Next-gen tech supports mining productivity and innovation
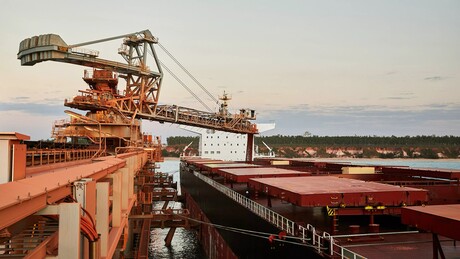
Australia is the world’s largest producer of bauxite, the primary component of aluminium. Aluminium is a key part of our everyday life and helps us travel far and wide. It is used in bikes, cars, trains and planes because it’s strong, lightweight and corrosion resistant. These properties also make aluminium the perfect solution for countless food and beverage applications — from drink cans to aluminium foil — and most importantly, it can be recycled over and over.
Rio Tinto is a global leader in aluminium, and located in Far North Queensland on Cape York in Australia is their Amrun mine. The Amrun mine is the third continuous mining operation alongside East Weipa and Andoom in the Rio Tinto Weipa Operations portfolio, which has been producing bauxite since 1963, and exports more than 30 million tonnes of bauxite annually.
Constructing Amrun took three years, with automation and control requirements needing to be carefully considered with the mine being in such a remote and isolated location. The project went to market for a main automation contractor (MAC) to provide engineering design services, equipment supply, implementation services, site services through offsite switch room testing, pre-commissioning and commissioning support, as well as training services. A key aspect of selecting the MAC was partnering with an organisation that could demonstrate capability in delivering an end-to-end automation solution for a major capital project. Of importance was the project delivery personnel who would see the project through from design office, Factory Acceptance Testing (FAT), pre-commissioning and commissioning.
The Rockwell Automation suite of products was chosen to provide a complete solution from the ground up — from its communications stack through security, product integration, diagnostics and engineering tools — as a complete solution.
The processing plant, materials handling systems, water and tailings, mine infrastructure, wharf and rail-mounted machines are all controlled by Allen‑Bradley ControlLogix controllers, together with Allen‑Bradley CompactLogix controllers for smaller outdoor MCCs and package controllers. Given the scale of the Amrun site, there are approximately 50 PLC controllers in operation across the site.
With a large, distributed architecture, Amrun needed a modern process control system that could provide seamless integration between critical mine processes.
After looking at various technologies, a Rockwell Automation PlantPAx solution was implemented, delivering cost savings and schedule benefits. Using a predefined and standardised library ensured rich functionality and robust performance. The usability of the PlantPAx toolset allows for quick modify configuration and its ability to be easily integrated across multiple systems has simplified control system troubleshooting.
By using a common automation platform, the PlantPAx system provided seamless integration between critical process areas of the processing plant. Amrun’s control and automation system uses plant-wide Ethernet communications with the complete FactoryTalk suite of products. The entire suite of application servers is virtualised on high-availability data centres.
While Amrun is located in an isolated site approximately 800 km from Cairns, the data centre is integrated into Rio Tinto’s IT infrastructure, enabling centralised management and remote access. A set of portable mobility tablets was implemented so operators could access data from the plant. These devices were enabled by Rockwell’s ThinManager, providing users access to real-time information.
“With integrated software that can collect and manage the information from various sensors, devices and systems from across the site, operators can now collect, coordinate and share data internally,” said Bernard Ooi, Project Manager, Rockwell Automation. “This helps to ensure better data-driven decision-making and greater consistency in results.”
Safety was a key priority for the mine and processing plant, and as such, Amrun uses the latest technology to run operations safely and efficiently. Functional safety was implemented in GuardLogix controllers and integrated with the PLCs to provide seamless visibility of safety and control.
With such a large-scale project, it was important that commissioning was a smooth process. To help achieve this, the FAT was undertaken at the Rockwell Automation facility in Melbourne. The majority of the plant was staged and tested in a complete integration test to simulate the control of the plant from the dump truck through to the ship loader. The full integration test was conducted with the required controllers and application servers hosted on the VMWare-enabled data centres.
The Amrun project was delivered under budget and ahead of schedule as a result of an integrated approach to design, construction and commissioning.
“Amrun is a great example of innovation through collaboration, which is vital for advancing the future of mining,” said Glenn Otway, Manager, Power and Automation, Rio Tinto.
Phone: 03 9757 1111
Alfa Laval ThinkTop V55 diaphragm valve control unit
Designed for Alfa Laval diaphragm valves, the slim profile of the ThinkTop V55 is designed to...
Siemens SIMOCODE M-CP motor management system
Siemens has launched SIMOCODE M-CP motor management system designed for motor control centres.
Rotork IQ3 Pro valve actuator with Ethernet
Rotork has introduced a fully integrated Ethernet actuator compatible with EtherNet/IP, Modbus...