The next evolution of process wiring
By Mark Dietzsch, Business Development Manager Process Automation & Custom Connectivity, Turck Australia
Friday, 01 September, 2023
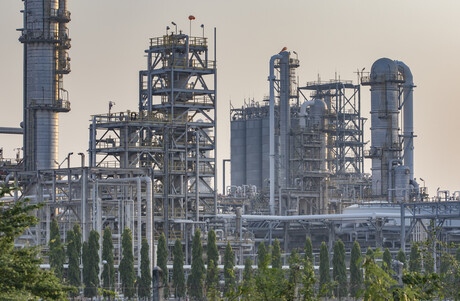
Process wiring in hazardous and non-hazardous process areas has been rigid for a very long time now. Rigid conduits, rigid seals, and a rigid belief in blindly doing things the way they have always been done. Quick disconnect, while very popular in factory automation, has not had much traction in this field, but times are changing.
Wiring and installation of process controls and instruments in the field can be complex, fiddly and challenging. It is a task that must be done correctly, because if errors occur the consequences can be catastrophic. There are many typical issues that can occur during installation.
Bad seals can result in the ingress of water or condensation into conduit, fittings, devices, splices, etc. This can result in intermittent faults or short circuits. Poorly formed or unsafe seals can also allow hazardous gas to pass through, creating an unsafe environment.
Improper or incorrect interpretation of the grounding of cables and shields can create ground loops, stray currents, noise and interference all of which can cause multiple issues, including compromising the integrity of analog signals.
With manual wiring mistakes can occur, and these can result in the incorrect wiring of conductors. This can result in damage to equipment, system failure and an unsafe installation. More minor mistakes, such as loose wires or stray wire strands at wire termination points, can cause the same issues.
If screw terminals or hold-down screws are inadequately tightened this can result in difficult-to-trace intermittent faults, arcing and open circuits.
One of the major problems with all these pitfalls is that the current rigid connectivity system is very difficult, costly and time consuming to troubleshoot and repair. Large portions of the wiring need to be broken down and redone and this, of course, creates the potential for introducing a new issue, or having the same problem occur again.
If all these potential pitfalls are avoided and everything is done correctly, then it can still be very hard to access and calibrate the equipment once it is in place.
End of life or damage-caused device replacement, when the need occurs, becomes another major task and the potential hazards must be avoided all over again.
So, what is the solution? Turck’s ultra-robust Minifast Extremelife cordsets, receptacles, junction boxes and accessories have been designed to withstand the harshest conditions found in the process automation world. Their moulded connectors and gas blocking cables are factory sealed and tested so they can simply and easily eliminate all the above pitfalls while reducing installation time and cost. They also cut down start-up time and facilitate faster and more efficient maintenance.
Quick-disconnect cordsets offer an alternative method to traditional rigid wiring of conduit and fittings and they can be used in any industry, both in hazardous and non-hazardous application areas.
Turck’s Minifast HD Extremelife cordset offering carries four different hazardous location approvals and is the first of its kind to offer an ATEX and IECEx approved solution in a complete cable assembly package. For exporters and multinationals this creates a globally accepted connector solution for hazardous location applications. Additionally, this product offering includes approved mating receptacles, junction boxes and Lokfast guards, and it also makes calibration of instruments much easier. Typically, traditional ATEX and IECEx connector solutions are very complex and expensive field wireable devices, but the Turck Minifast HD offering provides the convenience and reliability of a comprehensive connector solution at a much lower cost than current products.
Minifast IECEx products for Zone 2 are significantly different to standard process wiring products and they carry a II 3 G Ex nA IIC T5 Gc approval issued by FM Global. They include male and female cordsets and receptacles, stainless steel body and coupling nut, are available in 2-pin to 19-pin configurations, are straight only, unarmoured only, and have standard coupling nuts with Lokfast guards. The Lokfast guards used in Zone 2 render a quick disconnect connection not ‘normally arcing’ by making disconnection without a tool impossible. While they are in place they eliminate access to the coupling nut. They also carry a warning notice to the user advising them to disconnect power before removing the guard.
Turck’s Extremelife XL60 cables have exceptionally tough jackets that meet the requirements for armoured cables without having the armour. The basic ITC is already a premium cable. The requirements dictate a very rugged, highly flame-retardant cable. Extremelife cables meet this and are both ER (exposed run) and DB (direct bury) rated. The crush and impact requirements for ER cable are quite difficult for unarmored cable to meet. In the crush test the cable is crushed 10 times between a flat plate and a 20 mm steel rod. The average force to produce an electrical short must exceed 450 kg. In the impact test the cable is impacted 10 times by a 4.5 kg ball dropped from 500 mm and at least eight impacts must produce no electrical shorts.
Turck’s process wiring solutions can provide many benefits. They save valuable time on install and startup, they limit the potential for dangerous mistakes, there are no messy and labour-intensive seals to deal with and they enable quick replacement and return to operation when a device reaches its end of life. Not only that, but the reduction of manual tasks will provide increased human safety benefits and the use of quick disconnect fittings on panels allow those panels to remain locked during transit. This provides increased safety and enables a fast and simple plug-and-play installation process.
There are also many other Turck products for hazardous and non-hazardous process automation applications. Excom is the only universal remote I/O that can be installed in Zone 1/21, Zone 2/22, and C1D2 or in the non-Ex area. The system can communicate via Profibus-DP, ProfiNet, EtherNet/IP and Modbus and the field circuits are approved for Zone 0 and C1D1. Turck also has products for use with Foundation Fieldbus and HART.
Turck’s process wiring solutions offer safer installation and provide a lower bottom line for contractors, who can do more jobs in less time. They reduce installation time and startup time and they make calibration and fault finding easier. Instruments can also be prewired prior to installation.
For convenient, cost effective and safer process wiring solutions it is time to leave the rigid past behind and embrace the future.
Seamless modular I/O integration
For seamless modular I/O integration, WAGO controllers combine with WAGO's I/O System 750 to...
LAPP Australia introduces ultra-reliable Wieland Electric wipos power supplies to Australia
Power supplies perform a central function in the control cabinet, so a robust and proven design...
Drive the future of transportation with SCHURTER
SCHURTER offers solutions for various applications in the automotive industry: our products...