Pinnacle Midstream futureproofs Texas oil and gas operations
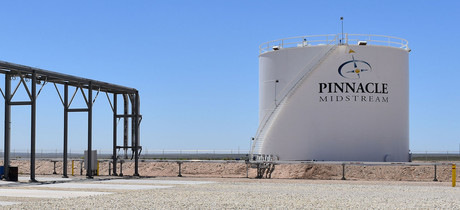
Pinnacle Midstream was formed by a group of seasoned oil and gas executives who have a vision for changing the profitability dynamics of the midstream oil and gas market and believe technology will play a significant role. Pinnacle focuses on installing and operating value-added solutions that free midstream production facilities to focus on continued development of field oil and gas assets while benefiting from the economies gained by extending oil and gas gathering systems to neighbouring producers. Pinnacle tailors each customer solution for compression, treatment, processing or dehydration of a producer’s oil and gas to derive the highest market value.
When Pinnacle set out to add new delivery points in West Texas, the company turned to Meers Engineering, a Texas-based systems integration firm that was already implementing Inductive Automation’s Ignition SCADA interface and management software for it. Together, Pinnacle and Meers concluded that a long-term strategic plan for control automation — one based on the most modern industry standards and protocols — would establish the foundation they needed to accommodate anticipated growth. Pinnacle’s philosophy of leveraging cutting-edge technology led Meers to conclude that the Bedrock system was the right answer for its automation controls. Bedrock’s open, secure automation platform not only offered the best combination of efficiency, flexibility and reliability for Pinnacle’s current pipeline control and safety needs, it could easily scale to meet future needs, including a potential future transition to a DCS application.
Meers also felt that Bedrock’s list of advanced features would help Pinnacle futureproof its approach from the beginning. Key attributes such as intrinsic cybersecurity, environmental hardening and large-scale processor data logging were just some of the platform capabilities that convinced Pinnacle that the Bedrock platform was aligned with the company’s technology philosophy. There was also a need to overcome the challenges posed by remote and rugged locations, as well as the demand for high performance and secure reliability.
“Bedrock’s construction makes it ideal for very, very rugged conditions,” said David Ibach, a Meers Automation principal. “The completely enclosed metal cases provide critical protection in these very sandy, dusty areas. Then there are the extreme temperatures — which can really pose a problem with control systems. Lightning is a real problem out here as well, so Bedrock’s EMP resistance is a big deal. Pinnacle actually had some equipment go out due to lightning in the past, which poses a significant safety concern.”
Bedrock’s ability to lock down system cyber-vulnerability — given that concerns around potential attacks on critical infrastructure assets continue to escalate — was also a welcome aspect of Bedrock’s value proposition, according to Ibach.
The platform’s overall efficiency helped complete the picture for Pinnacle. Bedrock’s non-obsolescence guarantee was a big value-add, according to Ibach. “That’s huge for them,” he said. “They want equipment that’s going to last a long time, and that’s going to keep a lid on total cost of ownership. Features like the universal, software-configurable I/O represent big savings because Pinnacle will need to buy fewer I/O modules for the same applications. Being able to put any I/O point anywhere is really nice — and enabling them to do that on the fly with software changes the game entirely.
“As their integrator, we were also impressed with the capabilities designed into the Bedrock controllers. You can tailor any solution very elegantly and the object-oriented programming allows us to easily customise and troubleshoot applications right in the controller itself.”
The solution manages midstream crude that’s being held in storage tanks and subsequently transferred into trucks and pipelines. That means controlling the flow of the oil into the tank, out from the tank and into trucks and pipes as well. The only thing the Bedrock system doesn’t currently control is the actual volume metering, because validated audit trail was already provided by pre-validated metering devices.
Pinnacle and Meers both felt Bedrock offered superior flexibility compared to other potential solutions. “We are able to store data in the processor,” Ibach added. “That allows us to log data, events and sequence of events right in the controller. The speed and simplicity of getting accurate data, in real time, into the controllers is impressive. It also minimises bandwidth requirements that would otherwise be needed to push that data to other applications.”
The system incorporates numerous digital and analog I/Os, communicating with multiple devices via Ethernet, all of which are tied into and secured by the Bedrock system. Another aspect of flexibility was Bedrock’s Integrated Development Environment (IDE) and its programming capabilities that allowed Meers to pass substantial engineering savings on to the customer.
Pinnacle’s implementation in its current configuration populates the Bedrock pinless backplane with 10 I/O modules, including 10-channel universal I/O modules and a 5-channel Ethernet module. The universal I/O modules connect to the field computers, which control flow at each storage tank. The Ethernet I/O connects with IIoT edge devices and applications to mine data for subsequent planning and operational improvement. The Ethernet modules also poll radios on wireless sensors simultaneously and support Power over Ethernet (PoE), which simplifies installation further by eliminating the need to run additional wiring to some of the devices. Bedrock control modules integrate switching and other functionality usually relegated to external devices, reducing wiring and installation costs. This also makes it very easy to scale up in five, 10 and 20 backplane unit increments.
The solution was commissioned in January 2017 and is fully operational. Ibach feels it was very easy to implement with a short learning curve, which from a start-up perspective is a huge time saver. He cites ease of use, the IDE’s intuitive interface and power, and the ability to software configure the system as competitive differentiators.
“The Bedrock system is very start-up friendly, and it can scale easily as the user’s business grows. It uses state-of-the-art electronics and is designed to work for decades. Its free IEC 61131-3 compliant engineering tools also saved a great deal of coding time during the installation and will continue to reduce maintenance costs for many years to come,” said Ibach.
“We are expanding to the meet the growing need for midstream services and need a secure way to centralise flow control amongst our facilities, said Mike Hillerman, VP of Engineering and Operations for Pinnacle “The Bedrock system provides an economical solution in a small, easy-to-implement system that can coordinate edge control today, while also scaling easily and economically to the full DCS functionality we expect to need in the future.”
Based on the system’s performance to date and its inherent scalability, Ibach believes Bedrock will play a key role in this facility’s expansion as well as other Pinnacle facilities, including global locations.
Phone: 1300 376 288
TESCOM AGI BR Series packaged flushing ring solution
The TESCOM AGI BR Series flushing ring is a packaged solution for flushing and bleeding...
Alfa Laval ThinkTop V55 diaphragm valve control unit
Designed for Alfa Laval diaphragm valves, the slim profile of the ThinkTop V55 is designed to...
Siemens SIMOCODE M-CP motor management system
Siemens has launched SIMOCODE M-CP motor management system designed for motor control centres.