Software-based process orchestration improves visibility at hydrogen facility
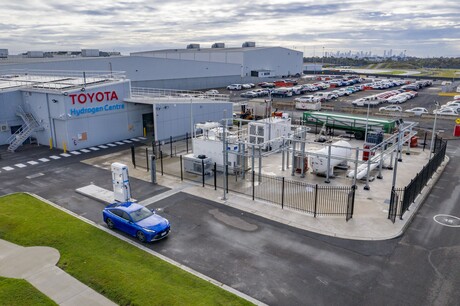
Since the closure of its vehicle manufacturing, Toyota Australia’s Altona Emissions Testing facility in Victoria has been transformed into a demonstration-scale hydrogen production, storage and refuelling plant.
The primary objective of the project was to demonstrate the process of generating, storing and utilising hydrogen gas, including demonstrating the use of a percentage of renewable energy. As part of the project, Toyota Australia engaged with Emerson to supply the control and safety systems.
The Toyota demonstration project shows that a combination of onsite solar PV with battery storage can provide the facility with reliable and continual power supply. The facility is also connected to the grid. The project demonstrates that hydrogen produced onsite can fuel hydrogen-powered vehicles and supply electricity to the Altona site through the use of a fuel cell. The project also involved the building of a Hydrogen Education Centre to promote hydrogen innovation and awareness.
The challenge for the Emerson project team was to connect a wide array of OEM systems, all using a variety of communications protocols. Engineering connections between the systems ran the risk of building a complex, cumbersome infrastructure that increased costs, while potentially delaying the project and impeding efficient maintenance across the lifecycle of the plant.
The Toyota project team collaborated with Emerson to create a process orchestration layer connecting a system consisting of power meters, an electrolyser, a fuel cell, a hydrogen refueller, a solar and battery inverter system and instrumentation to collect data for system monitoring and reporting. Much of the data collected will be shared with the Australian Renewable Energy Agency (ARENA) to contribute to a nationwide pool of information from ARENA projects. ARENA provided approximately 40% of the Toyota project’s funding.
Toyota used Emerson’s DeltaV Automation Platform to integrate the various OEM systems needed to run the hydrogen system effectively and efficiently. The project team selected the DeltaV Distributed Control System (DCS) and Safety Instrumented System (SIS) to manage operations such as differentiating between deep and normal cycle drawdown of the hydrogen storage vessel.
The DCS and SIS are natively integrated with Emerson’s DeltaV PK controller to eliminate complex configuration between the automation equipment, managing orchestration for the many skids and systems running across the plant. The Toyota team converted a wide variety of communication protocols from the many OEM systems to a common protocol — EtherNet/IP — and directly terminated them on the DeltaV PK controller to reduce communication complexity, lowering project costs and shortening the project schedule.
The Emerson team also saved significant time and effort in integration by deploying the DeltaV DCS and SIS with Emerson’s PACSystems RX3i CPL410 Edge Controller to gather data from the solar PV and battery system via a web-based API. WebAPI connections provide access to renewable energy data, system energy efficiency calculations and data from the site’s existing 500 kW solar array. Rosemount infrared flame detectors also help keep personnel and operations safe.
Toyota’s highly connected architecture readies the plant for future expansion, enabling the organisation to add future requirements such as remote operations and data analytics more easily, without the need for complex engineering.
Phone: 03 9721 0200
Anderson Greenwood Type 84 pressure relief valve
The Anderson Greenwood Type 84 pressure relief valve is designed to protect tanks and vessels...
TESCOM AGI BR Series packaged flushing ring solution
The TESCOM AGI BR Series flushing ring is a packaged solution for flushing and bleeding...
Alfa Laval ThinkTop V55 diaphragm valve control unit
Designed for Alfa Laval diaphragm valves, the slim profile of the ThinkTop V55 is designed to...