Machine learning in manufacturing process control: How ARDI enhances operational efficiency
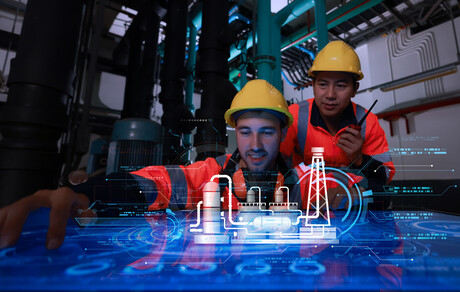
In today’s competitive manufacturing landscape, optimising process control is essential for achieving high levels of efficiency, reliability, and production quality. With increasing data availability, machine learning (ML) has become a powerful tool in this optimisation process. ARDI’s machine learning capabilities provide manufacturers with real-time insights that directly improve production processes, reduce downtime, and boost efficiency. At the core of ARDI’s approach is the ability to consolidate, analyse, and deliver: three principles that drive process improvement and innovation in manufacturing.
How ARDI’s machine learning enhances manufacturing process control
By combining real-time data analytics with advanced machine learning, ARDI integrates seamlessly into existing control systems to optimise manufacturing processes. Below are the three ways ARDI’s Consolidate-Analyse-Deliver methodology transforms operations.
1. Consolidate: Bringing data together for better control
One of the biggest challenges manufacturers face is managing the vast amount of data generated by equipment and systems including historians, DCS, SCADA, and PLCs. ARDI addresses this by consolidating data from multiple sources into a single, unified platform.
ARDI’s consolidation capabilities ensure that all key process variables, along with other data including ERP, shift, maintenance and production data, are easily accessible. This eliminates data silos and provides a holistic view of the production process, which is critical for making informed decisions.
2. Analyse: Machine learning for optimised process control
With the data consolidated, ARDI uses machine learning to analyse in real time. This analysis makes it possible to continuously optimise processes by identifying inefficiencies, predicting equipment failures, and adjusting operating conditions.
Because ARDI analyses data from a wide range of sources, machine learning can be used to reduce variability in the process and improve both precision and consistency for a wide variety of operating conditions. ARDI’s machine learning identifies trends and patterns that traditional control systems and expert systems miss, ensuring optimal process performance under varying conditions.
This capability translates directly into more efficient use of resources, fewer production disruptions, and better overall equipment performance.
3. Deliver: Actionable insights for real-time decision making
The final piece of the puzzle is delivering actionable insights to key stakeholders. ARDI’s ability to provide real-time feedback on production processes means that operators, engineers, and plant managers can react quickly to changing conditions.
In manufacturing, where small deviations can lead to significant issues, having accurate and timely insights is crucial. ARDI delivers this information in a clear and actionable way, allowing teams to improve process control, minimise downtime, and maintain high levels of productivity.
Real-world applications of ARDI’s machine learning in manufacturing
ARDI’s machine learning platform can be used for a wide range of applications in manufacturing process control, including:
- Anomaly detection: Unplanned equipment failures can cause costly downtime, and ARDI can be used to uncover process and equipment performance anomalies to predict equipment failures before they occur, allowing maintenance teams to schedule repairs in advance and extend equipment life.
- Production optimisation: Production efficiency is a major concern in manufacturing, and ARDI can help by analysing production performance, identifying areas for optimisation, which can be used to improve yield and throughput, while reducing costs and downtime.
- Energy savings: In adding to reducing production costs, ARDI can also help manage energy usage and help drive sustainability initiatives.
- Quality control: ARDI’s machine learning can improve quality control processes by detecting anomalies in real time, reducing defects, and improving product consistency.
How ARDI integrates with existing systems
Manufacturers don’t need to overhaul their systems to benefit from ARDI. Whether the facility uses SCADA, PLC, or DCS systems, ARDI integrates seamlessly into existing infrastructure. By consolidating data from these sources, ARDI provides a unified view of operations. ARDI does this without replicating the data, saving on infrastructure and implementation costs.
While ARDI can run in the cloud, it typically runs on-premises to better interact with real-time data and improve security. ARDI is open, flexible, scalable and is vendor independent so it can work with any existing industrial information infrastructure.
Consolidate, Analyse, Deliver with ARDI
In today’s rapidly evolving manufacturing environment, the ability to leverage data for real-time process optimisation is more important than ever. ARDI’s Consolidate-Analyse-Deliver methodology offers manufacturers a comprehensive approach to process control, helping them reduce downtime, improve efficiency, and enhance operational performance.
For manufacturers looking to take their operations to the next level, ARDI provides the tools needed to achieve smarter, more efficient production. Learn more about how ARDI’s machine learning can optimise manufacturing process control by getting in touch with the team at Optrix.
In a digital world, why is value still hard to find?
At all levels of an industrial system there are a number of barriers that make it difficult to...
Verifying and Validating AI in Safety-Critical Systems
In the era of AI-enabled safety-critical systems, validation and verification is becoming crucial...
Transforming industrial processes with AI-based anomaly detection
AI-based anomaly detection is a significant advancement in the quest for manufacturing efficiency...