Challenges in the maintenance of complex PLC-driven systems
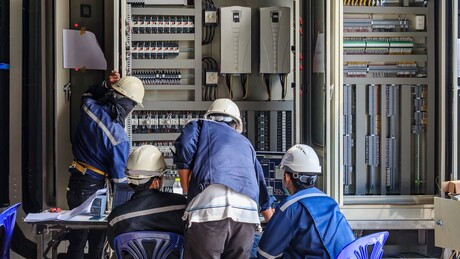
PLCs are now widespread in process control and automation systems and there is a trend towards increased complexity of such systems. The increased amount of information about processes leads to their improvement and increased efficiency, but it also leads to increases in PLC code size and complexity. Consequently, commissioning and maintenance of such systems is often a real challenge. In all but the simplest installations, there is a frequent need to synchronise operation of a number of PLCs — actions taken in one part of the system affect actions that the rest of the system may need to take. PLC programs never shrink in size — almost any code modifications increase the code size. The more complex a system, the more difficult it is to predict and later identify all the side effects of any code changes.
The trends described above lead to three major problems that control engineers face:
- Verifying correctness of system operation at the commissioning stage and then locating and fixing any issues that often emerge in both the startup phase and in early operation of a system.
- Managing changes to PLC code in running installations, detecting any side effects resulting from the changes.
- Identifying the sources of any system malfunction as systems age and wiring, sensors and actuators operate less reliably.
In many cases control systems problems have the form of ‘gremlins’ — sporadic faults appearing and disappearing seemingly at random. It may be a matter of PLC code running ‘off the rails’ due to a randomly misbehaving sensor or an unreliable electrical contact. It may be that the code which works as intended suddenly fails because it does not handle certain external events occurring in a particular sequence or at particular times. Causes for such intermittent and often very short-lasting faults are notoriously hard to identify. This is the worst kind of problem a control engineer may face, and while tightly monitoring the system 24 hours a day may allow to catch the glitch sometimes, it does not always work and is always expensive.
Another problem is that maintenance of a system often involves making changes to the PLC code written by somebody else in the past. If the code is sufficiently complex — and it often is — making such changes necessitated by system modifications or required by the end user is fraught with risks. It may be very difficult to predict what a change can lead to in terms of side effects.
Introducing PLC-Analyzer pro 6
The German company AUTEM offers PLC-Analyzer pro 6 — software with unique ability to assist in tracking and diagnosing PLC-related problems. PLC-Analyzer is a purely software solution: no additional hardware is required. It can connect to multiple PLCs at the same time, monitor their internal tags and record them with no need to change or add to the PLC code. PLC-Analyzer can be connected to a PLC via its programming interface and also, if the PLC supports it, via Ethernet or the Internet. Multiple PLCs, possibly of different types, can be simultaneously monitored in real time in the same window.
All values monitored by PLC-Analyzer can be recorded and subsequently re-played onscreen. Recorded data is accurately timed and the timing information can be easily retrieved. Project files can be used to automate frequently recurring acquisition sessions.
Additional hardware supplied by AUTEM enables the monitoring of actual physical signals, both analog and digital, independently from the PLC, and these signals can be displayed in real time in the same window as internal PLC tags. This helps to detect situations where there is a discrepancy between the actual physical values and the information used inside the PLC code.
Recording of timed data coming from possibly a number of PLCs also facilitates the optimisation of the process, leading to material and energy savings and increased plant efficiency.
Recording of values and timing of process data, taken at different times during the life of an installation, enables the detection of process changes due to equipment ageing or changes in raw materials.
PLC-Analyzer pro 6 supports the definition of trigger conditions to intercept intermittent, randomly appearing events. A trigger, when activated, saves the pre- and post-event data and can also send an SMS message or an email.
In systems with robots or moving machinery, it is sometimes difficult to investigate cases where the machine movement seems to be taking place in an incorrect way or at an incorrect time. It is possible to connect a video camera to the PLC-Analyzer and obtain simultaneous recordings from the camera and recordings of internal tags in PLCs. Analysis of such recordings can show what is the nature and, most importantly, the cause of incorrect equipment behaviour.
Records of information internal to the process, made by software not related to the manufacturer of the plant equipment, PLCs or to the developers of PLC code may assist in resolving warranty claims. In any dispute an independent ‘second opinion’ is always of benefit.
Supported PLCs
The PLC-Analyzer supports the following PLC families:
- Siemens S5, S7 and related models
- Beckhoff TwinCat family
- B&R PLCs
- Pilz PSS and PNOZ controllers
- AllenBradley ControlLogix and Compact PLCs and SLCs
- Phoenix Contact PLCs
- Bosch CL family of controllers
- GE Fanuc Series 90, VersaMax, Nano, Micro, CNC and PMC
- Fanuc R30i and R-J3i
- Omron C, CV, CS1, NJ, NX, NY and CJ2
- Mitsubishi MELSEC Q, L, A, and FX
- Schneider Modicon TSX Quantum, Momentum, Premium and Atrium
- Schneider AEG TSX A250, A120 and Micro
- Selectron
- Jetter JetControl, Delta and Nano
- Hitachi H, EH150 and Micro-EH
- all PLCs based on CoDeSys software.
PLC-Analyzer supports current as well as legacy PLCs. For many of these PLCs the software originally supplied by the manufacturer may no longer be maintained and may not be able to offer the monitoring, recording and fault capturing required by engineers today. Even if a manufacturer’s software includes tracking and capturing capability, PLC-Analyzer users report that its functionality is superior to what native PLC-related software provides.
Conclusions
PLC-Analyzer pro 6 is an indispensable tool for system integrators to help at the commissioning stage. For companies with sophisticated automation and process control systems, it offers a means to resolve PLC-related problems as they arise, to optimise the processes and to monitor the systems for changes related to ageing of the machinery, and for condition monitoring.
Companies offering services in the area of PLC programming and code maintenance should make sure that the PLC-Analyzer pro 6 is included in their engineers’ toolboxes. And if a system involves legacy PLCs, there may be no software available for advanced troubleshooting: here PLC-Analyzer pro 6 is indeed an indispensable engineering tool.
For more information please email: sales@fieldbus.com.au
The future of automation: Siemens SIMATIC S7-1200 G2
Industrial automation has entered a new era: one that demands smarter, faster, and more connected...
New laser scanner series with LiDAR technology for contour measurement and navigation
The latest laser scanners from Leuze are engineered to ensure manufacturing and logistics...
Revolutionising efficiency in process technology: The Danfoss iC2-Micro drive
Pacific Automation introduces the Danfoss iC2-Micro drive.