Bürkert technology for clean processes: a better planet for all
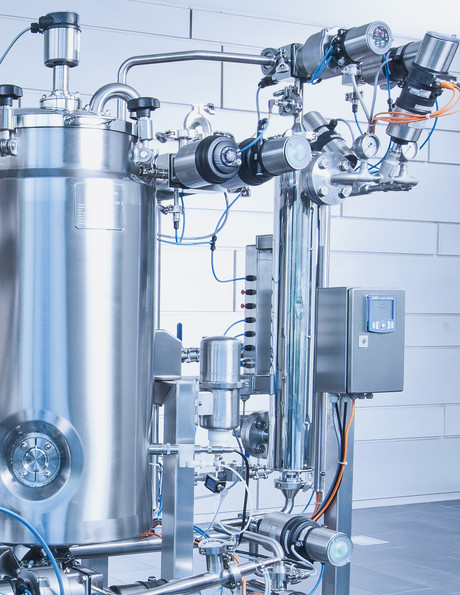
In applications with high standards of hygiene — such as food and beverage production — clean-in-place (CIP) or sterilisation-in-place (SIP) is especially important. All pipes and tubes must be flushed regularly with cleaning agents to remove bacteria, chemical and biological residue, as well as to prevent the spreading of micro-organisms, which can have a negative effect on product quality.
These processes should ideally be carried out with no manual disassembly or active intervention from outside. In addition, the cleaning process must be efficient, to prevent heat losses and also to minimise water consumption.
Traditional forged-body diaphragm valves needlessly consume energy in SIP processes with excessive amounts of costly-to-raise clean steam. They also diminish manufacturing time while heating and cooling slowly in CIP/SIP cycles due to their excessive thermal mass.
Looking towards a sustainable, environmentally conscious solution will not only improve your carbon footprint, but it can also save you up to 54% in your steam rate per valve (with a temperature delta of 100 K). Multiply this energy saving with the number of valves in your plant, and then multiply again with the number if CIP/SIP cycles per year — and now we’re talking about smart savings.
Bürkert’s externally piloted diaphragm valve type 2103 consists of a pneumatically operated piston actuator, a diaphragm and a 2-way valve housing made of cast stainless steel. The tube valve body is robust and rigid: its wall thickness conforms to ASME-BPE 2014, and the hydroformed tube section and the flange are joined by laser welding. Hygienic safety is assured by EHEDG-certified CIP processes and the fact that any media only touches the diaphragm and the pharma tube section — which is identical to the piping elements you are already using in your process. With this revolutionary body, you get access to the most hygienic connection available: tube-to-tube welding.
The design also enables the easy integration of automation modules whether they are electrical or optical position feedback, pneumatic control units or an integrated fieldbus interface.
Best design practices: Creating a high-performance HMI
Creating a high-performance HMI will enhance operator efficiency.
AVEVA Plant SCADA 2020 R2 taps into the full potential of the AVEVA portfolio
When Citect became part of Schneider Electric and then AVEVA, Citect SCADA was integrated with...
Citect SCADA lives on as AVEVA Plant SCADA
Citect SCADA has been a trusted SCADA platform for over 35 years and continues to evolve.