RFID technology ensures accurate paper production
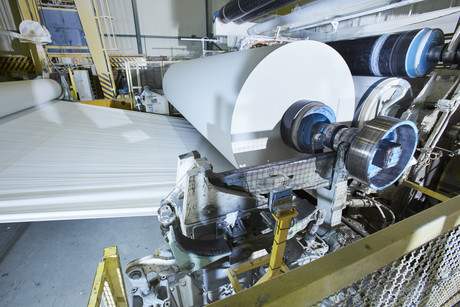
It is clearly evident that digitalisation has left its mark on the paper industry. Does print media face an uncertain future or will haptic page turning hold its own? Both theories have their proponents, but German company Kabel Premium Pulp & Paper (Kabel) and its paper mill are showing no sign of dark clouds on the print horizon, with the company manufacturing high-quality paper around the clock.
Since 1896, Kabel has been manufacturing for the biggest printing houses in Europe. The Hagen-based company in Germany’s Westphalia region initially manufactured newspaper; now it specialises in coated paper for high-quality catalogues and magazines, handling a total capacity of around 485,000 tons per year.
To maintain a strong overview of the multistep production process, Kabel utilises an RFID-based identification solution, with an integrated high-performance, wireless transmission system. This enables workers at Kabel to constantly track and determine in any given paper batch which production step is currently being processed.
Kabel produces each roll of paper — known as a ‘tambour’ — in line with client specifications, and overhead cranes transport them from one processing step to the next. Depending on the particular paper thickness, the rolls, measuring 7.20 m wide, carry around 50,000–60,000 m of product and weigh up to 20 tons.
Production faults in Hagen can mean tens of thousands of metres of paper wasted. Therefore, to keep a close eye on the production of each individual roll, Kabel uses a custom-made RFID solution from system integrator Intelligent Data Service (IDS) with 26 RFID reading devices provided by SICK.
“We required a solution to ensure the automatic detection of tambour cores in the production flow,” explained Johannes Broer, who is responsible for IT at Kabel. “Our requirements included, among other things, reliable system components and wireless data transmission to our IT system. The components used are exposed to process-related contamination, dust and heat. They must be able to withstand contact with chemicals or machine oil.
“We therefore had to rule out optical detection-based solutions due to the risk of contamination.”
Additionally, a solution with very short read times was required since the tambours are constantly in motion. “Apart from the fact that the reading stations can be hard for our workers to reach, the long identification numbers can also result in manual input errors,” he continued. “Automated detection allows us to ensure accurate tracking and relieve some of the burden on our workers.”
The tambour cores are marked with passive RFID tags, which are read at individual stations. When the tambour is rolled out for the first time, the system records which tambour core the batch is assigned to, and from this point on, each station will accurately read out via RFID which tambour core the paper is being wound into and from.
A total of 26 UHF RFID reading devices from SICK are being used at the factory in Hagen to decipher the passive tags on the cores. Depending on the reading distance, an RFU620 is used for a scanning range of up to 1 m and RFU630 for larger scanning ranges. Passive RFID tags have no energy source of their own that would require regular inspection and are more reliable than active tags when it comes to processing. They are the ideal option for objects that come under heavy mechanical strain such as tambour cores.
At Hagen there were a number of factors that had to be taken into consideration, including metal reflecting radio waves, which can result in system faults. It is for this reason that the RFID tags on the metal cores had to be chosen so that close proximity to metal wouldn’t pose a risk of failure.
IDS integrated the SICK reading devices into its roll online tracking system, known as ‘Rolf’, which IDS developed itself. The system collects all results directly from the RFID reading devices, visualises them and makes the data available for further processing. This means that all process data can easily be viewed in the production database at Kabel and each tambour is directly assigned.
“It was a tall order and we are happy to have found the right partner in SICK,” explained Rainer Marchewka, Managing Director of IDS. “We have been working with SICK for 15 years. We know that we can rely on them and also that long-term system support is guaranteed.”
RFID-based roll tracking has now been in operation for over a year. “We are happy that we opted for this solution,” said Broar. “In truth, we have worked with RFID-based identification solutions previously, albeit with active tags. These are indeed advantageous when it comes to reading range, but the battery runtimes were too short and also the tags were too susceptible in this environment. We are very pleased with this solution and the collaboration with IDS and SICK.”
Phone: 1800 334 802
Leuze DCR 1048i OCV image sensor
The DCR 1048i OCV from Leuze can read 1D or 2D codes within one application and also check...
Flexicon mobile flexible screw conveyor system
Flexicon's latest mobile tilt-down flexible screw conveyor system is designed for manual...
Cognex DataMan 380 image-based barcode reader
The DataMan 380 barcode reader uses AI and wide-area scanning to speed up production lines.