Sunrise Dam gold mine implements a dewatering control system
Thursday, 05 April, 2018 | Supplied by: KAPP Engineering
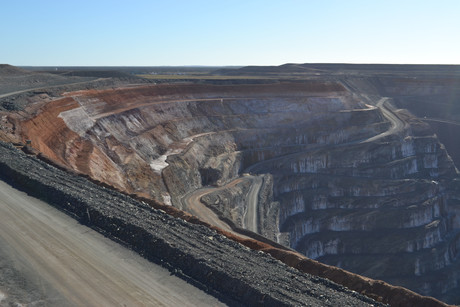
AngloGold Ashanti’s Sunrise Dam gold mine, located 55 km south of Laverton in Western Australia, began operations in 1995, commencing underground gold ore extraction by 2003. As the ore extraction started to go deeper underground, several electrical substation and pump stations were being installed across the mine to perform the hypersaline water-pumping duties from the pit bottom all the way to the surface.
An increasing number of manually operated pump stations — as well as limited data about running hours per drive, equipment faults, pressure readings and volume of water being displaced to the top — led to engineering studies that concluded on the necessity to implement a dewatering process control system (PCS).
KAPP Engineering, as a systems integrator that has an ongoing working relationship with AngloGold to maintain and support the operations for the respective processing plant, was engaged to design and develop the PCS that would ultimately monitor, interconnect and control the dewatering function of the underground operation.
The solution was to integrate nine independent mono pump stations, four diesel pump stations, an intermediate flow monitoring station and two additional subsystems: an underground vent fan and stench gas release system respectively.
PLCs and SCADA servers were implemented in a redundant configuration, with two single-mode optic fibre rings to carry the field I/O data and SCADA data respectively. The rings, forming the backbone of the control architecture, provide self-healing and rapid recovery times in the event of a failure.
Rockwell Automation Allen Bradley 1756-L74 PLCs were selected for controlling the operations of the entire dewatering system, having two EtherNet/IP adapters, which allowed the ability to have two independent networks sharing the same control data. The first Ethernet adapter was assigned the field and I/O data traffic, communicating using EtherNet/IP through an optic fibre ring. The ring itself is composed of 18 Moxa industrial switches with a Turbo Chain redundancy protocol, interconnecting 15 POINT I/O EtherNet/IP adapters with respective I/O cards.
A second Ethernet adapter was assigned for the monitoring of SCADA data traffic using an independent optic fibre ring interconnecting three Moxa switches, two Dell PowerEdge R710 servers running CitectSCADA, and two SCADA clients for the underground infrastructure department and Barminco’s mine operation shift supervisor.
The CitectSCADA servers are set up in a manner that allows automatic detection of a server failure and automatic failover, ensuring that the SCADA system will be available as long as one of the two servers remains operational.
Critical pump stations were allocated with a standalone Allen Bradley L74 PLC and PanelView Plus operator interface panel to give the operators the option of controlling it locally and independently in case of communications failure. This is the case for the level 2225 pump station, which is controlling eight mono pumps and three diesel rental pumps, and similarly for the level 2004 (Hammerhead) pump station controlling two trains of three pumps each.
In normal operation these standalone controllers communicate with the main redundant dewatering controller performing a produce/consume procedure, making the local tags available to be monitored and controlled by the SCADA system up in the surface.
Specific situations require customised implementation, as in the case of the diesel rental pump stations installed during the wet and rainy seasons to support the operation. These pumps are controlled locally by DCU Intelidrive unit with Modbus RTU capabilities and through several protocol conversions, making the data available for the main controller to read data and command the start and stop of the drives. These protocol conversions consisted of a first Modbus RTU (RS-232) to RS-485 to achieve longer transmission distances and then a second RS-485 Modbus RTU to EtherNet/IP.
“Without the ability to see the various pumping stations within the dewatering network underground, it was very difficult to identify any issues with the overall mine water balance and establish if there were any underperforming pumps or pump stations,” said Richard Austin, underground infrastructure superintendent at Sunrise Dam. “Implementing a dewatering process control system gave us the option of controlling and monitoring the pump stations underground and in the pit, while having reporting capabilities on the volume of water being pumped out to the surface. Trend analysis proves to be a very useful tool to manage pumping networks.”
Apart from this main structure, there is a radio communication network, integrated by four Weidmüller 900 MHz Ethernet radios, to integrate two independent pump stations on the pit, which are difficult to reach through an optic fibre or any wired media.
Additionally, third-party vendor packages were integrated into the process control system to facilitate monitoring and control. In the case of the main ventilation drive underground, the operators were given the ability to start and stop the ventilation system from the surface, as well as to adjust speed and other critical parameters. As for the stench gas release system, which is controlled by Miri RTUs, the ability to monitor the status of each one of the release units underground and perform an actual release of the gas was implemented using the required privileges.
Phone: 08 6103 1234
Anderson Greenwood Type 84 pressure relief valve
The Anderson Greenwood Type 84 pressure relief valve is designed to protect tanks and vessels...
TESCOM AGI BR Series packaged flushing ring solution
The TESCOM AGI BR Series flushing ring is a packaged solution for flushing and bleeding...
Alfa Laval ThinkTop V55 diaphragm valve control unit
Designed for Alfa Laval diaphragm valves, the slim profile of the ThinkTop V55 is designed to...