IIoT solution enables water company to leverage data insights
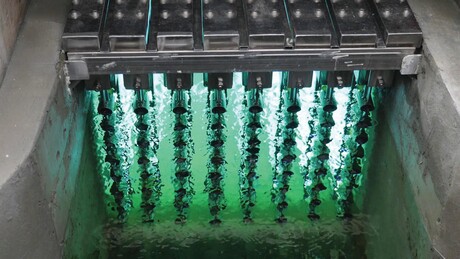
Founded in 2016 in Chengdu, China, Chengdu Xihui Water Environmental Co., Ltd. (Chengdu Xihui) operates wastewater treatment plants and supply networks. The company manages seven plants, including a wastewater treatment plant that has a daily treatment capacity of up to 190,000 tons.
In 2019, Chengdu Xihui recognised the need for a digital transformation and sought an industrial Internet of Things (IIoT) solution. They chose Insights Hub, an IIoT solution from Siemens, to improve operational decision-making.
There were three major challenges that Chengdu Xihui addressed with the implementation of Insights Hub. First was water quality, which is Chengdu Xihui’s top priority. In the past, the company used a manual process to address water quality issues, such as the concentration of dissolved oxygen (DO), quantity of water intake, quantity of aeration, dosage of chemicals and the reflux ratio. The DO and oxidation reduction potential (ORP) sensors were used to measure the concentration of dissolved oxygen and then the data was uploaded to a SCADA system via a PLC. Only then were adjustments made. Due to these lengthy manual processes, it was very difficult to keep water quality at a stable level.
Another challenge for Chengdu Xihui was operating costs. The top three operating costs are machine and parts maintenance, energy consumption and chemicals. Without measurement and process transparency, plants are forced to overuse chemicals and excessive treatment to ensure output water conforms to regulations. The overuse of chemicals, in turn, increases machine usage, machine maintenance and energy consumption.
Unplanned plant downtime was the third challenge. When running eight wastewater treatment plants simultaneously, the failure of one will not only affect the quality of water output, but also greatly impact operational costs.
Upon deploying Insights Hub, Chengdu Xihui started to connect isolated critical assets and processes to break down barriers. The company used MindConnect 2040, a plug-and-play connectivity solution, to connect assets and processes. Chengdu Xihui now uses the MindConnect 2040 to connect PLCs to critical equipment and processes and acquire real-time IoT data insights.
Chengdu Xihui also leveraged many of the Insights Hub applications and solutions from the Siemens Xcelerator business platform to further propel its IoT implementation.
For example, with Industrial IoT Asset Manager, Chengdu Xihui established IoT data models so it could define IoT data collection points and manage equipment assets. It now uses Insights Hub Monitor to view all plant, production lines and equipment in the cloud, and to realise remote monitoring by self-defining alarm rules and response events. Insights Hub Monitor also allows Chengdu Xihui to check the operational data of any asset and send the data to the equipment provider in real time through KPI alerts, requesting the equipment provider to conduct equipment troubleshooting remotely.
“Siemens understands the wastewater industry and our challenges,” said Zhang Chenghui, General Manager, Chengdu Xihui. “Insights Hub provides us with the required transparency and data-driven insights needed to make the right decisions and strengthen our digitalisation strategy.”
The energy consumption of critical assets, like a blower, in a wastewater treatment plant needs to be consistently monitored and evaluated. A blower’s energy consumption typically accounts for 50% of total operating costs. Based on a comprehensive analysis of IoT data done with Insights Hub, Chengdu Xihui can now associate the blast capacity of the blower with current electricity prices, take advantage of off-peak electricity prices and, as a result, control a blower’s output power while ensuring the quality of the water output. Doing this keeps the blast capacity at a lower level to minimise energy costs.
“Thanks to Insights Hub, critical assets are well managed now,” said Li Junwen, Maintenance Manager. “We can schedule maintenance ahead of time and also work closely and efficiently with the equipment provider and service provider.”
As a result, Chengdu Xihui has successfully reduced its monthly electricity costs by 10% and realised a further 10% cost savings by refining and digitalising the extensive chemical administration model.
Maintenance is now also smarter. Based on real-time and historical data collected from the blowers, machine learning (ML) and advanced analytics can provide earlier warnings to maintenance personnel before the failure of a blower. Alerts can be escalated to the equipment provider for remote diagnostics or to reset the machine.
With advanced analytics and ML, the company’s plant maintenance shifted from a reactive or scheduled approach to a proactive approach. Now assets can be serviced based on operating data and actual health instead of prescheduled unnecessary maintenance or when an asset is already failing.
Through the company-wide deployment of Insights Hub, Chengdu Xihui has not only achieved digitalised monitoring and management of the whole wastewater treatment process, but found the most scientific, accurate equilibrium point between product quality and cost by diving deep into IoT data analysis, leading to significant cost savings.
Phone: 137 222
Anderson Greenwood Type 84 pressure relief valve
The Anderson Greenwood Type 84 pressure relief valve is designed to protect tanks and vessels...
TESCOM AGI BR Series packaged flushing ring solution
The TESCOM AGI BR Series flushing ring is a packaged solution for flushing and bleeding...
Alfa Laval ThinkTop V55 diaphragm valve control unit
Designed for Alfa Laval diaphragm valves, the slim profile of the ThinkTop V55 is designed to...