Automation delivers five-fold increase in productivity
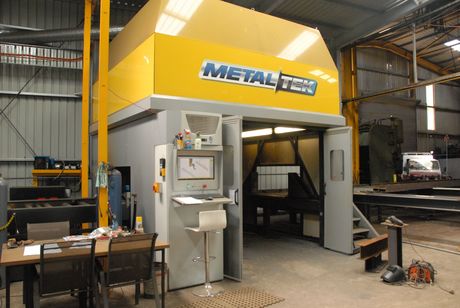
Faced with increased international competition and a steep drop in mining construction, Kmar Engineering sought to automate its structural steel coping process. As a result, the company achieved a 500% increase in production, better finishes and dimensional tolerances, and the ability to produce a wider range of profiles, including pipework.
Located in Doyalson on the Central Coast of New South Wales, Kmar operates out of two factories processing beams, structural steel, tanks, silos, hoppers, ladders, walkways, platforms and much more. The business looks back at a 30-year history, mainly focusing on the mining industry. However, the recent steep drop in mining construction and pressures of both domestic and global competition have led company owner Peter Learmonth to change the way he thinks and the way he works. “Working smarter, concentrating your time on value-adding activities means obtaining greater manufacturing efficiencies and increased productivity,” he said.
In face of intense competition to drive labour costs down and with the relentless pressure from the market to reduce lead times, Kmar decided it was time to automate its factory. “My aim was to provide steelwork to the local market efficiently and cheaper than before,” explained Learmonth. “We decided to offer custom, versatile steel processing services in the short term to the steel suppliers themselves, who cannot afford or are not willing to wait four weeks for stuff to come from China.”
After thorough investigation, Learmonth decided to go for a locally made machine from Brisbane-based Advanced Robotic Technology (ART). The company is a renowned manufacturer of routers and plasma cutters sold under the ART brand, and has recently added the Metaltek brand to its line-up of Australian-made machines. The Metaltek XB1200 structural steel coping machine offers fully automatic structural steel, pipe and plate processing in one machine.
“I had a look at some American and Canadian machines,” said Learmonth. “When I started looking at the ART machine I went to Brisbane, […] and I was really quite impressed. The machine does more things than the competitors’ machines I investigated. Of course we also liked the idea that it was Australian made.”
The machine was installed in December 2014 and after initial training and familiarisation with the machine, the company has been busy with work for the last couple of months. According to Learmonth, installation went smoothly and ART’s support and service were very good. “We couldn’t speak highly enough of them.”
The Metaltek XB1200 structural steel coping machine offers fully automatic structural steel, pipe and plate processing in one machine.
Kmar’s increase in orders from steel suppliers can largely be attributed to the machine’s versatility and productivity. Being able to automatically process not only beams but pipework has transformed the business and opened up new opportunities. “We’ve been doing a fair bit of pipework since we installed the Metaltek XB machine, cutting all angles, custom shapes, creating weld preps, slots and bevels,” he said. “We’ve recently created weld preps and widening joints on 170 tons of pipe with our Metaltek machine. In the past, we wouldn’t have done that job. Doing it manually would have taken us at least five times longer and been nowhere near as accurate!”
The machine’s versatility and range of capabilities including four-sided processing is complemented by its user-friendliness. “The controller is easy to learn, it is easy to pick things up and get started with the job, although there are so many things in there we are still learning.”
An extra bonus is the XB’s ability to cut structural steel and pipe directly from any 3D CAD program using 3D solid and mesh files, so there is no need to learn new specialised steel software to generate machine-oriented NC1 files.
Moreover, a 3-axis material handling conveyor systems and cross-transfer conveyors for loading and unloading eliminates a large percentage of lifting, flipping and moving of steel members between machines. “We simply prepare the next length of steel for loading while the previous one is cutting. A tick box on the touch screen lets the controller know that the next length is ready to load.” Inside the work area, the machine automatically senses material dimensions, and an extra-articulated robotic arm performs the desired cuts, even underneath the beam.
“The machine has been changing directions for us,” Learmonth concluded. “It is really like a breath of fresh air, it is almost like ‘being on holidays’… what I mean is we can now concentrate on the value-add work, be more productive, concentrate on strategic business developments and let the machine do the hard work.”
Phone: 07 3393 6555
Ximea ixX-XL Series PCIe cameras
The xiX-XL Series cameras are engineered to offer high performance while maintaining minimal...
Leuze Series 33C and 35C photoelectric sensors
The Leuze Series 33C and 35C each include stainless steel sensors designed for packaging...
Leuze IS 200 series long-range inductive proximity sensors
The IS 200 series inductive sensors enable switching distances of up to 40 mm in compact,...