Top float
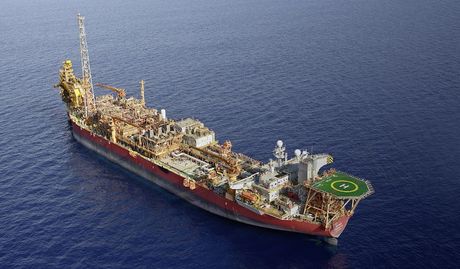
Woodside, Australia’s largest independent oil and gas company, is recognised globally for its world-class capabilities as an explorer, developer, producer and supplier. Its proven track record and distinctive capabilities are underpinned by 60 years of operational experience, characterised by strong safety and environmental performance in remote and challenging locations.
The company operates the Okha floating production, storage and offloading facility (FPSO), which was commissioned in 2011. The facility is located offshore about 135 km north-west of Karatha in Western Australia and stands in 80 m of water. It connects to 10 subsea wells with an estimated production capacity of 60,000 barrels of oil per day and has a storage capacity of 925,000 barrels.
The Okha FPSO has been designed to extract, process, store and offload oil as well as export gas from the Cossack, Wanaea, Lambert and Hermes (CWLH) fields. The topside processing facilities consist of oil, water and gas separation systems, plus gas compression equipment. Oil from the CWLH fields can be produced through the wells via five production manifolds connected to the Okha FPSO. In addition, the facility has one gas-lift integrated manifold, which supports gas export into the North West Shelf Project’s trunk line for onshore processing at the Karratha gas plant.
The Okha FPSO is designed with a closed-loop flare system so that, under normal operating conditions, no continuous flaring occurs. The surplus gas from the production system is redirected to the cargo tanks to provide a 100% hydrocarbon blanket; it is subsequently used as lift or export gas. The facility operates 24 hours a day, 365 days a year, supporting production and maintenance activities. Production involves receiving hydrocarbons from the CWLH fields via subsea infrastructure, followed by onboard processing and storage and, finally, export of oil to tankers and gas to the trunk line. The facility and supporting subsea infrastructure are inspected and maintained regularly to ensure safe and reliable operations, and a turret mooring system that can be disconnected allows it to safely sail away in severe weather, such as cyclones.
The Okha’s integrated control and safety system (ICSS) is based on a Simatic PCS 7 process control system with fault-tolerant controllers and a combination of standard and safety I/O systems used downstream. The OS level comprises three redundant OS servers (topsides and vessel, fire and gas, and package), 11 OS clients, a central archive server, an asset management server and an offshore data provider server. A total of 11 fault-tolerant controllers make up the AS level. Because the package units for the boiler, gas compressor, connect/disconnect system and nitrogen system are automated based on Totally Integrated Automation from Siemens as well, they can be easily integrated into the ICSS.
Woodside also uses Comos Walkinside 3D virtual reality software for work on Okha and other FPSOs. The software allows operators and maintenance personnel to familiarise themselves with the layout of the vessel through a 3D simulation onshore, prior to flying out to the facility. The Comos Walkinside solution can be used for immersive operator training and delivers tools for efficient data exchange with third-party applications, as well as distributed real-time collaboration. As a result, service and maintenance work can be planned, simulated and executed efficiently.
The Siemens experts in Australia have been involved in the Okha project from its early stages and provided a comprehensive training program for Woodside engineering and maintenance personnel. They also supported the project during and after commissioning, as well as during system optimisation and process improvements. Subsequently, Woodside established a maintenance contract with Siemens for the complete ICSS which is reviewed and renewed annually, including on-call support, weekly health checks and services for preventive maintenance. Siemens will also develop and manage a life cycle road map for the facility. The teams are already planning the next steps, such as upgrading the Simatic PCS 7 system to the latest version in order to keep the solution in line with technology evolution and providing Woodside with new features.
Phone: 137 222
Anderson Greenwood Type 84 pressure relief valve
The Anderson Greenwood Type 84 pressure relief valve is designed to protect tanks and vessels...
TESCOM AGI BR Series packaged flushing ring solution
The TESCOM AGI BR Series flushing ring is a packaged solution for flushing and bleeding...
Alfa Laval ThinkTop V55 diaphragm valve control unit
Designed for Alfa Laval diaphragm valves, the slim profile of the ThinkTop V55 is designed to...