Minutes instead of days: energy chains reduce the assembly time of machining centres
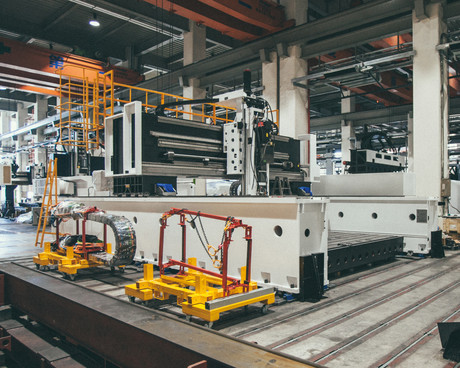
In very few industries are throughput times as important as in the machine tool industry. Cutting out individual work steps means that considerable savings in process costs can be achieved. The design engineers at Hartford, the largest manufacturer of CNC machining centres in Taiwan, know this as well. The manufacturer has 50 years of history exporting more than 46,000 machines to 65 different countries. Since 2017, the company has been developing CNC equipment of the AERO series — the robotic machining centres for very large components needed for the aerospace industry, for example. In this industry, precision and reliability are critical factors. Therefore, it was important to have a reliable means of energy supply from the switch cabinet to the moving parts, which include spindles and motors. At the same time, all the information regarding axis position and dynamics must be passed back to the control system without any interruption. In the first model in this series, the AERO626, this happens at accelerations of up to 0.5g and a maximum travel speed of up to 60 m/min.
Hartford’s engineers turned to igus, since it develops energy chains that are configurable and predictable online, as well as igus’s specially designed, highly flexible chainflex cables that have been tested for up to two billion cycles per year. As a complete system from one source, these so-called ‘readychains’ are harnessed to Hartford’s requirements and then delivered as ready-to-install equipment.
For Hartford, the advantage of using the igus ready-made energy chains is that the amount of installation space needed can be reduced considerably. One reason for this is that all chainflex cables on the machine have an oil-resistant PUR outer jacket. As additional protective hoses are superfluous because of this feature, the amount of space needed for the cables, and therefore the size of the chains, is reduced. The absence of these protective hoses reduces cost and helps ease maintenance too.
Through close collaboration between igus Taiwan and Hartford, a 3D drawing of the readychain with assembly frame was created in order to simulate the assembly procedure. The benefit could be seen straight away: the first energy chain fitted with all electrical cables was installed on the machine in an hour. The second chain with hydraulic hoses was installed even faster, taking just 40 minutes.
Normally, machine tool manufacturers try to avoid too many different work steps being carried out on a system at the same time. A lot of manual work done by different employees does not necessarily enhance efficiency; on the contrary, it increases the probability that errors can occur. By using igus readychains, all four e-chains from igus can be fully installed in half a day. Previously, two employees took one and a half weeks for the work on the X axis of an AERO system and a further week for the energy supply of the Y and Z axes. In this way, Hartford is able to cut out some work steps, reduce process cost and, at the same time, greatly improve productivity.
Phone: 1300 65 75 64
AchieVe PSA series power supplies
The AchieVe PSA series of switchmode power supplies offer basic DC power for general industrial...
Phoenix Contact Trio Power power supply
The third-generation Phoenix Contact Trio Power power supply is now available with a protective...
Phoenix Contact PTCB 48 VDC circuit breakers
The PTCB single-channel circuit breakers can now protect loads with a supply voltage of 48 VDC.