Worry-free access management for complex machine tool operations
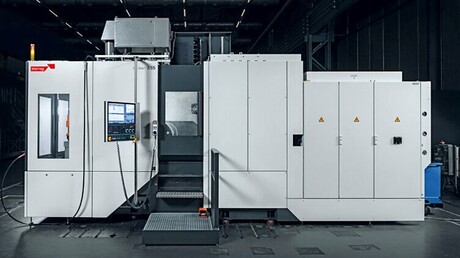
In today’s advanced manufacturing landscape, the ability to switch between different operating modes on machine tools is essential. This capability, however, introduces various risks, necessitating intelligent safety solutions. PITmode from Pilz addresses this need by combining access authorisation and safety-related operating mode selection into a single, compact system.
Modern machine tools, such as those in the Heckert HEC series developed by Heckert GmbH (part of the Starrag Group), perform complex tasks like turning, drilling, and milling. These tasks are critical for manufacturing components like engine blocks and turbine blades, demanding maximum precision and efficiency. However, the need to switch between multiple operating modes for setup, retooling, quality monitoring, and maintenance introduces significant safety risks for operators. Ensuring operator safety while maintaining efficiency is a major challenge.
The key to comprehensive safety
Heckert’s machining centres use 3+2 operating modes in accordance with EN 12417:A2 2009, implemented using the PITmode system. These modes include automatic mode, setup mode (with enabling switch), manual intervention under restricted conditions (with enabling switch), process monitoring (without enabling switch), and service mode (for special requirements).
A special operating mode under ‘process monitoring’ allows for inspection of individual stages, such as machining quality, at reduced axis speed with the safety gate open and without an enabling switch. This mode requires specific qualifications and training to ensure safety, as highlighted by Hans-Jürgen Theileis, Head of Electrical Engineering at Heckert.
The operating and safety concept at Heckert was scrutinised during the update of the Heckert compact machinery. To eliminate operator errors and manipulation, the classic PITmode fusion system from Pilz was enhanced. This collaboration resulted in a holistic entry and access permission management system for safety and security tasks. The system now uses individually configurable keys with personal, manipulation-proof access and operating rights, along with clear rules on who can access specific machines and process data.
The complete, downward-compatible solution for safety and security tasks consists of the PITreader read/write unit with RFID technology and integrated web server, plus a safe evaluation unit. This combines the reader, keypad, and safety controller. In conjunction with the PIT oe 4s operation element and the PIT oe USB data interface, which can be activated depending on permissions, the enhanced solution sets new standards, particularly in security. Via software on the PC, Starrag can now create user-based generic keys and assign personalised codes. As a result, PITmode fusion ensures that when an operator inserts the key, they can only carry out the actions and accesses attributed to them, managing multiple machines with different authorisations simultaneously.
PITmode scales safety according to the risk level of each operating mode. Operators receive ‘machine enables’ that match their abilities, with universal coding to prevent manipulation. This ensures that safety and security are maintained across all operations.
“Our customers receive a unique, all-round impressive state-of-the-art solution for all safety and security tasks,” said Ulf Keiling, Senior Development Engineer at Starrag Chemnitz. “PITmode fusion generates significant added value and will have a positive impact on productivity and plant availability.”
SICK launches Flexi Mobile: The game-changing safety controller for mobile robots
The SICK Flexi Mobile safety controller promises to revolutionise the way AGVs and AMRs navigate...
Hydrogen: Powering the future safely
By integrating functional safety and industrial security, Pilz ensures that hydrogen projects are...
Filling the logic solver gap
There are two widely accepted tools in implementing the logic solver component in functional...