Wireless steam trap monitoring improves productivity
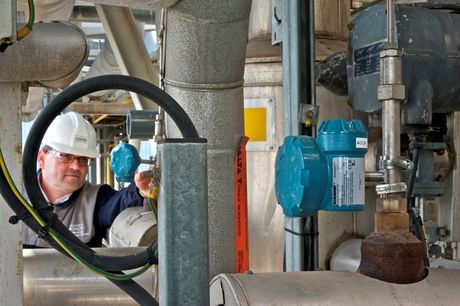
A major food manufacturer in the United States drives innovation in all areas of its business while maintaining the highest quality in its products, services and relationships. For the food product’s plant in the south-east, innovation extends to process instrumentation and control.
“We are always looking to improve energy use,” said the project engineer who provides project and maintenance services in the utility area of this plant. “This is a large plant with multiple product lines which are run as individual business units from a cost perspective. We want to know the energy use for each business unit over time and compare them. In that way, we can make continuous improvements to the areas that need it the most.”
Steam traps were identified as one culprit of energy loss. When a steam trap fails open, steam is not completely consumed and is blown directly into the condensate return system, where it may be lost to the atmosphere in an ‘open system’. It can also raise the pressure in the condensate system, inhibiting the discharge of other traps and causing system-wide inefficiencies. If it fails closed, the system will flood, causing a loss of heat transfer and subsequent loss of production. Steam trap failures also increase the potential for water hammer, which may lead to equipment damage and downtime.
In an effort to prevent steam trap failures, a preventative maintenance (PM) schedule was developed. With close to 100 traps in the plant, PM could only be performed once per year. It takes the maintenance crew at least one hour per unit to check the steam traps, when done properly, so maintenance labour on the traps was 100 hours annually.
“When I heard about the acoustic transmitter from Emerson, I wanted to try it out,” the customer said. “We were looking for automatic, online monitoring of steam trap performance and real-time alerts to minimise preventative maintenance requirements and minimise energy losses. This new transmitter from Emerson seemed like a good fit and we were glad to test it.”
A self-organising, wireless network with wireless 3051S DP flowmeters had already been installed to monitor compressed airflow to the various business units in the plant, to understand the electrical energy use. Adding the non-intrusive wireless acoustic measurement device was easy and saved a significant amount of money in installation cost. “Wireless greatly reduces installation cost,” said the customer, “and we use those savings to purchase more instrumentation to extend utility monitoring in our plant.”
For steam trap monitoring, nine 708 Rosemount Wireless Acoustic Transmitters (with integrated sensors that mount externally) were installed on steam lines throughout the plant and integrated into the existing Smart Wireless Gateway, which communicates to a plant host. The steam traps range from thermostatic (TT) and float and thermostatic (FT) to simple bucket traps. The customer found that the acoustic transmitters work equally well on all of them. One application is even a steam-driven pump, where the acoustics of the pump are being monitored to give an early indication of problems. The network was easy to expand and the new transmitters also strengthened the mesh network. Even though there is a large amount of concrete between the transmitters and the gateway, and high EMF, the wireless communications are strong and reliable.
The 708 transmitter, with a combination of temperature measurement and acoustic ‘listening’, gives high visibility into steam trap states.
“Manual monitoring of temperature did not give us enough information to conclusively target a steam trap for replacement when we saw water hammering,” the project engineer continued. “But when we installed the wireless acoustic transmitter, we could tell immediately which steam trap was stuck.” It was quickly fixed, and a trend of the new trap showed normal acoustics and temperature.
Now the plant has real-time alerts for each of the nine steam traps with wireless acoustic transmitters. Some are in washdown areas and one is in a high-humidity environment. All are communicating reliably. Because of the design of the device, the customer can ‘set and forget’ each of the acoustic transmitters and eliminate manual PM activities.
“We found 22% of our traps needed to be replaced during our last PM check. By installing wireless acoustic transmitters, the plant will prevent steam loss with early detection of steam trap failure. Not only will this minimise energy loss, but it will free up maintenance to focus their time and attention on things that need to be fixed, to further improve our productivity,” concluded the customer.
Phone: 03 9721 0200
ABB ProcessMaster FEW630 electromagnetic flowmeters
The ProcessMaster FEW630 is an easy-to-use electromagnetic flowmeter for municipal and industrial...
Krohne OPTIWAVE 1520 and 1540 radar level transmitters
Krohne has released the OPTIWAVE 1520 and OPTIWAVE 1540 2-wire 80 GHz radar level transmitters...
Optris Xi 1M spot-finder infrared camera
The Xi 1M from Optris has a resolution of 396 x 300 pixels and is housed in a compact, robust...