Automating fill level measurement for granulates
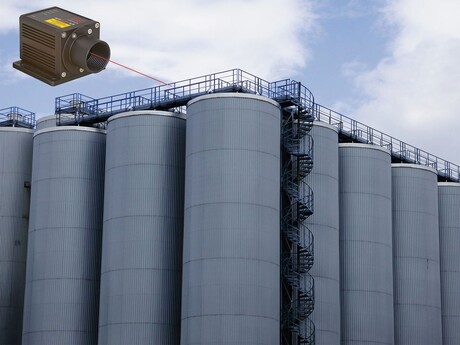
Long-range laser sensors are a flexible solution for monitoring fill levels of granulates in silos.
Powder granulation is one of the most viable methods to produce granulates by blending multiple types of materials. This process is developed with the intention of easing the handling of raw materials and making them easier to be transported. This technique has been applied in manufacturing dairy, fertiliser and pharmaceutical products to improve their bulk storage quality in silos or tanks.
To avoid manufacturing and logistics problems, manufacturers must first ensure that the product quantity in the tank is precisely measured. These measurements are performed continuously to ensure sufficient volume in the tank. Industrial weighing load cells have been used in the past for this measurement, and although they can accurately measure the weight of materials in the tank, they cannot be used to measure the fill level of the tank.
An alternative is to use ILR2250 long-distance laser sensors on the lid at the top of the silo to perform continuous measurement towards the bottom of the tanks. The measured distance calculates the volume of materials remaining in the tank or the amount displaced for processing. This compact sensor offers a stable measurement signal over continuous exposure and can accurately detect coarse grain and dark surfaces, making it suitable for this application.
These long-range laser sensors operate based on the phase-comparison principle, where distance is measured by determining the phase shift from the reflected high-frequency modulated laser light with the reference signal. The ILR2250 offers the capability of measuring down to millimetre precision up to a distance of 100 m, which makes it ideal for this type of measurement application.
Material discharged from silos is expected to follow a funnel-shaped discharge pattern. Therefore, laser sensors must measure at numerous points to get accurate measurement results. At least three laser sensors are required to generate accurate data. This industrial laser sensor can also be fitted with an air purge cleaning system and protective glass to ensure adaptability in filling level measurement applications.
Ease of monitoring and control
Once the measured results are obtained, they can be looped in real time to the process control system via a USB, Ethernet or digital RS422 interface. The system can use this data to calculate the exact filling level, the residual volume and the volume of granulates needed to replenish the tank. The results can be transferred and displayed at the central control room, allowing the operators to monitor the filling performance in real time and take immediate intervening actions if required.
This autonomous, real-time monitoring system offers the advantage of avoiding the overfilling, slipping and emptying of bulk materials. It ensures that there is always sufficient material in the tank, preventing manufacturing delays that could occur due to a shortage of raw materials.
The system can be configured to trigger an early warning alarm when the fill level falls below the desired level. With the flexibility of this automated measurement system, operators can plan for materials replenishment at an earlier stage and avoid production downtime.
The ease of installation, commissioning and integration of the ILR2250 means that manufacturers can develop, expand or retrofit their current equipment without complex reset and commissioning work for the new system. The flexibility of this system introduces a significant cost saving for the manufacturer.
How to optimise WWTP flow measurement for process efficiency
In wastewater treatment plants, the right flow measurement instrumentation ensures optimal...
Precise flow measurement for ultra-pure water
Anton Paar's single straight tube L-Cor Coriolis mass flowmeters offer a reliable and...
Reducing emissions from industrial processes by effective particulate monitoring
Continuous particulate monitoring instruments play an important role in air pollution control.