Filling the logic solver gap
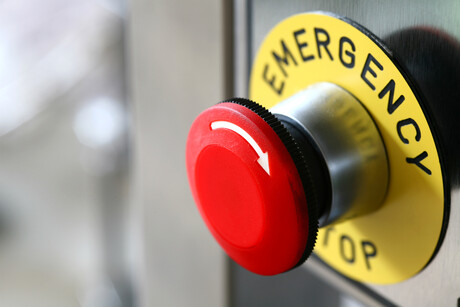
Of the three main components typically contained in a SIF (Safety Instrumented Function), the logic solver is the most critical. The logic solver is responsible for determining whether dangerous conditions have been met and is responsible for the final element’s ultimate effect on the mitigation function or strategy.
Two types of products have become widely accepted tools in implementing the logic solver component in functional safety applications. They are the programmable logic controller, or safety PLC, and the single-loop logic solver. The safety PLC, which is the generic name given to large point-count logic solvers, offers much more flexibility but does so at a significantly higher price and with greater complexity, while the single-loop logic solver is more limited in its capability but can adequately reduce risks and meet safety system requirements with less expense and complexity.
Safety PLCs certainly fill key requirements within functional safety, especially as they relate to large point and loop counts and TMR (triple modular redundant) applications, or where the need exists to sync or network multiple safety logic solvers together to address a complex safety function. Safety PLCs are very capable but come with an extremely high price tag and often require sophisticated programming, maintenance and documentation.
Conversely, there is the fully capable but smaller single-loop logic solver that handles one loop and just a few points. Like safety PLCs these are often IEC 61508 certified but have a much smaller footprint and cost far less than safety PLCs. Additionally, the programming is less complicated and does not require any software licensing.
This is where the logic solver gap lies: functionality, complexity, and cost between these two types of logic solver options are vast. While each certainly has its place, many functional safety applications require just two loops, or three loops with six inputs and six outputs, and perhaps some simple 1oo2 or 2oo3 voting or maths. The safety PLC could certainly handle this, but is it overkill? Alternatively, single-loop logic solvers might be able to handle this with output relay wiring for voting, but point counts are limited and voting architectures can become convoluted with relay inter-wiring.
The Moore Industries SLA Multiloop and Multifunctional Logic Solver and Alarm fills this gap as a less expensive, less complex, multipoint, voting capable and IEC 61508-certified logic solver that allows safety practitioners the option that meets the functionality below that of the safety PLC but above the capabilities of the single-loop logic solver.
With up to seventeen I/O channels, simple voting configuration and enhanced maths/logic capabilities typically found in costly and complex safety PLCs, the SLA can handle everything from simple alarming to complex logic schemes including 1oo2, 2oo3 or even 5oo8 voting architectures. Each of the SLA’s 16 alarms can be configured for High Availability or High Integrity, giving optimal control over shutdown strategies.
The SLA also offers a powerful, flexible, easy-to-use equation/expression editor feature that uses spreadsheet-like formulas and prebuilt functions. An equation/expression editor quick reference is available on-screen to help ensure the quick and easy creation of these equations, or internal variables. Once built, these variables can be used as alarm input sources, analog output sources or even alarm suppression and reset triggers. Additional advanced functions like timers, running min/max registers, and custom curves are also available.
Configured with license-free FDT/DTM technology such as PACTware, the SLA meets a variety of logic solver needs and offers straightforward and quick setup with easy-to-use pull-down menus, checkboxes, and radio buttons.
For more information go to www.miinet.com/sla-pt.
Navigating SIF logic solver selection: Why the Moore Industries SLA stands out
It is important to select a logic solver that is not just well-documented but fully compliant...
Selecting instrumentation for functional safety (SIL) applications
Over the past couple of decades, the process industries have seen many changes when it comes to...
SICK launches Flexi Mobile: The game-changing safety controller for mobile robots
The SICK Flexi Mobile safety controller promises to revolutionise the way AGVs and AMRs navigate...