Sensors for quality control in battery manufacturing
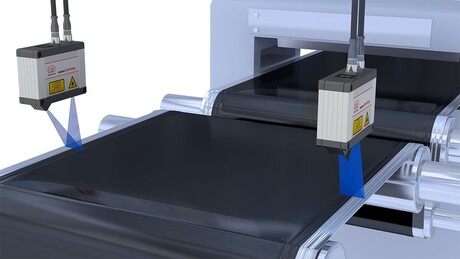
Australia has committed to leading the world in commercialising low emission technologies. We have successfully powered the local economy with reduced greenhouse gas (GHG) emissions by continually investing in local manufacturing capabilities and supporting the growth of emerging low emissions energy technologies such as clean hydrogen, ultra-low-cost solar, energy storage, carbon capture and storage (CCS), low-emissions steel and reduced methane emissions from livestock.
To accelerate the deployment of these emerging technologies, the government has supported a growing number of research and development activities in renewable energy technologies such as solar, wind, and hydrogen. Renewable energy technology has been seen as a clean alternative to fossil fuel as it can achieve similar performance to fossil-fuel-generated energy with reduced total emissions. The major challenge in using renewables as the primary energy source is keeping the electricity supply reliable.
For renewable technologies to be widespread and commercial, there need to be methods to store generated energy as a backup when the supply is not available. Energy storage systems such as lithium-ion batteries have been developed to utilise alternative energy. For example, they allow consumers to have greater control and take full advantage of the solar energy they generate from their solar panels. Lithium-ion batteries have also been used for electric vehicles and other battery-powered applications.
Locally, the Australian battery industry contributes approximately $1.3 billion to annual GDP and supports more than 6000 jobs. We are one of the highest producers of raw materials such as lithium and other critical metals for battery manufacturing. However, these materials were being shipped and processed overseas to produce battery-grade materials which were then exported back to Australia. This extra step has increased the price of locally-made batteries. It would be more economical to outsource battery manufacturing to countries with cheaper workforces specialising in this technology with the current situation.
Government initiatives to boost local manufacturing capabilities have promoted battery manufacturing to accelerate the deployment of a renewable energy future. This has resulted in a surge of interest in bringing battery technology manufacturing locally. Bringing the manufacturing home also provides more opportunities for local employment and supports the local economy. The feasibility of local manufacturing relies on our capability to reduce manufacturing costs while maximising energy storage density and operating life.
A fully-automated, precision manufacturing system to streamline production will bring down the manufacturing cost and make the technology market competitive. Optimising battery production requires sensors to monitor measurement tasks during production such as during electrode manufacturing, assembly and forming processes.
The critical control parameter in battery manufacturing is film thickness, wet layers and coatings on the electrodes. Manufacturers must meet the specifications of their customers while optimising production yield and minimising waste. Still, manufacturers have faced several measurement challenges to ensure they can reliably meet these standards.
An inline measurement system is a practical approach used for continuous measurement in the manufacturing environment. It can allow the control system to alter the processing parameters to bring the thickness back to the acceptable range if it deviates from the specification limit.
Factors to consider in thickness measurement
A key factor to consider in designing inline thickness measurement systems is to select products based on the required system’s accuracy. The performance of the measurement systems can be affected by various factors such as environmental influences, errors, and sensor accuracy. Combining these factors will create a significant measurement error if manufacturers select products based on the product accuracy alone.
Optical laser displacement sensors are used to design an industrial thickness measurement system. At least two laser sensors are required and they must be installed directly opposite one another in perfect alignment. This configuration ensures both sensors measure at the exact position of the object as the slight degree of misalignment in the sensor position can produce reasonable measurement errors. This error will amplify if the target moves in the measurement field.
In addition, it is also crucial to synchronise both laser sensors for them to perform the measurement simultaneously and at the exact opposite position to each other. If synchronisation does not occur, it will produce erroneous results as each sensor will measure at different times. This setting is highly prone to measurement errors due to micro-vibration or conveyor belt movement. Each sensor has a slightly different linearity that varies by the percentage of its measuring range.
Once the challenges in the measurement systems are addressed, manufacturers still need to consider the best technique to mount the sensors, as the mounting frame must be isolated from any source of vibration to achieve stable and reliable measurement. The mounting bracket must be made from materials with minimum thermal expansion to minimise the movement of sensors due to the temperature variation.
An integrated automated thermal compensation can also be implemented to eliminate the errors due to the expansion of materials. Regular calibration of sensors should also be performed to minimise the non-linearity errors.
Non-contact displacement measurement sensors such as single point laser and confocal sensors provide high resolution and precision measurements that can measure the slightest deviations down to nanometer resolution. Confocal displacement systems can also offer high-speed measurement with ultra-high precision up to sub-nanometer resolutions.
Measurement of other parameters in battery applications
Combining over 40 years of industrial experience, engineers at Bestech Australia provide rich expertise in high-precision testing applications. Bestech also offers not only thickness measurement technologies, but also technologies that enable reliable measurement of edges, gaps, profiles, and physical parameters such as temperature, pressure and many more. These operating parameters should be precisely controlled and monitored to optimise the manufacturing process.
For example, optical laser profile scanners can measure the edge curvature and deformations on the edge of the coating film during the cutting process. They can also be used to inspect the quality and uniformity of the coating process to detect undulations or defects.
Continuous thermal monitoring during the initial charging and discharging of batteries is crucial to understanding the temperature distribution inside the cell to identify faults such as short-circuiting. Non-contact sensors such as thermal imaging cameras or pyrometers are best used for temperature measurement tasks in a production environment. The measurement does not interfere with the process, enabling easy control and integration. Thermal imagers can also provide multiple measuring fields simultaneously and can be integrated with the control system to activate control response if the measurement exceeds the set limit values.
The drive for advanced renewable energy technology is expected to trend upwards to scale back our emission of greenhouse gases. Commercialising these new technologies will require approval from regulatory boards and the passing of complex test procedures to ensure that the products fit the market.
Measurement technology has advanced greatly in the last few years and there are sensors available for all types of measurement applications. The challenge is to know what kinds of systems are suitable for the intended applications. It isn’t easy to find the ideal systems from all available products and it is easier to consult measurement specialists for assistance.
Bestech Australia has successfully partnered with researchers and local manufacturers to support their testing and measurement needs. We supply not only products but also provide full local technical support from system design, testing and commissioning.
We have supplied high-precision sensors, measurement and inspection systems from Micro-Epsilon for testing applications in modern battery manufacturing. They offer the most extensive range of precision industrial sensors for automation and R&D applications.
In addition to Micro-Epsilon, we have also established a long-standing collaborative relationship with all our suppliers and combined this partnership with our local expertise to back our local manufacturing and testing capability.
The future of automation: Siemens SIMATIC S7-1200 G2
Industrial automation has entered a new era: one that demands smarter, faster, and more connected...
New laser scanner series with LiDAR technology for contour measurement and navigation
The latest laser scanners from Leuze are engineered to ensure manufacturing and logistics...
Revolutionising efficiency in process technology: The Danfoss iC2-Micro drive
Pacific Automation introduces the Danfoss iC2-Micro drive.