State-of-the-art techniques for lubricant condition monitoring
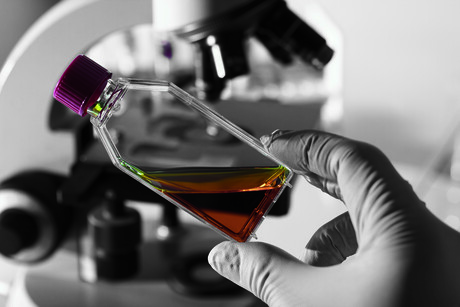
Lubricants are the vital fluid of machinery. Moisture and particle contamination can easily result in machine damage and potential failure. Condition monitoring enables issues to be identified and allows corrective action to be taken before a failure occurs, an activity that has become even more critical as oil prices climb steadily.
To assist with condition monitoring, HYDAC has an extensive range of sensors to collect and interpret data for in-depth and holistic analysis.
The sensors include pressure, flow, temperature, oil level, water, oil condition, and particle definition.
“HYDAC’s advantage is that it has its own electronics department, meaning we can construct sensors in-house,” said a HYDAC spokesperson. “Once we provide a distributed sensor array and install it over all the operating equipment at a particular plant, we can collect the data on a single analyser and examine it at a later and more convenient time, or we can monitor it live.”
Not just data collection but data interpretation
The spokesperson emphasises that it’s important to note that condition monitoring is not just about collecting data but interpreting it.
“I think this is where a lot of commercial and very sophisticated labs fall short because they report tables, but they artificially set limits on the basis of some specifications and don’t go beyond that simplified method of analysis,” they said. “In some cases, I’ve run into issues where intricate situations have occurred. But if you looked at them from the normal maintenance perspective, they were by no means extraordinary.
“And yes, certain components have failed. And to prevent this, additional analytical thinking is involved, not just procedures.”
The spokesperson says that analytical thinking can be followed by time-based maintenance.
“This means that every two months you change some components because you know that on average there’s a failure after three months. That’s already better than being reactive, but not necessarily elegant.”
Condition-based and predictive maintenance based on condition monitoring
The spokesperson highlights that predictive maintenance is based on condition monitoring.
“These types of maintenance practices encompass many different factors, with the trick being to put all these factors together, which is what affects oil service life.”
Factors that affect oil service life from complex interplay
Oil service life is affected by ageing, degradation and contamination, with contamination being the result of chemicals (fluids) or physical (solids).
“Obviously temperature and particulates are included, but not all kinds of particulates. For example, silica sand, in terms of chemical activities, is innocuous. However, it leads to abrasion, which generates metallic particulate with very highly active surfaces that can lead to a chemical impact on oil service life,” the spokesperson says.
Another example is water, which can lead to hydrolytic breakdown of both additives and base stocks.
“Here, it is highly dependent on which additives and base stock are employed as certain base stocks are much more prone to hydrolysis than others,” the spokesperson says. “As saturation plays a big role in this regard, it’s also significant as to whether the water is free or dissolved.”
The spokesperson points out that this has an impact on filter service life because filter service life will decrease quite dramatically if a lot of chemicals and contaminants are generated through chemical breakdown. They add that loss of leakage efficiency on pumps also affects filter service life.
“So, we can see that there is a complex interplay going on, and one of the big drawbacks in the historical approach to condition monitoring has been seeing factors in isolation rather than as a whole.
“Often, I hear someone say that the particle count is elevated but filter service life has not decreased. This means that either the filter is in bypass or that a particle counter is reading incorrectly. If you take these factors in isolation, you can obviously arrive at erroneous conclusions and get a misleading picture of what is happening within the system.
“And since the oil is already heated, the oil is exposed to the atmosphere, particularly oxygen. If contaminants are present, then obviously the degradation or depletion of service life can be further accelerated.”
Methods of condition monitoring
Numerous methods exist for laboratory oil conditioning monitoring. These methods include infrared spectroscopy (oxidation marker bands), titration for determination of the acid number, estimation of remaining antioxidant content (ruler), particle counting, and elemental analysis (ICP-AE).
Online methods for measurements of oil properties
Online methods for measurement of oil properties include viscosity, electrical properties (dielectric constant), relative humidity, infrared spectroscopy, and particle counting.
Ultraviolet visible spectroscopy and ASDM for colour analysis
These methods can be expanded to include ultraviolet visible spectroscopy for colour analysis.
"Typically, oils tend to shift to red, meaning they tend to acquire yellowish and brownish colouring as they age. So, we can see a shift in the ultraviolet, visible spectrum absorption to the red, but it’s not typically used,” they said. “People typically fall back to something simpler like ASDM colour analysis, which is simply visual assessment. This analysis tends to be a bit subjective because it’s sometimes difficult to determine a colour.
“Here there’s a tendency to not bring all the factors together and not to consider the background but rather focus on the actual signal derived from the counter.”
Placement of the particle counter
Placement of the particle counter is also very important.
“If you place the particle counter directly downstream of the filter, obviously it’s going to show you that the fluid is very clean if the filter is working. So, this is one way to make sure the filter element is doing its job.
“Another thing is to put it on the return line so that you can see what is happening before the filter element, how the filter element is being returned to the system, and what is being supplied to the filter element when it’s being returned to the tank, etc.”
HYDACLab deductions
HYDACLab can determine online relative viscosity (around 20%), relative dielectric constant (around 20%), relative humidity (0-100%), and temperature (-25 to +100°C).
Measurement ranges span temperature from -25 to +100°C; humidity from 0-100% (relative humidity); relative change in viscosity (1 to 1000 cSt); and relative change in dielectric constant (1,5,10).
Outputs include two free configurable outputs, standard outputs, switching outputs, and sequential analogue output (4-20mA) of measured oil property values and device status.
Condition assessment: electrical conductivity
In HYDAC’s HFCC laboratory almost 4000 lubricating, hydraulic and isolating fluids have been electrically characterised.
The following trends are known: high temperature results in higher conductivity as does high water content, high TAN, high impurity content, a mixture with more conductive fluids, and ageing oils.
In a digital world, why is value still hard to find?
At all levels of an industrial system there are a number of barriers that make it difficult to...
Machine learning in manufacturing process control: How ARDI enhances operational efficiency
With increasing data availability, machine learning has become a powerful tool in the...
Verifying and Validating AI in Safety-Critical Systems
In the era of AI-enabled safety-critical systems, validation and verification is becoming crucial...