Smart, energy-efficient robot grippers cut production costs
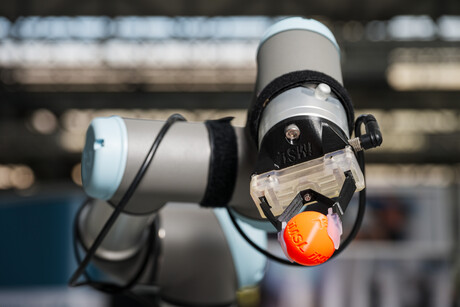
Researchers at Saarland University in Germany have developed a new type of robot gripper technology that needs 90% less electricity than conventional systems. The technology uses lightweight, shape memory materials to construct novel, non-pneumatic, industrial gripper systems that function without the need for additional sensors.
Robot arms are in use in countless modern industrial production settings, and when they are in use, most of them consume energy non-stop. Taken together, these industrial robot arms consume multiple gigawatts of electrical power. Many of the gripper systems work pneumatically with compressed air, which can be unpleasantly loud. They are often heavy, their moving parts wear out over time, and they tend to execute a constant, highly repetitive motion pattern. This existing technology sets limits on the extent of miniaturisation that can be achieved, and small-scale grippers systems with small grip points are particularly hard to achieve. Conventional robot arms are also hard to reprogram quickly, and it’s often unsafe for human workers to interact closely with them on production lines.
But a new type of drive technology may well make the industrial robots of the future lighter, more compact, more flexible and more energy efficient.
The technology developed at Saarland University is based on lightweight shape memory alloys (SMAs), which the team of engineers led by Professors Paul Motzki and Stefan Seelecke and the Saarbrücken Center for Mechatronics and Automation Technology (ZeMA) are using to build novel robotic grippers.
“The work we’re doing can help bring about a significant reduction in energy consumption, reducing production costs as well as helping to protect the climate,” Motzki said. “We can control these gripper systems in real time and whenever needed; all we need to do is apply a short pulse of electric current.”
The Saarbrücken gripper system is fully electric and is composed of bundles of ultrafine wires made from nickel–titanium shape memory alloy. These bundles of wires act not only as powerful muscles, but as nerve fibres as well. The behaviour of the bundles is due to a special property of nickel–titanium alloy; namely, that it can switch between two different crystal lattice structures. If an electric current flows through a wire made from nickel–titanium, the material heats up, causing it to adopt a different crystal structure with the result that the wire becomes shorter. When the current is switched off, the wire cools down and returns to its earlier crystal lattice structure and its original length. The material appears to ‘remember’ its original shape and to return to it after being deformed — hence the name ‘shape memory’ alloy. The wires are therefore able to exert remarkably large forces for their size and can be made to trigger tiny, controlled motions in whatever smart technology the engineers have attached to these minute artificial muscles.
“Nickel–titanium SMA has the highest energy density of all known drive mechanisms, so by using this material, we’re able to exert a substantial tensile force in very small spaces,” Motzki said.
A wire with a thickness of only half a millimetre can exert a pull of some 100 N, which is roughly the force exerted by 10 kg. But the researchers use bundles of much thinner, ultrafine wires, as more wires mean a greater surface area and therefore faster cooling rates. This means that the wire ‘muscles’ can deliver rapid, high-frequency motions and a stable tensile force. The engineering team in Saarbrücken actually holds a world record in this area: using a bundle of 20 ultrafine wires, each with a diameter of only 0.025 mm, they can exert 5 N of force at a frequency of 200 Hz. In some applications, the size of the force delivered is most important; in others it is the frequency with which the force is applied. Using the knowledge acquired from several years of research, Motzki’s team is able to tailor the composition of the wire bundles in terms of wire thickness and number of wires per bundle to meet the requirements of specific applications.
Using innovative control and design strategies, the engineers are developing drives that use SMA wires to create lightweight, manoeuvrable and cleanroom-compatible industrial robots. The technology is under continuous refinement in research and PhD projects, which has enabled the Saarbrücken researchers to develop elastic gripper systems with highly flexible ‘fingers’ that can quickly adapt to changes in the shape of a workpiece.
Conventional grippers usually rely on feedback from sensors, but the technology developed in Saarbrücken is self-sensing — the sensor properties are already built into the system. The system is controlled by a semiconductor chip.
“The shape memory wires effectively act as fully integrated sensors providing us with all the necessary data. An AI system precisely correlates the electrical resistance data with a particular deformation of the wires. As a result, the system always knows the exact position of each bundle of shape memory wires. The data-trained neural networks are able to calculate positional information efficiently and accurately even in the face of disruptive influences,” Motzki explained.
The engineers can therefore program the system to perform highly precise movements. By specifying the electrical resistance values, they can control the wires as needed.
“Unlike the standard industrial robots in use today, reprogramming is quick and easy with our system and can even be done on the fly when necessary. The gripper can adapt to the geometry of different workpieces while operating,” Motzki said.
IDEC SA1N subminiature photoelectric sensors
IDEC Corporation has expanded its photoelectric sensor range with the SA1N series of space-saving...
Leuze ROD 300 and ROD 500 series laser scanners
The ROD 300 series scanners are designed for contour detection while the ROD 500 series are...
Ximea ixX-XL Series PCIe cameras
The xiX-XL Series cameras are engineered to offer high performance while maintaining minimal...