Contract manufacturer uses edge technology to improve product quality
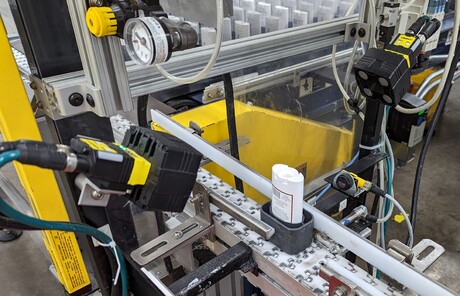
Federal Package, based in Chanhassen, Minnesota, is the preferred contract manufacturer for many well-known brands. The company specialises in the development and packaging of a wide range of health, beauty and personal care products including deodorants, sunscreens, lip balms, serums and a variety of lotions and creams. It prides itself on delivering a quality product that supports its customer’s brand image.
A recent project at Federal Package that involved producing deodorant for a personal care company helped spur the investment in automated inspection. There were two inspection points within the manufacturing process that were good candidates for automation. One was checking the plastic packaging that housed deodorant for drips that not only indicated overfilling but also resulted in a poor product presentation. The second quality checkpoint was label inspection. This involved verifying that the correct label was used and that it was applied in the correct position and orientation on the packaging.
The production line that Federal Package planned to use for this project required operators to manually inspect products after they were filled. To improve productivity and increase quality, automated inspection of each package was an ideal solution.
Federal Package has invested in machine vision in various areas of its business and has had previous experience with Cognex, which led the company to select Cognex the next time it needed a vision system, which presented itself with this new deodorant inspection application.
Cognex Account Engineer Nick Raddatz introduced one of Cognex’s newest 2D vision systems that featured edge-learning technology embedded in the device. Edge learning is a subset of artificial intelligence (AI) in which processing takes place on-device, or ‘at the edge’ of where the data originates, using a pre-trained set of algorithms. The technology is simple to set up, requiring less time and fewer images for training compared to other AI-based solutions, like deep learning.
Noah Leuer, a manufacturing engineer at Federal Package, felt this new vision system could do the job and the company bought both a colour and a monochrome system. They used the monochrome version for drip inspection and the colour version for label inspection, as it could more effectively differentiate between the label boundary and the body of the deodorant container.
The drip inspection system evaluated each deodorant package body for excess deodorant that resulted from overfilling. If there was any sign of deodorant on the outside of a package, that unit would be rejected.
“We have between 30 and 40 different deodorant designs which include different fragrances and colours, which means there are many different colours associated with the containers that the camera sees,” Leuer said. “After trialling the system, we learned that the system’s edge-learning capability was intelligent enough to filter out the colours and focus on the actual defects in the product.”
The drip inspection line runs close to 80 units per minute and the label inspection line runs around 60 units per minute. In both cases, the automation enabled more throughput, as well as guaranteeing all units were inspected, which manual inspection could not achieve. The company’s accuracy rate for catching defects is now over 99%, which means minimal human intervention to remedy the few defective units that get through the inspection.
Once initially installed on the line, the vision systems were deployed on the production line within an hour. This ease of use enabled Leuer to hand off the setup of the vision systems to the maintenance department, which allowed him to address other automation projects.
Multiple varieties of container types with different colours and labels also meant frequent changeovers. However, the automated inspection system handled the changeovers easily.
“The edge learning classify tool enabled us to quickly train the system with images of both good and bad examples, which simplified changeovers to different types of deodorant products,” Leuer said.
Training the system for new product runs only took 5 or 10 minutes, which helped maximise operational efficiency. In addition, Federal Package found that it did not need to retrain the system as often as expected, which saved time and increased the efficiency of the line.
The new edge learning-based automated inspection system that was put in place has enhanced Federal Packaging’s quality assurance process.
Federal Package has also invested in a Cognex AI-based vision system that it plans to use to verify date and lot codes that must be printed on its products to enable tracking through the supply chain for inventory management and lot control as required by its customers and the FDA. As its business continues to grow, Federal Package plans to add more Cognex vision systems across various lines to enhance end-of-the-line product quality where it makes sense.
Phone: 03 9720 0211
Leuze Series 33C and 35C photoelectric sensors
The Leuze Series 33C and 35C each include stainless steel sensors designed for packaging...
Leuze IS 200 series long-range inductive proximity sensors
The IS 200 series inductive sensors enable switching distances of up to 40 mm in compact,...
Turck BI11-CK40 and NI11-CK40 inductive sensors
Turck is expanding its inductive sensor range with flush and non-flush mount inductive measuring...