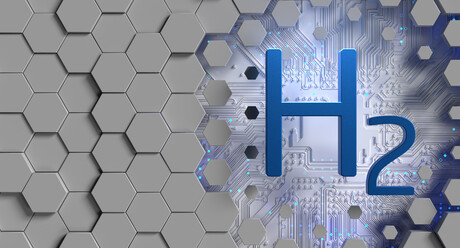
Society has started to move from fossil fuel utilisation to renewable energy to drive toward a sustainable future. Burning fossil fuels is no longer desirable due to greenhouse gases emissions that contribute negatively to global warming. Using renewable energy sources such as hydrogen offers clean and environmentally-friendly alternatives.
With the plan to build large-scale hydrogen plants underway, Australia has committed to reducing its reliance on fossil fuels and working with industry to reduce energy emissions. Green hydrogen is primarily produced via water electrolysis by splitting water molecules into hydrogen and oxygen with the help of electricity. It is a well-known technology for producing zero-emission hydrogen, but it only accounts for 4% of global hydrogen production due to its higher cost and difficulties in process scale-up.
As the government prepares to build large-scale electrolysers in Victoria and WA, Australia now has the potential to be one of the largest renewable energy exporters. The excess hydrogen can be stored in tanks, which later can be converted into electricity by using fuel cell systems. It is the preferred system for storing hydrogen as the battery loses its storage capacity over time.
Hydrogen is the smallest molecule, and as a result, it can easily permeate through objects and is highly flammable when in contact with oxidising compounds such as air. It is therefore extremely important to ensure that hydrogen tanks are free of leaks by implementing a monitoring system that can detect leaks at an early stage.
This has called for the development of a hydrogen fuel cell leak detection system. Currently, there is a compact and portable system the size of a suitcase. The leak detection process is straightforward: the fuel cell under test is connected to the system using a standard plug-in connector. Fuel cells typically consist of three channels — one for air (oxygen), one for hydrogen, and a cooling channel — each individually linked to the detection system. While the fuel cell is not running, a gas flow is connected to the fluidic chain that feeds the three channels. The tests are carried out independently — first using nitrogen, then hydrogen — to detect any leaks in the system. The cooling channel serves only to cool the fuel cells, which heat up during use.
Pressure sensors are needed to measure the pressure at the inlet and outlet of fuel cells. Loss of pressure indicates a leak in one of the flow channels. High-accuracy pressure transmitters are required in the measurement systems to detect the smallest leak.
Bestech Australia has supplied high-accuracy pressure transmitters from KELLER for local industries, which have also been integrated into the fuel cell leak detection systems above. The KELLER 33x pressure transmitters offer a high-precision measurement down to 0.01% of full scale, suitable for test bench applications or laboratory testing.
This sensor is extremely suitable for hydrogen applications as it is designed with nickel alloy with a low embrittlement rate. Hydrogen embrittlement is a common occurrence due to its high permeability through the material, causing mechanical damage. It causes loss of ductility and tensile strength, which can prematurely fail the material. Any sensors used for hydrogen application must therefore be designed with special materials and reinforced with a special coating to prevent hydrogen from penetrating.
For fuel cell testing applications, it is important to ensure the sensors are protected against damage from hydrogen penetration to avoid early breakdown. Gold coating techniques have been used in many applications to increase the chemical resistance of the material. The sensor can be protected against damage from hydrogen permeation by applying a gold coating layer to the sensing diaphragm.
Working together with its partner KELLER, Bestech has been able to supply gold-plated diaphragm pressure sensors for hydrogen applications. These pressure sensors can be customised with various process and electrical connections to suit different projects. Most importantly, these sensors are certified as intrinsically safe to suit measurement in hazardous and flammable environments.
Bestech Australia can provide custom sensor solutions from its standard range of pressure sensors for hydrogen applications, and not limited to the KELLER 33X: for example a custom-manufactured digital pressure gauge with a gold-plated membrane for pressure measurement in hydrogen pipelines. With its recording function, it can display and store the recorded pressure and temperature data over long period of time.
For any questions regarding pressure measurement in hydrogen applications, contact the engineers at Bestech Australia at 03 9540 5100 or email enquiry@bestech.com.au.
How to optimise WWTP flow measurement for process efficiency
In wastewater treatment plants, the right flow measurement instrumentation ensures optimal...
Precise flow measurement for ultra-pure water
Anton Paar's single straight tube L-Cor Coriolis mass flowmeters offer a reliable and...
Reducing emissions from industrial processes by effective particulate monitoring
Continuous particulate monitoring instruments play an important role in air pollution control.