Decentralised drive to success
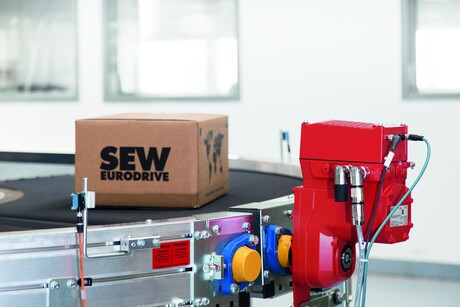
Osem Jibrail, Industry Manager at SEW-Eurodrive, discusses how developments in the company’s mechatronic drive systems and modular platforms make it possible to tailor exact solutions for each operator’s needs.
What are the key developments in the new generation of SEW’s decentralised drives?
Some common key hypotheticals that many end users, OEMs and project managers come across when implementing brownfield and greenfield drive installations are:
- Looking for a drive system that does not require time to setup
- Getting a benefit from significant reduction in drive variants
- Needing to reduce power supply, power distribution systems and the size of installed base
- Needing to keep track of multiple mechanical and electrical configurations in site installations
Over the past 10 years, SEW Eurodrive has pioneered new levels of efficiency, reliability and serviceability in conveying applications — meeting the usual objectives of reduction in total installed power, audible noise and vibration while extending the service life of the associated electrical and mechanical systems, all of which contribute to key reductions in total cost of ownership.
Benefiting all stakeholders involved, this can be attributed to the use of SEW Eurodrive’s modular Movimot Flexible and mechatronic Movigear drive systems; ensuring stable and sustainable material conveying within industries including, logistics, airport, food and beverages. By decreasing the number of installed variants and consequently a reduction of mechanical complexity, the potential for machine downtime, cost of repairs and spare inventory is greatly diminished.
Are you using the right solution for your application? Or are you using a legacy generic solution?
Our ongoing consultations with operators have led us to develop measures to ensure a more efficient maintenance plan for each drive system, further mitigating unpredicted downtime by utilising the enhanced drive capabilities. SEW Eurodrive’s new decentralised and mechatronic drive systems address this requirement by introducing a digital interface between the motor and frequency inverter (digital motor integration). This allows the direct integration of each drive into higher-level networks and makes it possible to gather information on energy consumption, machine utilisation, temperature and other operating data in unprecedented detail. Specific information on service life for wear parts, belt slip or vibration will also be possible in the future. Providing operational and service related metrics and reporting is now easily achievable via existing IT or machine network interfaces, geared for the relevant user base.
This, combined with the benefits of the previous generation, SEW Eurodrive’s scalable motor technologies and the ability to either motor integrate or remote mount the inverter, ensures the new portfolio of systems are designed for conveying demands of today, tomorrow and beyond.
How flexible are the new drive systems?
As the new system is based on the modular Movi-C automation platform, it has a remarkable degree of flexibility in all aspects of its operation. To start, interfacing the local system with higher-level controls is possible through everything from a simple binary control up to a high-performance, fully integrated industrial Ethernet. SEW’s technology also makes it possible to develop application-specific solutions for precise Ethernet fieldbus control that don’t compromise on efficient strategies for installation and start-up time.
Similarly, the system allows a high degree of scalability in electromechanical design and performance, covering everything from a standard asynchronous motor or gear-motor, up to a high-performance highly efficient permanent magnet motor-based mechatronics application drive.
On top of that, it’s simple to put together a system for either motor-integrated or remotely-installed drive electronics without requiring different components. Operators can also customise their system with modules dealing with local motor operation, including local display of process values and drive status, for instance.
How do SEW’s systems contribute to energy- and cost-efficiency?
The scalability of the Movi-C platform, and the way we optimise the selection process for each part of an installation allows us to meet the customer demands to suit each project. We focus on the ideal way to use each component, thus minimising physical footprint further contributing to an overall reduction in initial project cost and also the cost of ownership during its lifetime.
How does SEW technology enable monitoring of operation data and predictive maintenance?
Connecting the dots between a single motor/inverter/drive system, and the operational integrity and profitability of a factory has never been easier!
DriveRadar is our concept for providing an end-to-end digital operations map that gives customers a detailed insight into drive components, system solutions and processes. The aim of DriveRadar is to determine the status of products, machines and systems by using existing data that is collected by SEW systems during operation. Cutting-edge data analysis with machine learning can be used to accurately predict imminent damage by modelling a digital twin system. This means DriveRadar can prevent otherwise unforeseen failures and inteerferences in operation, detect wear and minimise downtime.
To be successful, DriveRadar requires the installation of smart and connected products able to collect the relevant information. The new Movi-C platform of decentralised drive systems is totally integrated and connected. Therefore, it’s one of the most important steps on the way to making conveyor systems more transparent and predictable, and, ultimately, optimising operations in various industries.
For further information go to www.sew-eurodrive.com.au.
Seamless modular I/O integration
For seamless modular I/O integration, WAGO controllers combine with WAGO's I/O System 750 to...
LAPP Australia introduces ultra-reliable Wieland Electric wipos power supplies to Australia
Power supplies perform a central function in the control cabinet, so a robust and proven design...
Drive the future of transportation with SCHURTER
SCHURTER offers solutions for various applications in the automotive industry: our products...