New robotic palletising solution for VIP Packaging
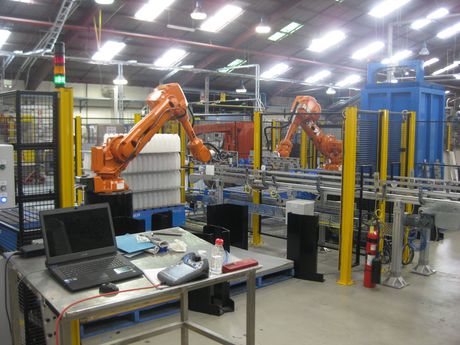
Palletising in any manufacturing plant presents many operational challenges: from production efficiencies to safety considerations. This is particularly applicable to a company like VIP Packaging, a leading plastic and steel packaging company in Australia and New Zealand, which manufactures packaging solutions for the food and beverage, personal care, household consumer and industrial chemical industries.
Among its products, VIP Packaging manufactures extrusion blow-moulded and injection stretch blow-moulded high-density polyethylene (HDPE), polyethylene terephthalate (PET) and low-density polyethylene (LDPE) bottles.
With clients that include many of the most well-known household names in Australia and New Zealand, VIP Packaging is committed to innovation, quality and sustainability.
The production line at the plant predominantly palletises bottles used for shampoos and laundry detergents. To minimise manual handling and gain production efficiencies, VIP Packaging called on Machinery Automation & Robotics (MAR) to deliver a solution to automate its palletising production line.
Hands-free palletising
The VIP Packaging plant transfers packaging bottles that are arranged in pallets in a predesigned format that is suitable for transport directly to clients. These bottles can range in size from 500 mL to 2 L and are delivered wrapped with clear plastic stretch wrap to ensure the bottles stay in position when transported.
Adhering to occupational health and safety standards, improving productivity and generating labour cost savings were all important priorities for VIP Packaging. According to Geoff Biscaya, rigid containers general manager at VIP Packaging, “To remain competitive it was clear we needed to reduce labour costs by automating our downstream inspection, packing and palletising of our high-volume blow moulding machines.”
Throughout this process there were three main palletising lines that would benefit from automation. These include the packaging handling, the pallet handling and the stretch wrapping. The challenge ahead was to design a system that could automate the entire palletising line and deliver not only the cost savings, but also improve quality control and safety.
After studying the operation of the VIP system, MAR presented a fully automated system - including three robots, a pallet dispenser, a twin shuttle, a three-vision system, a fully automated HMI, an automated pallet strapping system and a pallet stretching machine - which were all controlled by one central motor control centre from Rockwell Automation.
In the VIP Packaging plant, plastic bottles are continuously transported on the conveyor to the palletising line, where they are picked up by the robot and stacked in the pallet. Sensors are used to count the required quantity of bottles for each layer of packaging. Once a layer is complete, the robot picks up a plastic slip sheet and places it on top of the layer of bottles. This process is repeated until the pallet is full; the robot then places a timber sheet on top of the pallet to keep the bottles in place.
According to Merv Shirazi, project manager at Machinery Automation and Robotics, “The design of the grippers or claws on the robot arm was critical to the efficiency of the palletising process.
“When the plastic bottles stand up, we needed to make sure that they were in correct position; because if one bottle slipped or fell out of place, a domino effect could occur and hundreds of bottles could then fall, which would not only create a safety hazard that would need attention, but it would also mean that the whole pallet would have to be rejected,” he explained.
To stop the bottles that are packed in the pallet from breaking or slipping, the pallet is automatically wrapped in clear plastic. Each pallet is then transported by shuttle to the loading dock and the empty pallet is returned.
It’s all under control
In any automated system, integration between the control and safety system is important - but in a palletising line that is controlled by a single operator, complete integration is essential. PowerFlex 4M drives, used to provide effective motor control for the conveyors and the entire robotic palletising system, were controlled by CompactLogix.
According to Harish Ahuja, OEM account manager at Rockwell Automation, “The Rockwell Automation compact machine control platform provides cost-effective integration of a machine or safety application into a plant-wide control system because it integrates safety, motion, discrete and drive capabilities in a single controller, making it the most appropriate choice for this application.”
The operator workstation features a PanelView Plus 1000 touch screen that, in addition to the primary control for the system start and stop function, also includes programming for the manual control of conveyors, manual control of the robot gripper, shift production data, error reporting, robot control and access control for maintenance and cleaning.
“The programming of the system is simple and straightforward and it caters for a wide range of bottle-design shapes and sizes. The control platform also includes integrated safety systems which deliver improved operator safety,” said Biscaya.
When moving to an automated system, operator safety was a key priority. With this in mind, the system was designed with six separate safety zones that require no supervision. Parts of the plant were required to operate 24 hours a day, seven days a week, which is why reliability and minimising downtime was very important to VIP Packaging. This was addressed by designing and building the line to allow access to specific components that wear over time in a particular machine, without having to shut down the whole plant during routine maintenance.
Installing a new solution generally requires a period of shutdown of the existing system while the new one is installed, so the goal with this project was to keep this to a minimum and also to reduce the risk of any teething problems with the new solution. To achieve this, the new system was thoroughly tested off-site prior to installation.
“The complete system, including cycle times and other parameters, were factory tested off-site prior to installation so we could minimise the risk of downtime. This ensured that the installation progressed smoothly, which was very important to our business,” said Biscaya.
Consistent quality control
Maintaining superior quality control is essential to VIP Packaging, which is known for packaging solutions that not only offer outstanding performance but also differentiate and enhance customers’ brands. Biscaya knew that automating the company’s quality control systems would help it to maintain its reputation for superior quality packaging solutions and also introduce labour cost savings.
“With the help of MAR, we were able to integrate vision systems that could identify a number of bottle faults and reject those bottles. This automated quality control system was more consistent than the human element, which allowed us to lower the cost of each pallet through the associated labour savings and reduced packaging waste,” he said.
To confirm that the automated system was working effectively, the HMI system was programmed to monitor and sound an alarm to alert the operator if too many bottles were rejected consecutively.
Counting the savings
“We are continuing to realise the many benefits that the new automated system is providing. It has met all of our key requirements by allowing us to reduce labour costs, while also improving quality control and safety. In addition, the solution has established a low base cost to run the plant over time, which helps to improve our productivity and competitiveness,” said Biscaya.
The automation of the palletising line has resulted in significant labour savings, quality control and reduced running costs. The return on investment is approximately two years, which will allow VIP Packaging to reap the rewards from the solution for many years to come.
Phone: 03 9757 1111
Leuze DCR 1048i OCV image sensor
The DCR 1048i OCV from Leuze can read 1D or 2D codes within one application and also check...
Flexicon mobile flexible screw conveyor system
Flexicon's latest mobile tilt-down flexible screw conveyor system is designed for manual...
Cognex DataMan 380 image-based barcode reader
The DataMan 380 barcode reader uses AI and wide-area scanning to speed up production lines.