Driving paper production at Visy's pulp and paper mill
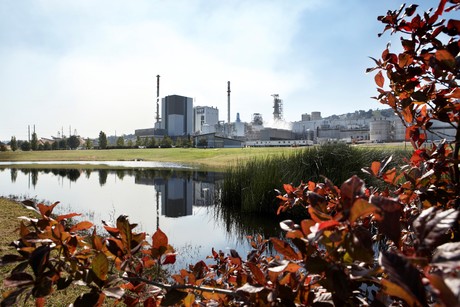
Visy is a global leader in the packaging, paper and resource recovery industries, providing high-quality, innovative and sustainable packaging products and solutions. The company has more than 120 sites across Australia, New Zealand, Thailand and Vietnam, and trading offices across Asia, Europe and the USA.
Visy’s Pulp and Paper mill in Tumut, New South Wales, is the largest integrated pulp and paper mill in Australia and produces high-quality kraft paper for both domestic and international markets. Two million tonnes of plantation-sourced wood is processed at Tumut each year — the site is one of Australia’s largest exporters of containerised manufactured goods and hosts a renewable energy generation facility, producing half of the plant’s own energy needs. The plant also operates a closed loop water system, where all mill wastewater is re-used for farm irrigation.
In financial year 2017–18, paper machines 9 (PM9) and 10 (PM10) at VISY Tumut produced over 681,000 tonnes of unbleached kraft paper.
As a company that is always looking towards the future, Visy took a proactive approach in upgrading legacy drive control equipment on the PM9 winder downstream of the paper machine to avoid any potential for downtime while also futureproofing the Tumut plant.
Visy contracted Rockwell Automation to conduct the planning and design stage of the project.
“The first step of the project was to perform a FEED study,” said Matthew Barrett, Senior Project Engineer at Rockwell Automation. “As part of this process we worked closely with Visy to gain a detailed understanding of the engineering requirements for the winder upgrade.” Upon completion of the FEED, a detailed proposal was prepared and the upgrade commenced.
Paper Machine 9 produces a ‘jumbo roll’ that is 3.2 m in diameter by approximately 5.5 m wide. This jumbo roll then moves into the winder, which cuts the paper into smaller rolls to suit customer requirements and allows for easy shipping. Each roll coming off the winder is wound with a specific tension profile, to avoid collapse or telescoping. The operational requirements of the drive system are very demanding — it must be able to rapidly accelerate and decelerate the heavy rolls and maintain web tension and production speed of up to 2500 metres/minute while the diameters of the rolls are changing.
To achieve consistent roll quality, it is essential to keep the whole winder system stable. Settings on the drives and control system must be finely tuned to ensure that tension fluctuations do not affect the roll structure. To achieve this, coordination of the drives on the winder was crucial. “If all the drives are not coordinated, the winder is unable to work effectively,” Barrett explained.
The Allen-Bradley PowerFlex 755TM drive system was decided on as the best choice for this application. The coordinated drive systems reduce energy consumption as they are able to share energy on the bus — some drives are motoring while others are regenerating. With a smaller footprint than the legacy system, the drives were also able to reduce the space required to house the system.
Control requirements were provided by Allen-Bradley GuardLogix controllers and all safety devices were upgraded to Cat3, Pld. Further safety upgrades are easily achievable due to the GuardLogix system being installed. EtherNet/IP provided secure communications between the controller and drives.
HMI requirements for the winder were delivered by FactoryTalk View software. The WindPro solution was engineered by Rockwell Automation to help paper manufacturers monitor and control paper roll density and help prevent quality defects, such as wrinkles and tears. It provides real-time winder control and monitoring including recipe management, roll data, general operator interface to the winder, faults, alarms and trending.
“This was one of the first applications in the world that used the new PowerFlex 755TM drives, so we worked closely with the product specialists in the US regarding some of the technical aspects of the drives,” Barrett explained. “As there was a limited time available for commissioning the new system, we conducted a factory acceptance test (FAT) to provide a complete simulation of the machine. This allowed Visy to see the drive system in operation and we were able to go through all of the functions to make sure it met Visy’s requirements.”
The installation and commissioning of the system was conducted during the plant’s annual shutdown, with no significant issues. In fact, the first roll produced by the winder was sellable quality. “The new winder drive system is working well and there has been no downtime due to drive system issues. We have remote access to the system, which helps with troubleshooting as required,” Barrett said.
“The technical support from Rockwell Automation has been great,” said Santiago Vargas, Visy Tumut Project Engineer. “The new control and drive system for the winder is performing really well and by having remote access to the system, Rockwell Automation is able to continue to provide support as required. The project has been a success for Visy and we are very confident in the Rockwell Automation team.”
Phone: 03 9757 1111
Mitsubishi Electric FR-D800 series inverters
Mitsubishi Electric has launched its FR-D800 series inverters, designed to deliver better...
IDEC SA1N subminiature photoelectric sensors
IDEC Corporation has expanded its photoelectric sensor range with the SA1N series of space-saving...
Leuze ROD 300 and ROD 500 series laser scanners
The ROD 300 series scanners are designed for contour detection while the ROD 500 series are...