Tracking software for pallets, containers and more
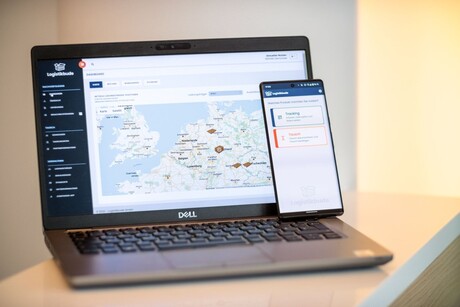
Pallets, crates, containers, racks and tanks play a vital role in transporting goods. According to data from the Federal Statistical Office of Germany, approximately 101 million flat pallets — also known as Euro-pallets — were produced in Germany in 2020. But while the whereabouts of the goods are precisely recorded and tracked, to date, the load carriers themselves have received far less attention. They often remain unattended in warehouses for days, reducing efficiency.
At the Fraunhofer Institute for Material Flow and Logistics IML in Dortmund, researcher and logistics expert Dr Philipp Wrycza, together with his co-founders Patrik Elfert, Jan Möller and Michael Koscharnyj, have developed a suitable software solution and recently founded their own spin-off with the appropriate name ‘Logistikbude’, meaning “logistics convenience store”.
The web-based software first generates a label for each load carrier and creates a digital file. At the same time, returnable load carriers — pallets, tanks, racks, containers, crates — are equipped with barcodes or active sensors. A smartphone app available for Android or iOS records each load carrier via its label both before transport and when the goods arrive at their destination. It also allows further entries about their status to be made. This data is then immediately synced to the web-based software platform. In addition to tracking the load carriers by scanning them, there is also the option to record quantities.
The customer or recipient of the goods can also access the account and record, for example, when the goods have been unloaded and the pallets are ready to be returned or to transport other goods. In this way, a joint exchange account is created in which the business partners keep each other informed about the current status of the load carriers. If load carriers that have already been emptied have not been returned promptly, a reminder email is sent automatically.
“Until now, many companies have often not even known where their own load carriers are at a given moment, for example,” Wrycza said. “Now they can see where they are at any time and when they will get them back. It makes planning easier, and the accelerated circulation ultimately ensures that fewer load carriers have to be purchased overall, contributing to increasing sustainability in the sector.”
The software also helps avoid problems that regularly occur between business partners. For example, if a glass manufacturer loads their transport racks with windows and has them picked up by the carrier, they either receive the empty racks back straight away, or the haulage firm delivers the goods to the recipient and then returns the racks. However, misunderstandings and conflicts arise time and again; for example, if a rack is missing or if the recipient believes it is damaged.
The joint management of the load carriers helps to avoid errors and surprises from the outset. This is because the status and position of each individual load carrier can be viewed transparently. For example, the recipient can now record on the smartphone app if a rack arrives damaged. Companies that already have their own load carrier management also benefit from this solution. Previously, it has not been possible, or only possible at great expense, to dynamically track all these packaging materials during transit and seamlessly exchange data with business partners.
It is also possible to equip the load carriers with sensors. These can record values such as location, temperature or humidity and record them in the digital load carrier file. This would also allow them to provide information about the condition of food, for example.
The Fraunhofer researchers have made the software highly user-friendly. There is no need to customise the system. “We’ve allocated one day of training, and then the customer can get started right away,” Wrycza said.
Dr Volker Lange, head of Packaging and Retail Logistics at Fraunhofer IML, has supported the team’s work from the very beginning: “Our researchers have come a long way from the initial good idea to having a market-ready and cleanly functioning solution,” he said. “The spin-off now has the best prerequisites to successfully establish the solution on the market.”
Leuze DCR 1048i OCV image sensor
The DCR 1048i OCV from Leuze can read 1D or 2D codes within one application and also check...
Flexicon mobile flexible screw conveyor system
Flexicon's latest mobile tilt-down flexible screw conveyor system is designed for manual...
Cognex DataMan 380 image-based barcode reader
The DataMan 380 barcode reader uses AI and wide-area scanning to speed up production lines.