IO-Link retrofit delivers rapid ROI
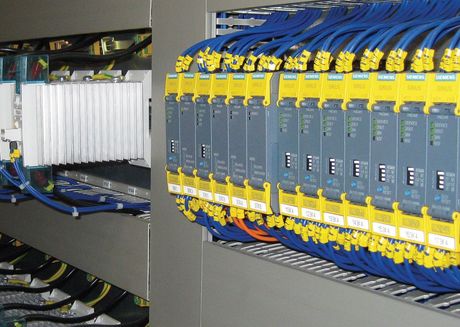
In today’s tight economy, manufacturers are seeking every possible edge to cut expenses and enhance performance. Schwartz GmbH, a German manufacturer of industrial heat treatment equipment, used IO-Link-enabled switching devices from Siemens to upgrade three furnaces it was building for a European customer, resulting in a significant increase in the equipment’s functionality and uptime without cost increase.
Schwartz has been making heat treatment equipment for almost three decades. The company produces furnaces with multiple chambers, each of which is divided into several zones that must be monitored separately. The design requires an approach that makes it easy to track temperatures and quickly make adjustments. The Schwartz team chose to apply IO-Link with the intent of improving performance and reducing wiring overhead so that changes did not affect the overall cost of the machine.
Cutting hardware costs
As well as large savings in wiring costs, the redesign also led to a substantial reduction in the number of ammeters in the switchboard doors and current transformers in the cables for each system. Each of the zones in each of the furnace chambers is monitored with the help of the IO-Link-enabled current-monitoring relay from Siemens. The devices are directly plugged into the power contactor from below, saving corresponding space and wiring.
Their previous design used signalling contacts to indicate faults. The current version is based on three-phase current measurement, which offers the advantage that each phase failure is detected as soon as it happens. This is because with the star connection they selected, a phase failure would result in a drastic current increase in the remaining phases. “We now register [a phase failure] immediately with the new monitoring relays, and we can influence this right away in control terms and adapt the current flow,” said Andreas Hollesch, head of electrical engineering. The approach delivers other benefits, as well. “It requires fewer openings in the switchboard doors. This means a higher protection class assessment according to the UL criteria, as required for deliveries to the US.”
For best results, the furnaces need to bring the workpieces up to their processing temperature as quickly as possible. For this purpose, the three-phase power contactors are switched via IO-Link capable function modules. Like the other IO-Link-enabled devices, these are connected directly to IO-Link master modules mounted in SIMATIC ET 200S distributed I/O systems from Siemens. The distributed I/O communicates with the controller via Profinet.
Monitoring heat, with redundancy
The furnace system switchboard includes multiple IO-Link masters, each of which features four channels. Every channel, in turn, offers up to 2 bytes of input and output for cyclic data transfer or monitoring the switching and monitoring devices. One IO-Link device or one group of up to four individual contactor load feeders can be connected per channel. With regard to the compact power contactors for the zone heating systems, this means that although four contactors are connected via one IO-Link channel, they can still be switched separately. This works via the corresponding function modules that have been plugged in and are connected via flat cable. “Here, too, the saved wiring overhead is clearly apparent,” noted Hollesch.
The actual temperature control in the zones is performed by semiconductor relays. These are wear-free and can be precisely regulated via the controller. So that the process engineering can be exactly measured and uncontrolled temperature fluctuations prevented, IO-Link-capable temperature-monitoring relays from Siemens also monitor each individual chamber in addition to the controller. Once again, IO-Link handles communications between the monitoring relay and the controller. “Thanks to the systematic use of digital measuring devices with IO-Link connections, we create redundancy at important points,” said Hollesch. “This is extremely valuable, both from a process view and from the safety perspective.”
Keeping it safe
In addition to process safety, operational safety is also important in systems with a high installed-power rating. For this reason, the Schwartz engineering team lavished as much attention on the safety engineering as on the standard automation. Here, too, a new approach came to the fore that avoids the disadvantages of previous solutions. In the past, connecting several devices together side by side required the use of contacts. The 3SK1 safety relay allows each basic unit to host up to five expansion modules, connected via the backplane bus, with input on the left and output on the right. It’s an approach that reduces footprint, components and cost while expanding functionality.
The system monitors the status of the emergency-stop push-buttons in all parts of the system, as well as the protective doors of the enclosure. In addition, each individual zone door is tracked to determine whether it is open or closed. Another advantage for the electrical engineering specialist is the ability to adapt the devices individually to the protection situation via DIP switches on the enclosure front. Above all, Hollesch finds that having a choice between direct switching and time delay simplifies the development of custom safety and shutdown systems, important for product differentiation and convenience, alike. “The safety relay is ideally suited to our safety concept,” he added.
Improving the process
If sensors and actuators are to be integrated into the control level, communication via IO-Link offers the best solution. In the case of Schwartz, the platform upgrade led to significant reductions in wiring, which almost entirely offset the added cost of substantially more modern device equipment. This was because it was possible to equip the feeders for the heating power with the relevant IO-Link function modules, and the current monitoring relays also have IO-Link capability. These simply mount to the contactors via connectors from below, thus saving space and wiring overhead.
The system also includes relays to monitor the temperatures in the furnace zones for safety reasons. The direct IO-Link connection simplified integration into the controller architecture. In addition to the reduction in wiring, Hollesch sees the detailed diagnostics facilitated by the IO-Link connection to be a significant technical advance in the manufacture and maintenance of heat-treatment equipment. This is because the condition data contributes valuable information for the overall process engineering, while laying the foundation for simplified service or for condition-related as well as preventive maintenance.
Overall, the upgrade yielded better-controlled process equipment at a near-parity price. The additional expense of the digital components is offset by reductions in wiring, and added cost benefits will result from advanced diagnostics and reduced downtime. The result is a platform that delivers enhanced performance and improved levels of safety in a smaller footprint and for a lower cost. “As a result of the modernisation measure with IO-Link devices, we have achieved substantial process improvements for almost identical cost,” said Hollesch.
Phone: 137 222
HMS Networks Anybus Defender industrial network security appliances
The Anybus Defender series provides a firewall to protect operational technology (OT) networks.
Rosemount 802 wireless multi-discrete I/O transmitter
The Rosemount 802 has eight discrete I/O channels, each one configurable as an input or an...
IDEC SX8R bus coupler module
The IDEC SX8R bus coupler module is designed to facilitate flexible control signal connectivity.