Automating the transformer manufacturing industry
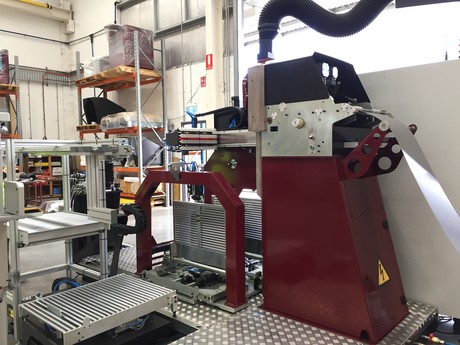
A strategic collaboration between SMC Pneumatics and AEM Unicore has been a catalyst in the success of manufacturing AEM Unicore’s Automatic DUO Core Machine model UCM440A.
SMC and AEM, a South Australian-based company that designs and manufactures special-purpose equipment for the transformer industry, have partnered in the manufacture of AEM’s Automatic DUO Core Machine. The machine streamlines the manufacturing of transformer cores through its key features. Fully programmable for flexible production, the machine produces fully formed half cores and eliminates the need for manual forming. It features a robotic arm and gripper, and an automatically adjustable core stacking and transfer system. It is fully automated and therefore improves productivity, quality and safety. With the ability to run just-in-time (JIT) production, users can enjoy the convenience of compact and lighter cores that do not compromise on quality.
AEM customers also have the additional choice of selecting a double decoiler with remote operation as an option.
The prospect of a partnership was realised when AEM noticed the substantial help and support that SMC was offering right from the inception of the project to manufacture the DUO Automatic Core Machine.
Peter Tedore, engineering design and project manager at AEM, said: “The service and support that we received from SMC exceeded our expectations; they were of more help to us than suppliers had been in the past.”
The complexity of the project brought about challenges in ensuring the compatibility between components of the machine. SMC’s wide product knowledge and offerings were key in enabling AEM to simplify and accelerate this design and selection process.
“One of the most critical components used in this machine is the pivoting linear drive arm,” explained Tedore. “We felt that SMC had a superior product compared to other products in the market. We were impressed with the ease at which SMC products integrated with other control components used. We used EtherCAT for communication and, after we plugged in and set up each component, the system worked seamlessly.”
Jason Sutton, an area sales manager for SMC Pneumatics Australia and New Zealand looking after AEM, said: “SMC wants to work with our customers to know what they need to solve the challenges they face and is always looking at how SMC can improve existing products to help them solve those challenges.”
According to Sutton, the hidden vacuum ejectors used in this project are an example of how SMC offers products that have superior performance compared to existing products. The ejectors are about half the weight of their predecessors, produce twice the vacuum flow and have half the wiring to control.
Another device that stood out for Sutton is the electric drive and linear card motor. The visible vacuum heads that pick and place the laminate sheets are mounted a reasonable distance away from the carriage, which induces a large moment onto the drive. The drive was selected as being able to continuously handle the load at the same time the speed was requested. SMC was able to provide its LEJB63 belt drive with a kit to mount AEM’s selected Beckhoff motor directly. This drive arrangement negated the need for a gearbox to be used.
During the design stage, AEM was unable to accurately measure laminate thickness, as many standard measuring instruments required being physically moved in and out of the measuring area. For the required accuracy of 1 µm, the favoured solution was to be a laser measuring tool. In response, SMC suggested using its linear motor as it could provide 1.25 µm accuracy, 20 mm of displacement and some clamping force at the point of measurement to increase the repeatability. Compact controllers with easy-to-use interfaces made for effortless integration.
AEM has delivered and commissioned three Automatic DUO Core Machines in a transformer core production facility in the USA and three more machines are currently in production.
Phone: 1800 763 862
SICK W10 photoelectric proximity sensor
The W10 photoelectric sensor does away with slide switches, potentiometers and rotary knobs by...
ABB IRB 7710 and IRB 7720 robots
ABB Robotics has expanded its modular large robot range with the introduction of the IRB 7710 and...
Siemens Simatic S7-1200 G2 controllers
The Simatic S7-1200 G2 controllers offer higher communication performance and more efficient data...