Plastic part inspection with a 5 s cycle time
Thursday, 09 November, 2017 | Supplied by: Omron Electronics Pty Ltd
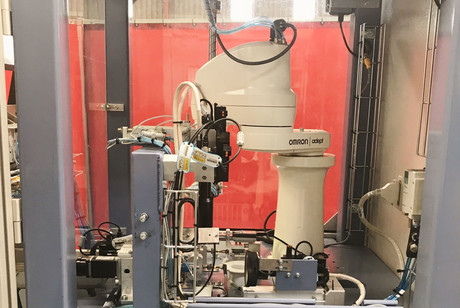
With today’s increased consumer demand, the manufacturing market has become more competitive than ever in trying to produce safer and more efficient products. Defective parts will be rejected by the end customer, so performing robust inspection becomes a must. Identifying process defects within plastic parts can be very challenging, and can only be achieved through deploying high-speed, precise machine vision systems.
Applied Robotics, based in Sydney, has been building automation machine systems for over 35 years with over 1000 system installations worldwide. Founded by Dr Paul Wong in the 1980s, the company is now a leading supplier of innovative automation and robotics systems.
Applied Robotics, as a system integrator for Omron, has been using Omron products for many of its applications. Recently, the company has been using Omron’s One Total Solution for a QC machine. The team at Omron’s Sydney office has collaborated on the project, which entails the detection of defects in a small moulded plastic component and the discarding of all faulty items. The products include Omron’s FH high-precision vision system, an Adept eCobra 350 SCARA robot, 1S servos and drives, NY IPC with HMI, NJ machine automation controller with database connectivity and Omron’s uninterruptible power supply.
The FH Vision system features a compact camera that can capture high-sensitivity and high-resolution images at very high speeds, without complex programming. Using Omron’s Shape Search III algorithm, this system measures and detects faults in the plastic workpiece. Each image is immediately processed and the results data displayed and logged for traceability. For this project four cameras are utilised to make hundreds of measurements in a cycle time of less than 5 s per part. Omron’s NYP industrial PC was used to provide visualisation, data handling, measuring and control, combining the functionality of box IPC and industrial monitor.
The eCobra 350 SCARA robot makes this machine highly autonomous. It provides high-performance transfer and handling of the small plastic parts with user-friendly interface software. It includes an Adept SmartController motion controller with an 8 kHz servo update rate to improve path following and control.
This integrated solution is said to be the industry’s first QC machine that improves reliability through continuous operation. It has little human intervention and a fast QC inspection time of only 5 s per part. This reliability and speed would have not been possible with human eyes.
“This project has seen some great ingenuity used, through the combined efforts of the Applied Robotics and Omron Engineering teams. It helps keep Australian manufacturing at the forefront in today’s competitive world by utilising up-to-date automation technology,” said Greg Field, managing director of Omron Australia and New Zealand.
Overall, the system improves efficiency of detection and gathering QC data stored in a database on the fly, which is not possible with a human process. The team will continue to improve the overall performance of the machine through testing.
“We are very pleased with Omron products and also the service from the Omron support team and engineers,” said Dr Wong. “The wide Omron product range makes them an ideal single source for the components of a multifunctional machine: basically a one-stop shop for the vision system, the OCR cameras, the robot, the PLC, the PC, the servo systems and the safety controller.
“As these machines will be shipped to clients all over the world, including the USA, Europe and Japan, utilising Omron solutions means that we can simply ‘plug in’ to Omron’s established service and support system worldwide. Overall, we are very happy with the outcome of the project and, as always, we are here to develop and commercialise leading-edge robotic systems worldwide.”
Phone: 02 9878 6377
Leuze Series 33C and 35C photoelectric sensors
The Leuze Series 33C and 35C each include stainless steel sensors designed for packaging...
Leuze IS 200 series long-range inductive proximity sensors
The IS 200 series inductive sensors enable switching distances of up to 40 mm in compact,...
Turck BI11-CK40 and NI11-CK40 inductive sensors
Turck is expanding its inductive sensor range with flush and non-flush mount inductive measuring...