Connectivity design tips and considerations for harsh environments
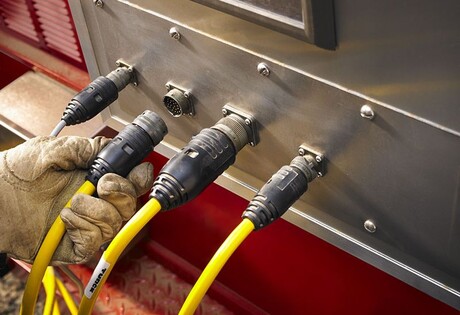
Connector and cable designs have evolved as connectivity manufacturers keep pace with user and application demands. From innovative overmoulded solutions to stainless steel potted connector bodies, today’s products improve performance and are more convenient than traditional field-assembled connectors.
Factors that affect connectivity performance
A number of factors influence how a connector or cable solution preforms in an environment. Material selection and chemical compatibility are two leading criteria because they can directly affect the integrity of the solution for a specific application.
Plastics are the primary material used to protect connectors and cables from the elements of harsh applications. The plastic material that is used has a critical impact on chemical compatibility, and variations have been developed for specific uses (see Figure 1). For example, certain materials can withstand very cold temperatures without cracking, while others resist high temperatures that would compromise another plastic’s integrity.
Overmoulded connectors are recommended for demanding applications because of their reliability and robust construction. These solutions are more than simple plastic housings: instead, they insulate and protect all the connection points between the cable and the connector against ingress. These fully-assembled products are also factory tested and provide ease of installation and improved performance.
With the different plastic material options available, there are overmoulded connector solutions to withstand most chemicals in harsh applications. However, some applications can be so demanding that a plastic overmoulded body may not offer enough protection.
For these applications, there are connector options that utilise a stainless steel housing filled with potting material. This type of solution provides improved mechanical strength and can still hold up well in applications with highly caustic chemicals. There are also versions of this connector that allow for additional hazardous location approvals. With stainless steel connector bodies, grade 316 stainless steel offers the best option for durability in harsh industrial environments: grades 303 and 304 can be more susceptible to corrosion with highly caustic chemicals.
Once materials and chemical compatibility are taken into account, engineers can review the next layer of specifications: ingress protection, vibration, operating temperature and pull strength.
Ingress protection
Ingress protection ratings, commonly referred to as IP ratings, demonstrate a product’s ability to resist environmental pollutants like dust and water. Engineers should look for a minimum of IP65 protection on cables and connectors used in harsh applications. This ensures no penetration of dust or water jets. IP69K is the highest level of ingress protection offered, ensuring protection against dust and water at high pressure.
Vibration issues
Vibration can threaten to disconnect the coupling feature of a connector and disrupt data transfer through the connector. To withstand this hazard, the design and quality of connectors, contacts and cable is critical.
To prevent a connector from coming loose, the connector design must have special features that maintain engagement even at high shock and vibration. The contact design must prevent the mating interface from intermittent connections or damage by vibration. The contact materials and plating are another critical element for strength, durability and electrical performance. Some criteria to look for in the most robust connector and cable products include:
- Machined contacts, instead of stamped or formed, for better performance
- Gold plating, instead of tin plating, for better electrical properties
- High-stranded wires, instead of solid wires or minimal stranding, for best cable flexibility
Temperature challenges
The temperature of an application can affect performance if the right material isn’t in place. Extremely cold temperatures can crack cable jackets or plastic connector bodies, and some materials will break down over time in very hot environments. For the best-fitting solutions, look for connectors and cables with rated optimal temperature ranges that meet those of the application. Don’t forget to take into account potential issues caused by fluctuating temperatures.
Pull strength
Cables and connectors can experience a lot of force in industrial environments, from getting bumped during operation to serving as improvised step ladders. A product’s pull strength indicates how well a connector will hold up to these forces. A good bond between the plug body and cable is one indicator that a product is likely to exhibit strong pull strength. An additional feature to look for is that the back of the coupling nut is extended over the connector’s plug body. This allows any angular forces to be absorbed between the plug body and coupling nut, and not directly on the wire to contact terminations.
Improving connectivity for mobile equipment and oil and gas applications
Advances over the past few years have transformed commonplace Deutsch connectors into robust overmoulded solutions that stand up to vibration and ingress. These can be used outside the cab to improve connectivity where moisture and the elements have historically caused repeated failures.
They’re also protected during cleanup and washing. Vibration issues can also be solved through correct installation. If connectors and cable aren’t mounted properly, they can end up floating as machinery runs, leading to connection failures.
Oil and gas applications face similar outdoor environmental challenges as mobile equipment, but also involve caustic chemicals in drilling muds and the potential need for hazardous location approvals.
Hazardous location approvals ensure a product is safe to use in hazardous locations. Oil and gas companies are increasingly looking for more international approvals to ensure global safety compliance and streamline product inventory. For example, a cordset with both ATEX and IECEx approvals can be specified for use not only in North America, but across Europe and other continents. Related to ATEX and IECEx connectivity products, field-assembled solutions are still most commonly found in process automation and oil and gas applications; however, some manufacturers now offer fully assembled cable solutions. Because all elements come assembled and factory tested, the products reduce the risk of miswiring while also accelerating installation time and reducing labour.
Tips for finding the correct connectivity solution
When sourcing a connectivity solution, a supplier will ask a series of questions like the ones below to better understand the application and how it may affect a connector or cable:
- What chemicals are present, and at what percent dilution?
- How exposed will the product be to these chemicals, and how often? Will the product be submerged, splashed or wiped down?
- Are explosive or hazardous gases or vapours present?
- What temperature or temperature range is typical?
- Will the cable flex?
- Is vibration and shock a factor? What frequencies or g-forces will be seen on the connectors?
- Are there opportunities for impact on the cable or connectors?
- What’s the current and voltage?
- Is this an indoor or outdoor application? Are sunlight, UV or water exposure possible?
- What IP ratings are required?
Conclusion
When it comes to choosing a connectivity supplier to solve applications in harsh environments such as mobile equipment and oil and gas installation challenges, look for solutions that offer the rugged construction, approvals and flexible cable jacket required in these demanding environments. All of these attributes combine to bring a connectivity solution that will result in less downtime and more cost savings in a fully compliant offering. Consult your local connectivity expert at Turck with all your harsh environment connectivity needs.
Seamless modular I/O integration
For seamless modular I/O integration, WAGO controllers combine with WAGO's I/O System 750 to...
LAPP Australia introduces ultra-reliable Wieland Electric wipos power supplies to Australia
Power supplies perform a central function in the control cabinet, so a robust and proven design...
Drive the future of transportation with SCHURTER
SCHURTER offers solutions for various applications in the automotive industry: our products...