Manufacturing COVID-19 rapid diagnostic tests
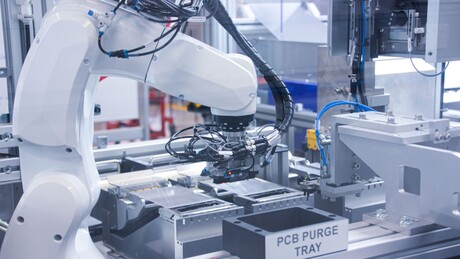
The COVID-19 pandemic has rapidly spread to all parts of the globe. There have been more than 500 million cases around the world and this figure continues to rise rapidly. Healthcare systems are overwhelmed and continue to face a multitude of challenges as they work to manage demand while providing high-quality care.
Communities, governments and industry around the world are now recognising the importance of minimising the requirement for widespread lockdowns and travel restrictions, which have been the main line of defence against COVID-19 since the start of the pandemic.
As countries around the world move towards a new post-pandemic normal, rapid diagnostic testing has an integral role in reducing disease burden, managing outbreaks and community transmission, and reducing pressure on healthcare systems.
Ellume, a Brisbane-based digital diagnostic company, has recently developed a rapid COVID-19 home test which detects the SARS-CoV-2 antigen and complies with Centers for Disease Control and Prevention (CDC) reporting requirements. Accurate results are provided within 15 minutes, providing users with quick results. With a growing list of orders, predominantly from the United States, ensuring supply was a key priority for Ellume.
To meet the consumer demand for COVID-19 home tests, Ellume has invested in new manufacturing lines for its facilities in both Australia and the US.
“COVID-19 isn’t going away anytime soon and as communities and economies continue to open up there will be increased need for rapid antigen tests, which is why automating our production is vital to meet a surge in consumer demand,” said Dr Sean Parsons, founder and CEO, Ellume.
Ellume called on Bosch Australia Manufacturing Solutions (BAMS) to automate the high-volume production of its COVID-19 diagnostic tests. This involves 27 new production lines in total — three new lines for Ellume’s facility in Brisbane and 24 production lines for its facility in Maryland.
“We are providing Ellume with 18 fully automated assembly lines for manufacturing the home COVID-19 analyser unit. This also includes an end-of-line test system that communicates to the analyser unit over Bluetooth and completes a functional check to ensure the quality of the part,” said Bradley Trewin, Programme Manager, BAMS.
“BAMS is also manufacturing nine lines for the production of the ‘dropper’ which will fully automate the assembly and packing of this product,” he added.
The production lines are being manufactured at Bosch’s headquarters in Clayton, Victoria. More than 160 robots are being utilised on this project; there are also more than 200 vision systems — cameras that inspect and evaluate the line — and more than 60 PLCs.
“We are delighted to bring the BAMS automation expertise to support Australian medtech manufacturing for a global market — a real positive for local manufacturing, and a positive for the testing and medical diagnosis of COVID-19,” said Gavin Smith, President of Bosch Australia.
Ellume’s technology addresses the unprecedented global demand for accurate and rapid diagnostics as accessible, reliable and fast diagnostics become increasingly critical to the COVID-19 response.
Given the widespread supply shortages resulting from the pandemic, Rockwell Automation has prioritised its global supply chain to applications and machines that can help in the fight against COVID-19. “Our priority is to support local manufacturing, helping to ensure that we are able to provide much-needed assistance to those requiring it urgently,” said Anthony Wong, Regional Director, Rockwell Automation. “By working with local innovative companies such as BAMS and Ellume, we can deliver next-generation technologies to help mitigate the risks of COVID-19 while also strengthening the Australian manufacturing industry.”
The new Ellume manufacturing facility will be one of the largest of its kind in the Southern Hemisphere. The production lines for Ellume’s Brisbane facility are now operational, while the final lines for the US are expected to be installed and operational in mid-2022. Once complete, the production capacity across the whole Ellume project will be nine parts per second.
“We’ve spent the last decade perfecting our technology, and now, in the midst of the COVID-19 pandemic, the role of rapid, accurate diagnostics has never been more important. Ellume is pleased to be working with Bosch to bring their world-leading automation know-how to our manufacturing process. This will allow Ellume to manufacture best-in-class diagnostics that can be relied on in a health crisis,” said Parsons.
Phone: 03 9757 1111
Leuze Series 33C and 35C photoelectric sensors
The Leuze Series 33C and 35C each include stainless steel sensors designed for packaging...
Leuze IS 200 series long-range inductive proximity sensors
The IS 200 series inductive sensors enable switching distances of up to 40 mm in compact,...
Turck BI11-CK40 and NI11-CK40 inductive sensors
Turck is expanding its inductive sensor range with flush and non-flush mount inductive measuring...