Foundry determines OEE performance indicators with RFID
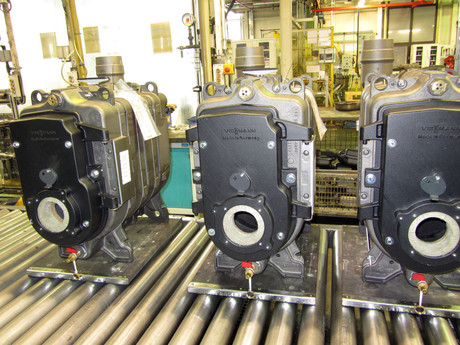
WESO, located in Gladenbach in central Hesse, is one of the largest foundries in Germany and has more than 400 employees. The company has produced high-quality cast iron products for the global market for more than 120 years. Today, the Viessmann group subsidiary is considered a full-service provider for everything related to metal casting. The product portfolio includes precision cast parts for mechanical engineering and drive construction, pumps and fittings, refrigerating machines, tractor and rail vehicle construction and components for heating boilers. The latter comprise 135 different variants in sizes from 15 to 270 kW. The throughput times are between 7.4 and 122 minutes.
By installing an ultrahigh-frequency industrial RFID system from Balluff onto the assembly line for heating boilers, WESO foundry has solved one of the most difficult problems for determining OEE key performance indicators.
Determining KPIs for OEE (overall equipment effectiveness) always proves to be extremely difficult if detecting, and comparing parameters using a control system is not possible in process flows. This is frequently true for assembly lines with primarily manual or semiautomated processes. Additional measurement systems — such as compressed air flow sensors or electricity meters whose measured values, along with other parameters, could be assigned to individual products using a controller — often cannot be integrated in these cases. As part of a ReVista project, Michael Kreide of WESO actively sought the most difficult range to measure on an assembly line for heating boilers. He did this in order to implement existing monitoring of the energy management system using component identification at every point down to the product level.
ReVista is a concept encompassing comprehensive resource and availability-oriented maintenance strategies. These strategies enable material and energy-efficient production and ensure availability as needed during operation. Ultimately, the focus is also on increasing process efficiency, which is based on the fundamental ideas of the continuous improvement process (CIP) and anchored as a company objective at WESO.
“In addition to the special requirements due to greatly varying component dimensions and changing assembly positions, we sometimes handle liquid working materials. The environment is already relatively unforgiving, and this makes it even more difficult to recognise components using optical systems,” said Kreide. This is why he sought out an RFID solution for identifying the heating boilers individually in the respective stations of the assembly line. This allows the actual consumption of operating materials such as electricity, compressed air, working material and the like to be tailored accurately to each heating boiler and allows the OEE key performance indicators to be determined.
For Kreide, this makes RFID the ideal technology given the prevailing conditions, because it can ensure automatic identification of objects of any kind and does so even without direct visual contact between the data carrier and reader. This also means that, in comparison to optical detection, information can even be read from data carriers that may be covered in dirt. Of the five different Balluff RFID systems, which all work with different transmission frequencies, the UHF BIS U version is the optimal solution for the assembly lines at WESO, as it can cover read areas of up to six metres.
However, the challenge now is to configure the process parameters of the reading system — the operating point — so that the only data carrier detected is the one that is supposed to be detected. This has to happen even if there are still other data carriers in the immediate vicinity, since this is unavoidable at WESO. This is achieved by varying antenna power to determine the setting value at which the transponder function is just barely guaranteed but other transponders do not respond. Antenna transmitting power is then increased beyond the minimum required response field intensity to set the operating point so that the identification system (transponder and processor unit) is immune to changes in the environment and fluctuations in the component or assembly. This value then also determines the actual read area of an antenna. Having the correct setting is required for a selective detection process.
The actual curve of field attenuation must be taken into account when configuring process parameters. In a real-world environment, the electromagnetic waves sent out by an antenna encounter objects of various shapes, sizes and material properties. This causes scattering and reflections. In these cases, interference known as stray waves can interact with primary waves or waves already reflected off other objects. Since the ambient conditions of the individual RFID reading points differ from each other, the response field intensity or the corresponding antenna transmitting power must be determined individually for each detection point. The RFID professionals from Balluff do this on-site using their special Power Scan procedure supported by software developed specifically for commissioning these types of applications. This allows the sensitivity of the data carrier to be measured at an assembly point in the space in front of the antenna, which determines the minimum required antenna transmitting power. Using the knowledge of what is known as an excitation characteristic diagram, the read area can now be defined in such a way that data carriers in closer proximity are not read inadvertently.
At WESO, setting the process parameters using the Power Scan process also provided the ideal positions for the antennas as well as the most suitable attachment point on the heating boiler housings for interchangeable data carriers. A total of four antennas are installed for monitoring the work stations in the assembly lines. All four are connected to a single, shared processor unit. The first antenna covers the material pick-up area. Here, the individual segments of the heating boiler are positioned by hand and a data carrier with a permanent identification number is affixed onto the base body. This requires that the worker removes a transponder from a storage container and holds it in the read area of the antenna. Its transmitting power is restricted so that the read distance of the transponder is only about 30 cm. This setting is used to ensure that only transponders held immediately in front of the antenna are read and registered in the system. However, the transponders next to it in the storage container are not detected. A second antenna detects the transponder when the heating boiler moves into the next joining station. After press-fitting, various attachment parts are assembled before the heating boiler reaches an inspection station for a leakage test. A third read station installed here makes it possible to assign operating and auxiliary material consumption selectively once again.
“Configuring the read station in this area proved to be particularly challenging because up to four heating boilers can be in the confined space within the inspection station depending on the type of heating boiler. Additional heating boilers can accumulate immediately upline of the inspection station infeed due to the continuously running preassembly,” explained Kreide. Once the leakage test has been completed, the heating boilers reach the packaging area where the transponder is removed again and, at the same time, the completion message is issued by the fourth antenna installed at this point.
Looking back on the successful installation of the Balluff RFID system, Kreide said, “They knew what they were doing!”
Phone: 03 9720 4100
Leuze Series 33C and 35C photoelectric sensors
The Leuze Series 33C and 35C each include stainless steel sensors designed for packaging...
Leuze IS 200 series long-range inductive proximity sensors
The IS 200 series inductive sensors enable switching distances of up to 40 mm in compact,...
Turck BI11-CK40 and NI11-CK40 inductive sensors
Turck is expanding its inductive sensor range with flush and non-flush mount inductive measuring...