Fumed silica measurement problem solved
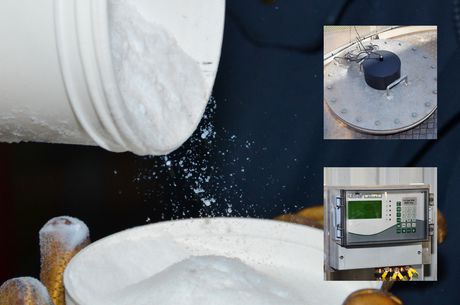
Cabot Corporation is a leading global specialty chemicals and performance materials company headquartered in Boston, Massachusetts, USA. Founded by Godfrey Lowell Cabot in 1882, Cabot’s original business was as an early producer of carbon black. The company built its first fumed silica facility in Tuscola, Illinois, in 1958.
Employing approximately 4500 people worldwide, Cabot’s businesses deliver a broad range of products and solutions to customers in every corner of the globe, serving key industries such as transportation, infrastructure, environment and consumer. It has been an industry leader for more than 130 years in products such as rubber and specialty carbons, cesium formate brines, activated carbon, aerogel, fine cesium chemicals, fumed metal oxides, graphenes, inkjet colourants, masterbatches and conductive compounds.
Cabot Carbon’s plant in Barry, Wales, needed to solve the problem of how to measure the level of fumed silica in a silo. Fumed silica is used as a thickening agent in everything from gel batteries to non-drip paint, as a light-scattering agent in cosmetics and as a toothpaste abrasive. However, it is notoriously difficult to measure with non-content level measurement technologies, having a bulk density of around 30 g/L and a surface area of sometimes hundreds of square metres per gram. A material as light as this presents significant difficulties for bulk measurement.
After a number of failed attempts, including a leading radar system, Cabot Carbon turned to Pulsar’s non-contacting ultrasonic technology to monitor levels in an 11 metre-high silo.
For Cabot Carbon, accurate measurement of the level of the finished fumed silica product in the silo is very important for stock control and to check for tanker loads. A number of approaches had been tried to measure the contents, including radar, but all had failed because of the lightness and absorbency of the product. All non-contacting measurement methods rely on being able to bounce a signal back from a material surface and measure the time taken for it to reach a transducer. Whether that signal is a microwave or an acoustic pulse, the challenge is to supply a signal with enough energy, then discriminate that signal against a background of competing noise.
Pulsar’s approach was to supply its highest power transducer, the dB50, along with an Ultra 5 ultrasonic control unit. With a beam angle of less than 5° (at -3 dB inclusive), which helps to concentrate the power at the target, and a relatively high frequency of 20 kHz, the dB50 is designed to measure up to 50 m, so was putting a great deal of ultrasound energy into the measurement. Even so, the signal that returns to the transducer from the very absorbent silica is very small.
The Ultra 5 control unit features five control relays and offers an optional 4–20 mA input for a pressure transmitter or similar. It includes preprogrammed tank shape conversion for a variety of standard tank shapes, while unusual shapes are also accommodated through a 32-point linearisation function. In the case of Cabot Carbon’s requirements, Pulsar’s latest generation DATEM echo processing software identifies and dynamically tracks the material level, maintaining a link to the true material level even as it changes and other signals from the internal features of the vessel compete.
Jason Jones, Cabot Carbon’s electrical engineer, said, “The Pulsar equipment has cured a headache for us. We were really struggling to find something that worked and was cost-effective, and Pulsar’s kit ticks both boxes.”
Phone: 03 9467 7300
Siemens Sitrans FMT020 transmitter
The Sitrans FMT020 is backwards compatible with existing sensors and offers extended conductivity...
Krohne OPTIBAR FC 1000 flow computer
The OPTIBAR FC 1000 is a compact flow computer for volumetric flow calculation and heat quantity...
Endress+Hauser QWX43 multisensor fermentation monitor
The Fermentation Monitor QWX43 is designed to enable a seamless and simple monitoring of...