Chemical plant upgrades safety-critical alarms
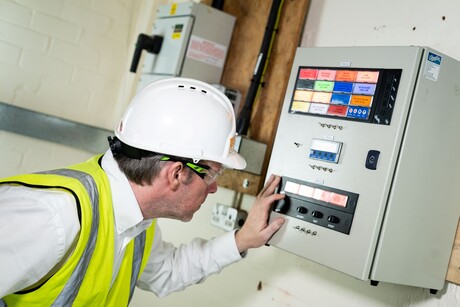
When the Sasol chemical plant in South Africa was first constructed in the 1970s, 21,000 critical alarm points were defined for monitoring by annunciators, enabling the plant to manage and control the production process safety. These alarm points are dispersed throughout the plant, with some as discrete as single 16-point annunciators and other as large as 300-point systems that monitor all safety-critical processes across the site.
However, when the alarm systems, originally supplied by Conlog, reached the end of their service lives, it became necessary to upgrade all 21,000 critical alarm points across the plant on a progressive basis.
Sasol engaged safety-critical alarm specialist Omniflex, which was formed as part of a Conlog management buyout, to provide the replacement systems.
Sasol is South Africa’s largest fuel-from-coal processing plant and also one of its largest downstream chemical manufacturers and is, therefore, home to large quantities of hazardous materials that are manufactured daily. This means that it is vital that all plant processes are suitably monitored and critical alarm systems are in place, able to alert operators about any abnormal alarm events that occur. In Australia, safety critical systems regulations, such as IEC 61508, usually insist risks are made “as low as reasonably practical”.
For example, alarm annunciators that monitor the plant’s steam turbines or catalytic converters are an essential part of operations and there would be serious consequences in the event of a system failure. In 2023, the Australian alarm installation services market is thought to be worth US $3.6 billion.
“The larger systems are too costly and difficult to re-engineer, so it was vital that all field wiring remained the same on the new system,” said Sakkie Buys, engineer at Sasol Technologies. “Replacements need to comply with the fit, form and function philosophy to optimise savings. Furthermore, documenting and re-engineering plant wiring is an administratively challenging task and hugely expensive in labour hours, so any system replacement would ideally minimise any changes.
“This was a large part of the reason we engaged Omniflex as it could provide modern critical alarm systems to replace the old systems that plug into the existing plant interface using the same panel space. This also meant changes to wiring and contacts were kept to a minimum and there were no unnecessary administrative requirements.”
The systems that Omniflex provided for Sasol comprised products from across its Omni16 series of alarm annunciators, including its Omni16C 16-point alarm annunciator, Omni16R rack-mounted annunciator with card slots for remote logic and OmniX remote LED displays, which provide eight to 124 annunciator windows in a standalone panel-mount package.
“We replaced the existing rack of card mounts and inserted the Omni16R rack into the same space,” said Ian Loudon, international sales and marketing manager at Omniflex. “With 16 inputs per card, compared to the previous system that had two inputs per card, this meant the new system had a much higher I/O density and required less space, as well as being 80% more energy efficient using LED technology.
“Cables, which are approximately 30 m long, connected the alarm racks to OmniX displays that are situated in the control room. A common problem when replacing old annunciator systems is changing the column and row matrix compared to the old system, but the OmniX allows users to define any row by column size, meaning they can match the old systems and maintain operator familiarity. This is particularly important for safety-critical alarms where operator response time is crucial in preventing serious incidents from occurring.”
The systems also provide Sasol with improved sequence-of-events recording capabilities. This is beneficial as rapid fault diagnosis can be made, improving the time for operators to react. Alarm technology continues to evolve, requiring greater access to live and historical data and increased sequence-of-event analysis capabilities in the event of a plant incident. The system dates and time stamps every plant alarm with a better than one millisecond resolution, enabling rapid root cause detection and efficient analysis of plant trips and alarms.
Originally published here.
Phone: 02 8090 2144
IDEC FS1B safety controller
The FS1B safety controller offers flexible preconfigured logic strategies to simplify design and...
Fortress Safety tGard access control with IO-Link Safety
Fortress Safety has announced an upgrade to the connectivity capabilities of its tGard range of...
Allen-Bradley Logix SIS safety system
Logix SIS is a safety instrumented system designed to address the evolving needs of modern...