Mechatronics service you deserve
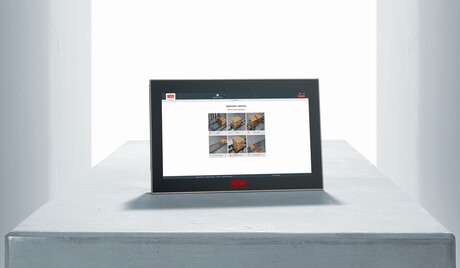
In process industries, where production downtime leads to increased outlays and lost opportunities, reliable manufacturing equipment backed by high-end service and support is critical to business success. Businesses that rely on mechatronic drive technology to keep their production lines moving offer a prime example of this principle in action.
Whether in food and beverage, mining, recycling, or at a parcel distribution centre, these businesses, and others like them, know that service and support offerings need to be all-encompassing if they are to create a competitive advantage. The process begins with knowledgeable sales and engineering assistance to devise an optimum solution, and continues for the life of the product with ongoing support and maintenance delivered by service and repair teams.
If a production line is down, it can be very expensive. To help mitigate that risk, the SEW-EURODRIVE team provides 24/7 breakdown service and support for its mechatronic products from well-equipped service and support centres in Perth, Adelaide, Melbourne, Sydney, Mackay and Brisbane.
All the service and support facilities are well-stocked with spares, so if a client has an issue, all it takes to initiate repair or replacement is a phone call — at any time of the day or night. As soon as the caller quotes the details of the affected unit, the support team swings into action.
Quick turnaround
The modular nature of the units and SEW-EURODRIVE’s heavy investment in holding spares mean the support team is generally able to build a replacement unit and have it ready for dispatch in a short time. This ability to quickly turn around service and repair jobs has proved crucial in the quest to set up a network of service and support centres that save clients time and minimise their costs.
Additional capabilities at key service centres cater for local requirements. The Mackay centre, for example, offers a unique load-testing facility that provides enhanced testing. Load testing of up to 500 kW power and 600,000 Nm torque is available. There is also provision for spin testing or partial load testing up to 1.5 MW. The facility has become the gold standard for servicing large industrial mechatronic products in Australia. It is set to be duplicated in Newcastle, in an expansion program due for completion by early 2022.
Experts on hand
Because of the importance of service and support, assistance is available around the clock. This includes weekends and public holidays, and applies to all product types.
The 1300 363432 after-hours telephone hotline caters to breakdown needs, with both mechanical and electrical specialists on call to answer queries and provide advice. If the problem can be solved on the spot, it will be. But the person who takes the call always has access to additional expertise if it is required.
This approach reflects SEW-EURODRIVE’s philosophy of centralised assembly and decentralised support, backed by high-quality German engineering design and practices. Technical expertise is in place at the local level, with all the service centres staffed by knowledgeable and experienced people. However, the collective knowledge and creativity of the entire global team is always available as well.
Team approach
In daily practice, the service and support team is made up of several departments. This layered and integrated structure means that approximately 40 sales and engineering people available to the service team nationally.
In the first instance, sales staff assist clients with an appropriate selection and configuration of mechatronic drives to fulfil their needs. If necessary, the engineering team then refines the design by calculating correct drive performance, the sizes of units and frequency inverters and other accessories. Once the design is optimised and the equipment is delivered, the installation and commissioning team is available to assist on site.
After commissioning, the support continues, with maintenance and repair available for the life of the product. In some cases, the ongoing support occurs overseas, taking advantage of SEW-EURODRIVE’s global network of integrated support centres and manufacturing facilities. This often occurs when OEMs purchase equipment in Australia for use in export projects. In this case, the OEM installs the equipment overseas and then uses one of the nearby offices for support services.
Significantly, the high level of service and support expertise is not confined to SEW-EURODRIVE’s own products. Recognising that many client facilities have a mix of legacy equipment and current products, the service centres are able to repair a wide range of mechatronic devices made by other manufacturers. Staff at the centres are trained in many different products and have the ability to service and repair the majority of units from most well-known manufacturers.
Predictive maintenance
Good support means much more than simply providing a repair service. Planned maintenance is intrinsic to the process too. As part of this, attention is fast being turned to the emerging art of predictive maintenance.
Built-in sensors convey information that enables digital recording and analysis of the operational data of industrial gear units. Information regarding oil temperature, vibration, motor temperature, motor current and similar is received, and further analysis enables prediction of changes in condition and other maintenance-related events.
Used in this manner, the developing and upcoming DriveRadar technology allows operations managers to optimise and plan maintenance and repair activities for their drives. Similarly, the monitoring of key parameters enables them to observe trends and see any unusual results. This helps avoid potential system failures.
Online support
Much of the support is now available online. With the appropriate permissions, quotes and current orders can be tracked, and ordering history can be viewed. For installed equipment, CAD files, installation manuals and operations manuals can also be retrieved. The recently added Drive Selection Tool provides a guided means of determining a suitable drive combination based on user entered application parameters. Based on the selected combination the user can request to receive a quotation.
This level of convenience is set to be augmented in 2022 with the increased use of QR codes. The codes are being printed on the units’ labels. Scanning the code reveals a wealth of information about the unit, including data and documents, spare parts ordering, and troubleshooting. Should further assistance be required, the appropriate contact number is also provided so that the local service centre can be called.
The trend towards increased online support from SEW-EURODRIVE also extends to training. The company’s Drive Academy provides online training for a diverse range of activities, including optimised maintenance, programming of devices and troubleshooting. Plans are afoot to add drive selection and configuration in the future.
This steady stream of innovations, ranging from online services and training to enhanced physical testing facilities, reflects a strong, ongoing commitment to service and support. Continually raising the bar in this manner offers improved performance and savings for any business that uses mechatronic drives to keep its operations running smoothly.
Seamless modular I/O integration
For seamless modular I/O integration, WAGO controllers combine with WAGO's I/O System 750 to...
LAPP Australia introduces ultra-reliable Wieland Electric wipos power supplies to Australia
Power supplies perform a central function in the control cabinet, so a robust and proven design...
Drive the future of transportation with SCHURTER
SCHURTER offers solutions for various applications in the automotive industry: our products...