Drive the future of transportation with SCHURTER
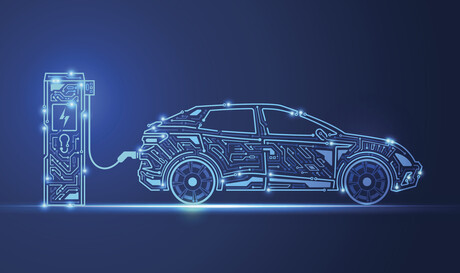
According to market research, electrified vehicles are overtaking the automotive industry, with EVs expected to account for half of all cars sold globally by 2035. Most EVs on the road are two- and four-door passenger vehicles. However, larger commercial and public transit vehicles are being electrified as charging and energy storage technology continues to evolve. Large commercial EVs like long-haul trucks, city and interstate buses, and delivery vans operate more often and for more extended continuous periods than passenger EVs and require larger batteries with more complex charging infrastructures.
The battery is the main element of an electric vehicle: More cells provide more charging capacity, which means longer distances to travel before needing a recharge.
Charging speed plays a decisive role. With fast charging, the alternating current is converted directly into direct current at the charging station. The DC converters used in this process must be as efficient as possible in order to minimise energy loss. However, more efficient DC conversion also means higher electromagnetic emissions. The attenuation of these emissions is of central importance, as they must not be allowed to enter the power grid or the connected electric vehicle as interference signals. Insufficiently attenuated signals can interrupt the communication protocol between the charging station and the vehicle. In the worst-case scenario, this can even lead to defects in the vehicle. SCHURTER offer various products for use during the charging process.
Battery balancing is a key technology to ensure the safety of the charging process
Given the installation of thousands of such batteries in electric vehicles, the charging process is crucial, and the batteries must be charged in as short a time as possible. The solution to this challenging task is called "battery balancing." This refers to an electronic circuit (often part of the BMS) that ensures even charging of the battery pack's individual cells. Due to manufacturing differences or varying usage conditions, slight electrical characteristic differences may exist among these cells. This can result in some cells charging or discharging faster than others, causing voltage or capacity imbalances. "Battery balancing" is the process of uniformly charging the battery pack.
Customized fuses
However, the biggest enemies of battery packs are overtemperature, short-circuits and pulsed overcurrent. Depending on the design and purpose of the high-performance battery pack, the focus must be placed on protection against overcurrent and/or more on temperature. In most cases, however, several potential problems come together at the same time. In practice, this means that customized solutions are required for protection. Possible — and already implemented — are pulse-proof combination fuses for protection against overcurrent and overtemperature. This is done using chip technology to ensure the necessary mechanical resistance. Maximum power density with maximum safety and longevity: this approach applies not only to the individual cells, but to the entire energy unit.
Taking the SCHURTER UMT 250 series fuse as an example, it is a surface-mount (SMD) fuse with dimensions of only 3 x 10.1 mm, supporting 250 VAC and 125 VDC, and it is an SMD fuse that operates in the range of 80 mA to 10 A. The fuse is designed with a compact form factor to minimize footprints while maximizing its breaking capacity. It is suitable for pulse-shaped continuous currents.
Safety requirements for components in the automotive industry
AEC stands for the Automotive Electronics Council, an organization based in the United States that focuses on the standardization of the qualification of electronic components in the automotive supply industry. The Q200 standard, introduced in the mid-1990s, outlines requirements for passive components, while the Q100 standard and its derivatives focus on active components. These AEC standards are globally recognized and accepted by all leading manufacturers in the automotive industry.
The development of the AEC-Q200 standard aims to ensure the reliability and durability of automotive electronic components under extreme environmental conditions. The internal environment of automobiles imposes stringent requirements on electronic components, such as high temperatures, low temperatures, vibrations, humidity variations, and more.
Reliable and accessible EV charging to all
SCHURTER offers solutions for various applications in the automotive industry: in addition to a safe power supply during the charging process for electric vehicles, our products ensure protection of the battery, the inverter for the motor drive and the air conditioning systems, protection of the ignition system and emergency power supply as well as the provision of intuitive operating elements. The close networking with international automotive organizations and the industry itself make SCHURTER a competent partner for all questions concerning the protection of electronics in automotive engineering.
Get to know our products for the various charging processes. Determine the best EMC and HMI components for your project. Visit SCHURTER Automotive: https://www.schurter.com/en/markets/automotive.
Originally published here.
Seamless modular I/O integration
For seamless modular I/O integration, WAGO controllers combine with WAGO's I/O System 750 to...
LAPP Australia introduces ultra-reliable Wieland Electric wipos power supplies to Australia
Power supplies perform a central function in the control cabinet, so a robust and proven design...
The evolution of SEW-EURODRIVE decentralised drive technology
MOVIMOT advanced integrates a motor with a new decentralised inverter covering a power range from...