Photoelectric sensors in a hot glass production line
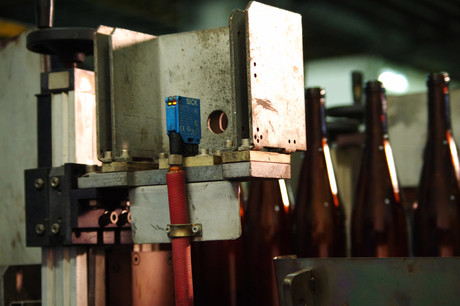
With its slogan “We are Glass People”, Heye International GmbH from Obernkirchen in Germany has a leading global position in the field of services and systems for the container glass industry. The company, which has been part of the international Ardagh Group since 2003, manufactures machines and equipment for the efficient production of container glass under its HiPERFORM brand. Its HiSHIELD testing and inspection systems can be used with a wide variety of hollow glass containers, while its specialist HiTRUST services include project management, planning, designing and construction of new production facilities and improving the efficiency of existing processes. As a supplier of high-performance machinery and production optimisation and project management services, the company’s objective is to make glass the most successful packaging material in the world.
HiPERFORM machines are used at what is called the ‘hot end’ of container glass production. During peak periods, the machines can make more than one million bottles a day over three shifts at the fluid glass melt, which has a temperature of more than 1000°C. When the bottles are transported in a continuous flow to the next stage of production, they are still at temperatures of up to 650°C. This heats the air in the production area to over 120°C. The operating conditions of the sensors that count the bottles and monitor the flow are made even more difficult by contaminants and moisture in the air and the heavy vibration of the machines.
With these challenges in mind, the employees of the product development and production maintenance departments at Heye International evaluated several different sensor alternatives. Non-optical systems proved to be unsuitable because of their inadequate operating distance, inappropriate size, poor detection results and slow response times. There were also problems with optical sensors. Through-beam photoelectric sensors were rejected because they involve twice the amount of assembly and installation work for the senders and receivers. Photoelectric proximity sensors failed primarily as a result of their operating distance and the critical hot surface of the glass bottles.
The solution proved to be the SICK ClearSens WL12G-3 photoelectric sensor for transparent materials, combined with the SW50 high-temperature reflector. The sensor’s metal housing, which has an enclosure rating up to IP67, makes it highly mechanically rugged and resistant to a range of aggressive chemicals. It has a maximum safe operating ambient temperature of 60°C. However, in long-term use at Heye International installed behind a heat shield, the sensors can withstand more than 80°C. With a sensing range in this application of 2 m, this auto-collimation sensor guarantees to provide a reliable detection function and, at the same time, has high operating reserves, for example, if a coating builds up on the sensor lens. The lens is made from scratch-proof PMMA (acrylic glass), which is resistant to chemicals and ageing. The switching frequency of the photoelectric retro-reflective sensor is 1500 Hz, which ensures that the individual bottles in the transport flow are detected and counted reliably. This is where the reflector comes in. It is installed on the other side of the flow of bottles from the sensor, where the temperatures are also high. Standard plastic reflectors would melt and become deformed after only a short time because of the intense heat. This does not present a problem for the SW50 reflectors since they have a pane of borosilicate glass mounted in an anodised aluminium frame which allows them to withstand temperatures up to 300°C over long periods. As a result of their past experiences, the team at Heye International also put a great deal of importance on the ease of use of the sensor. The bottle and container glass machines are in operation around the clock. For this reason, it is essential that the sensors can be operated during the third shift when there is no maintenance engineer available.
Phone: 1800 334 802
Leuze ROD 300 and ROD 500 series laser scanners
The ROD 300 series scanners are designed for contour detection while the ROD 500 series are...
Ximea ixX-XL Series PCIe cameras
The xiX-XL Series cameras are engineered to offer high performance while maintaining minimal...
Leuze Series 33C and 35C photoelectric sensors
The Leuze Series 33C and 35C each include stainless steel sensors designed for packaging...