Z Energy sets the standard in safe fuel transport and storage
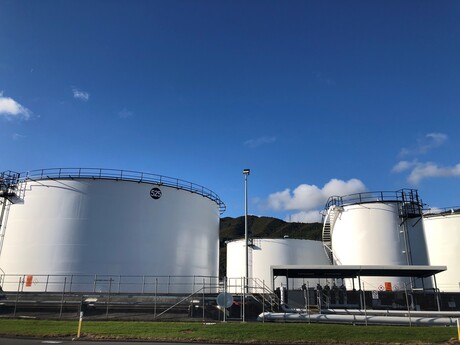
Leading-edge safety system helps meet compliance and improve safety.
Fuel transportation, storage and handling is a highly regulated industry that could result in serious consequences if a safety incident were to occur. Meeting these stringent safety requirements is a key priority for businesses that transport and store fuel.
Z Energy is a New Zealand company that supplies fuel to retail customers and large commercial customers including airlines, trucking companies, mines, shipping companies and vehicle fleet operators. Their safety system drives them to proactively focus on the risks that matter most and helps to ensure the continual improvement of their operations.
With a strong commitment to safety and sustainability and to meet the new requirements resulting from the Buncefield incident in the UK, Z Energy recently implemented an innovative automation and safety solution to avoid overfilling their fuel storage tanks while also providing safety function monitoring.
Z Energy called on Pilz for their safety and automation expertise to deliver this turnkey project. A project of this importance would require high-level integration capabilities to meet its unique requirements, so Pilz called on their Authorised Systems Partner, DRE Systems, for this implementation.
Scoping the project
Z Energy transports offshore fuel to their tank farms, which can be many kilometres away from the original location. The scope of the project was to install an automated system that monitors the level of the storage tanks to avoid overfilling. If the fuel level was to exceed the safe limit, the safety system would then automatically shut down the site and close the valves on the storage tanks.
“Prior to the upgrade, we were relying solely on radio communications between the boat and the receiving tank but if that communication were to be interrupted or break down there would be a high likelihood that we could overfill the storage tank which would then cause significant issues onsite,” said Duncan McIntyre, Project Engineer, Z Energy.
“Although we can halt the product movement coming into our site, it poses a risk in that the ship may not be aware that we have stopped receiving the fuel and they can continue pumping, which could then lead to a pipeline fracture which would be a major failure for us,” he explained.
To address this, Pilz and DRE Systems designed a SIL 2 safety instrumented system involving safety PLCs communicating via radio. Providing a safe automated solution removes the human factor ensuring that in the event a high limit is detected within the tanks onsite, signals are sent to the berth automatically. This sends alerts via alarms, lights and sounders for the wharf staff to attend to the system.
The challenge of the distances and terrain involved at the Seaview site required an innovative approach to the solution. DRE Systems was tasked with solving the site-specific challenges.
Flexible and adaptable safety
The SIL 2 solution was based on the Pilz PSS 4000 safety PLC system, which is highly configurable with the SafetyNET p protocol. DRE researched and discovered a local supplier of state-of-the-art Ethernet radio links for industrial use. 4RF were able to provide their hardware and expertise to develop a reliable communication link.
“With this safety integrated system, the compliance is largely performed through the documentation, which provides flexibility in relation to how the solution is delivered. Using the SafetyNET p protocol, the PSS 4000 safety PLCs can be configured to communicate at different transmission rates, whether it is 10 milliseconds or 30 seconds, depending on the application,” said Tony Catterson, New Zealand Manager, Pilz.
“The ability of the PSS 4000 to work with variable transmission rates made it the natural choice when selecting the control technology. This allowed the use of radio communication between the wharf and the terminal with a range of up to 300 km. In fact, this application is one of the first in the world to use radio communications for safety — it is not something we have seen anywhere in the industry and is very much a leading-edge solution,” he added.
This modular system provides the ability to control both automation and safety functions, meeting all relevant safety standards. DRE Systems worked closely with Pilz to supply the equipment, build the panels, develop the PLC software and generate the test documentation and commissioning onsite.
“The radio system operates similar frequencies to a handheld system but with safety rated Ethernet communication. For example, if operators need to send a signal to the wharf without intervention within one second, the PSS 4000 PLC communication can be guaranteed to meet these requirements. The robustness of the communication link was critical to the project, even if there was a tanker parked in front — the radio system is able to perform adaptive modulation, where it actually changes its frequency to ensure 100% uptime,” said Dan McNicholas, Managing Director of DRE Systems.
Safe fuel transport and storage
The solution exceeded Z Energy’s project requirements and given the flexibility of the PSS 4000 system, DRE Systems was able to integrate with Z Energy’s SCADA system, external communications and radio signal to the wharf. It eliminates the requirement for human intervention and provides reliable communication to the wharf with safety rated SIL.
The radio system together with the adaptiveness of the Pilz safety and automation system provided the capability for an innovative and robust solution which will now also be implemented at additional Z Energy sites.
Navigating SIF logic solver selection: Why the Moore Industries SLA stands out
It is important to select a logic solver that is not just well-documented but fully compliant...
Selecting instrumentation for functional safety (SIL) applications
Over the past couple of decades, the process industries have seen many changes when it comes to...
Hydrogen: Powering the future safely
By integrating functional safety and industrial security, Pilz ensures that hydrogen projects are...