Industry 4.0 technologies as enablers in the fluid power industry
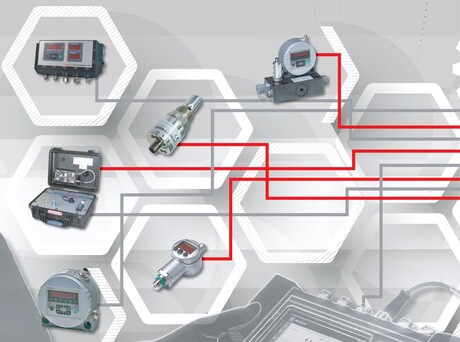
Industry 4.0 technologies enhance and advance condition monitoring using historical machine data for real-time predictions.
Industry 4.0 technology enablers are a group of diverse technologies — including machine learning, robots, additive manufacturing and cloud technology — which all work together in an ecosystem, according to HYDAC Technical Training Manager Paul Marley, who has been involved in the fluid power industry for over 30 years as a hydraulic fitter and technical trainer.
Technologies of interest in the fluid power industry
In Industry 4.0, the collaboration between cloud technology and robotics is pivotal for comprehensive solutions. Predictive maintenance, a standout innovation, utilises sensor technology for on-demand, data-driven forecasting. Enhancing and advancing condition monitoring, the inclusion of predictive maintenance into Industry 4.0 enablers represents an evolution: using historical machine data for real-time predictions.
This evolution is essential for heightened efficiency and innovation, making the seamless convergence of cloud technology, robotics, and predictive maintenance a linchpin for success. The transition from traditional monitoring to predictive paradigms marks a tangible leap toward industry goals, underlining the transformative impact of advanced technologies in shaping the future of manufacturing.
The difference between predictive maintenance and condition monitoring
Predictive maintenance diverges from traditional condition monitoring by focusing on accurate forecasting rather than the current state of the machine. Unlike its predecessor, it actively collects real-time data throughout a machine’s operation, a paradigm shift facilitated by Industry 4.0. This continuous monitoring, a departure from periodic readings, enhances accuracy and facilitates the early detection of potential failures.
The shift towards real-time data recording offers heightened precision in assessing machine conditions and identifying issues at their nascent stages. Importantly, this approach is not limited to new machines; it can be applied retroactively. However, it’s crucial to recognise that installing sensors on aged, frequently malfunctioning machines alone won’t suffice. A comprehensive strategy involves repairing maintenance practices, optimising lubricant storage, and providing training for users, operators, and maintenance personnel.
While sensors represent a powerful tool, they are part of a broader solution that requires a holistic approach. In the domain of condition monitoring, Industry 4.0 elevates possibilities, as the accuracy of information gleaned sets it apart from its predecessor, Industry 3.0, marking a transformative leap in operational insights and efficiency.
The benefits of predictive maintenance
The crucial question surrounding the efficacy and return on investment in condition monitoring versus predictive maintenance hinges on the latter’s successful implementation. While the inherent risk of failure of any applied solution exists, the affirmative answer depends on obtaining buy-in from all levels of the business. A common challenge lies in interruptions to planned machine servicing, often due to a production department prioritising schedule. However, if the maintenance department holds the authority to adhere to plans, successful data collection can lead to a tangible return on investment.
Addressing the need for condition monitoring on a reliable machine is not solely about enhancing reliability. Instead, the strategic placement of sensors on a dependable machine, after it has become reliable, aids in predicting future performance. This proactive approach acknowledges that all machines, regardless of reliability, require interventions and repairs. The advantage lies in the sensors’ ability to gather data for more accurate predictions, underscoring the importance of continuous monitoring for optimal operational insights.
In fostering a maintenance mindset, particularly in the Australian context of mechanics repairing machines, a fundamental distinction arises — the maintenance department’s role is to ensure reliability, not just to conduct repairs. Industry demands a synthesis of knowledge, skills, and technology to enhance and sustain the reliability that the maintenance department seeks to achieve.
New laser scanner series with LiDAR technology for contour measurement and navigation
The latest laser scanners from Leuze are engineered to ensure manufacturing and logistics...
Revolutionising efficiency in process technology: The Danfoss iC2-Micro drive
Pacific Automation introduces the Danfoss iC2-Micro drive.
Pacific Automation announces Microsonic partnership
Pacific Automation has announced its latest partnership with Microsonic, a pioneer in specialised...