Remotely manage and protect assets with FactoryTalk AssetCentre
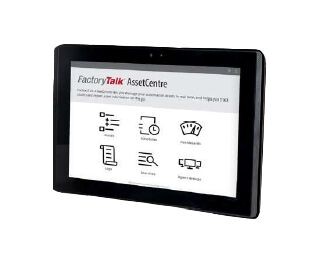
PLC faulted? Quality control issues? Why is production down on the other shift? What is the life cycle status of my automation devices? Who can access my automation devices?
There is a solution to all of those scenarios and more — FactoryTalk AssetCentre from Rockwell Automation provides users with a centralised tool for securing, managing, versioning, tracking and reporting automation-related asset information across entire facilities. It can do all this automatically, with limited additional management or work from employees.
FactoryTalk AssetCentre focuses on awareness across the plant floor and making sure staff have everything they need when trouble arises — all while having a positive impact on productivity, quality, employee safety and regulatory compliance. Its scalable design allows for easy expansion of assets and add-on capabilities, whether it be used for small applications or plant-wide systems. Its integrated and modular design allows for the system to grow as business goals and production needs change.
AssetCentre empowers the user to centrally track and manage configuration changes in a facility while providing secure access to restrict who can perform these functions. FactoryTalk AssetCentre functionality can assist with diagnostics and troubleshooting to reduce the time needed for maintenance of assets. The base server functions include:
- Source control, which leverages the centralised database and provides automatic version control, providing proper file management and single master relationships. Any electronic file can be put under source control — Studio5000, Microsoft Files (.doc, .xls, .ppt, etc), and computer-aided design (CAD) files (.dwg, etc).
- An Audit feature that gathers information generated by user interactions with FactoryTalk-enabled applications, including FactoryTalk AssetCentre. Audits are captured regardless of whether they are connected to the network or disconnected. The audit trail consists of Logged Time, Occurred Time, Source, Location, Resource, Username and Message.
- An Events feature that gathers system-generated information centrally from FactoryTalk-enabled applications, including FactoryTalk AssetCentre. The events log consists of Logged Time, Occurred Time, Source, Location, Severity and Message.
- Reporting capabilities, which allow scheduled or on-demand searches that include traceability information from Audit, Events or Source Control. Scheduled reports can be sent to an email distribution list or, if run on demand (manually), can be saved as an electronic file format of Microsoft Excel, Microsoft Word, Crystal Reports, Adobe or Rich Text Format.
- A Scheduler that is used to run periodic tasks or reports which are assigned to FactoryTalk AssetCentre designated computers (or ‘agents’) to leverage unused or underutilised computing power within the facility and are load-balanced automatically across all agents in an agent group.
- Security on automation systems to prevent unauthorised access to making changes to the system. This is a critical first level in providing a layered security approach. FactoryTalk AssetCentre internally leverages the security provided by the FactoryTalk Services platform that can be integrated into Windows authentication services. This standardised security model minimises efforts to administer users and passwords on operator interfaces, historians, and engineering or maintenance workstations. These security rights are even enforced while computers hosting FactoryTalk applications are disconnected from the network.
- Tamper Detection, which allows the user to configure constant monitoring of their Logix controller for changes. It will detect malicious changes in real time, log activities and generate a report. For example, if a contractor walks up to a panel and connects their laptop to a controller directly via a USB cable, goes online and modifies the program, AssetCentre will be able to capture and report it in real time. AssetCentre can also be configured to send this report to stakeholders via email.
- Integration with Studio 5000 Logix Designer, which provides ease of use for managing versions of controller programs. Users can check out controller programs, make edits, test out changes then check in a new version, adding appropriate comments to document the changes. This is very valuable during system commissioning or after the system is in production.
- The Asset Inventory Agent that allows users to automate discovery and track the status of all connected devices, network switches and workstation computers across an entire facility or product in operation. When a search is run, it not only gives a list of devices but also tracks other pertinent information such as software that is running, firmware revision, vendor name and IP address. Attributes or values can also be manually added to the devices and stored within the FactoryTalk AssetCentre repository to keep a complete picture of all automation assets. When future scans are run, the compare report would list any devices that have been added to the network or any firmware or attribute change that occurred.
- The Mobile Web Client that provides read-only access to the Disaster Recovery Status Dashboard, Asset and Schedule Information and Audits and Events Reports. The dashboard gives a quick view of last search results along with a drill-down capability to gain more insight on failures.
Disaster recovery
FactoryTalk AssetCentre provides control system backup that is integrated with source control to provide reliable and easy access to the latest control system configuration files. The backup system can be configured to provide a comparison of the configuration files retrieved from the plant floor devices with the master file stored in source control. Users can then determine if changes have been made and take appropriate action. For supported devices, a detailed report is available identifying in detail what changes were made. These operations can be performed on demand by the user or on a scheduled basis to best fit operational needs.
The FactoryTalk AssetCentre Starter Kit is ideal for implementation today and prepared for expansion into the future.
For further information on FactoryTalk AssetCentre, please contact NHP Electrical Engineering Products on 1300 NHP NHP or NHPSales@nhp.com.au. In New Zealand: 0800 NHP NHP or salesnz@nhp-nz.com.
In a digital world, why is value still hard to find?
At all levels of an industrial system there are a number of barriers that make it difficult to...
Machine learning in manufacturing process control: How ARDI enhances operational efficiency
With increasing data availability, machine learning has become a powerful tool in the...
Verifying and Validating AI in Safety-Critical Systems
In the era of AI-enabled safety-critical systems, validation and verification is becoming crucial...