The importance of emergency stop pull-wire devices
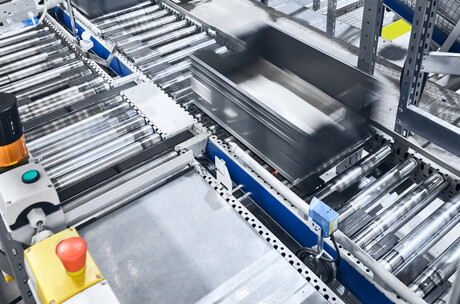
When it comes to emergency stop devices there is no doubt that the red mushroom-head push button is the most common — they seem to be everywhere. The second most common emergency stop device is the pull wire, and like the light curtain in safeguarding devices, the pull wire is probably the most misapplied emergency stop device.
Emergency cable pull switches are designed to provide continuous emergency stop control along exposed areas of machinery and conveyors that present hazards to operators or maintenance personnel. As such, they can fulfill the requirements of having a means of an emergency shutdown at every area where a work-related task is being performed. Unlike isolated E-Stop pushbuttons, emergency cable-pull systems can be actuated at any point along the ‘trip wire’.
Emergency stop pull wires are most often used where there are long stretches of machinery between normal operator stations. As an example, pull-wire emergency stop devices are commonly used on conveyors and other long machines. They can be challenging to install correctly with cable tension and support being extremely important.
Bear in mind that emergency stop systems are complementary protective measures. Complementary protective measures are backup devices to the primary safeguards, and as such they do not provide guarding to protect a person from being hit or entangled and dragged by material on the belt.
The basic idea of an emergency stop pull wire is to provide a person with a way to stop the equipment motion from any place along its length. This same idea is sometimes used when a worker could be present at many points along a piece of machinery, with no explicit workstation defined. Once the trip wire is tensioned, the switch will initiate an emergency shutdown if an operator falls into, is pulled into, or pulls on the trip wire, and will also fail to safe if the cable is cut or goes slack.
Pull-wire systems are made up of multiple components including the switch, anchor points, the cable or rope, cable guides (such as pulleys or eye-bolts), and a tensioning device. Which components are required will be determined by the application. Since the cable is flexible, it can be made to turn corners so that it can follow the work area — which also means a single system can be installed over a large distance. As for the pull-wire switch itself, they are designed so that the switch will activate if the cable is pulled, breaks or is cut. It will also have an indicator to show that the switch has been tripped and there must also be a way to reset the tripped connection. Switches like Schmersal’s ZQ 900-02N come with a built-in push button as a secondary means to trip the switch, in addition to wire pull and breakage protection, position indicator, external watertight collar, and three cable entries. As you can see, there are many important details to the correct installation of an emergency stop pull-wire switch. These details need to be looked after during design and maintenance, and as with any other safety device, there are many ways to do the job poorly. Cable tension, support and guidance are critical to correct operation. |
![]() |
Pull-wire systems are made up of multiple components including the switch, anchor points, the cable or rope, cable guides (such as pulleys or eye-bolts), and a tensioning device. Which components are required will be determined by the application. Since the cable is flexible, it can be made to turn corners so that it can follow the work area — which also means a single system can be installed over a large distance.
As for the pull-wire switch itself, they are designed so that the switch will activate if the cable is pulled, breaks or is cut. It will also have an indicator to show that the switch has been tripped and there must also be a way to reset the tripped connection. Switches like Schmersal’s ZQ 900-02N come with a built-in push button as a secondary means to trip the switch, in addition to wire pull and breakage protection, position indicator, external watertight collar, and three cable entries.
As you can see, there are many important details to the correct installation of an emergency stop pull-wire switch. These details need to be looked after during design and maintenance, and as with any other safety device, there are many ways to do the job poorly. Cable tension, support and guidance are critical to correct operation.
With some care and attention to detail, users can install a system like this correctly without too much difficulty. For more information on what pull-wire switch would be best suited for your organisation, or information on machine safety or specialist training, contact Control Logic on 1800 557 705 or email sales@controllogic.com.au.
Navigating SIF logic solver selection: Why the Moore Industries SLA stands out
It is important to select a logic solver that is not just well-documented but fully compliant...
Selecting instrumentation for functional safety (SIL) applications
Over the past couple of decades, the process industries have seen many changes when it comes to...
Hydrogen: Powering the future safely
By integrating functional safety and industrial security, Pilz ensures that hydrogen projects are...