Automation solution a reason for popping corks
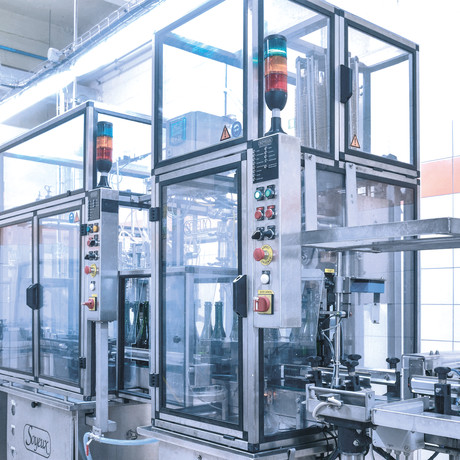
At the heart of Reims, 600,000 to 800,000 bottles of Champagne de Castelnau are produced every year. The Reims vineyard enjoys an excellent reputation and is renowned for the superlative quality of its champagne. This is achieved with a great deal of intuition and know-how. The same was required when it came to extending the special disgorgement line — which was where Bürkert came into play as a partner.
For continuously good quality
Several years ago, a special disgorgement line was added to the production facility operated by the CRVC (Coopérative Régionale des Vins de Champagne). However, the new system imposed several technical restrictions on the operators of the facility. Due to the large amount of space required for the disgorgement line, the dosing system and dosing machine are housed on different floors, resulting in a a height difference of 10 m between the dosing machine and the dosage system. From a technical perspective, the fluctuating pressures during the dosing delivery present quite a challenge.
To ensure maximum quality and optimum taste, CRVC required precisely controlled dosage delivery during disgorgement — a crucial step during champagne production. This is to compensate for the loss of liquid after the removal of the ice pellet while simultaneously exerting a decisive influence on the subsequent taste of the champagne. To overcome the existing challenges and to implement a technically flawless solution, CRVC and Bürkert joined forces to create an automation solution that would reliably and effectively fulfil all the requirements of the control function. Starting with a feasibility study, initial trial runs and the right programming, this close cooperation has led to lasting and reliable operation of the system.
It’s all about using the right settings
When it came to automating the dosage delivery system, CRVC trusted the application expertise and the components offered by Bürkert. One particular advantage for CRVC was the optimum coordination of individual components with one another, which ensures reliable results. At the heart of the solution is the Type 8619 multiCELL transmitter/controller, which records the different measurements and precisely regulates the dosing. The controller offers a simple and intuitive operating interface with a large graphics display as well as the option to connect different sensors directly. Additional components, including process control and diaphragm valve as well as pressure sensors, work together and enhance the automation solution.
Real teamwork and perfect craft
By working hand in hand, the maintenance department at CRVC and Bürkert realised an automated dosing delivery solution. While the technicians at CRVC were responsible for the installation, Bürkert handled the start-up, parameterisation tasks and provided training for the employees on-site.
The future of automation: Siemens SIMATIC S7-1200 G2
Industrial automation has entered a new era: one that demands smarter, faster, and more connected...
New laser scanner series with LiDAR technology for contour measurement and navigation
The latest laser scanners from Leuze are engineered to ensure manufacturing and logistics...
Revolutionising efficiency in process technology: The Danfoss iC2-Micro drive
Pacific Automation introduces the Danfoss iC2-Micro drive.