Latest evolution in condition monitoring pulls out all stops
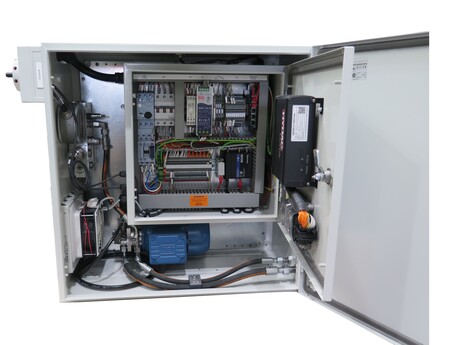
The latest version of HYDAC’s CMExpert hydraulic fluid and system condition monitoring unit, the soon-to-be-released CME-AU2000, brings with it a range of smart sensors, a central data collection system, edge computing, ease of system expansion and the limitless possibilities of MindSphere data analytics.
What differentiates the latest version compared to its predecessor, the CME-AU1000, is its ability take in more information from different sensors that are not necessarily hydraulics-related, according to HYDAC Managing Director Mark Keen.
“There are new sensors coming into the market from HYDAC and other suppliers, which are smart sensors,” he said. “The end result is far more correlated data, enabling understanding of the relationship between pressure and temperature with one sensor, with built-in warnings, as an example. If that is multiplied out by many sensors, there are huge possibilities for understanding what’s going on with a machine.”
He underscores that the series 2000 (Level 2) comes with a central data collection system that monitors itself, automatically interprets data and points out corrective action before it becomes a serious problem.
Wizardry of edge computing
The series 2000 enables HYDAC to integrate edge computing, which comprises a computer embedded into the system to enable much of the processing and interpretation of data to take place locally and not just remotely.
This, Keen says, means that the amount of data that has to be transmitted to the cloud or some other location, is dramatically reduced, taking into account that “a lot of number crunching” is done at a local level.
“We embed edge into the new system with our new Data+,” he said. “This allows us to have multiple inputs with different formats and to execute smart processing of all that input as well as communicate externally as an output.”
He highlights that the edge device’s technical side clearly shows it’s a “very smart little computer with a high amount of storage and a high amount of processing”.
“The magic is that it’s also the Swiss Army Knife of connectivity, enabling reception of signals from different formats. So we look at it as a bit of a Lego set in terms of building solutions for our customers.”
Ease of expansion order of the day
Keen points out that if a client wants to add more sensors or data points he can do that easily without needing to buy a more expensive system.
“Through IO-Link, CAN and Modbus we can bridge anything and then cloud the data with pre-interpreted data as a result of our smart data programming, which avoids redundant and superfluous information, using the power of edge technology.”
The edge device keeps detailed data available, so if a cloud warning comes through it’s possible for a client to examine the detail, receive the necessary information and thereby to react appropriately.
This comes through a cloud dashboard that is “nicely configured” and equipped to show basic information and an overview of “how things are going”. On its right-hand side are all the channels of inputs in a list that enables an operator to drill down for more details on a channel.
Advantages of MindSphere
Keen explains that cloud computing is a standard feature with the series 2000 whereas the series 1000 is available with edge computing. “The MindSphere dashboard comes once you choose the Level 2 package and get cloud subscription,” he said.
He adds that drilling down and looking at historical information is also possible, among many more features and capabilities. Especially relevant is the ability to provide customers with ‘smart’ information around alarms and fault codes to enable decisions as to how alerts will be received for potential malfunctions and to easily determine whether an issue merits attention or not.
Qualified technicians with the correct tools and parts can be tasked to a service job quickly and automatically, taking into account 70% of all hydraulic system failures are directly related to the condition of the fluid and 30% are electrical failures and misuse among other errors.
System connectivity spans levels
System connectivity spans Level 1, 2 and 3. Keen points that Level 1 — focused on oil analysis — has been designed as a base module to allow integration of condition monitoring easily into the system.
HYDAC’s oil condition monitoring Level 1 unit also enables the user to leverage the Level 2 solution. This means that if a user has 10 machines in one factory they don’t need 10 Level 2 units.
“The customer can have nine Level 1s, which are cheaper, and bridge them together to one master Level 2 or Level 3 unit depending on the desired outcome,” said Keen. “So the difference between Level 2 and Level 3 is Level 2 gives a customer edge computing with internet connectivity and Level 3 gives a PLC at a local level to allow added control.”
In a digital world, why is value still hard to find?
At all levels of an industrial system there are a number of barriers that make it difficult to...
Machine learning in manufacturing process control: How ARDI enhances operational efficiency
With increasing data availability, machine learning has become a powerful tool in the...
Verifying and Validating AI in Safety-Critical Systems
In the era of AI-enabled safety-critical systems, validation and verification is becoming crucial...