Hoisting a gondola for building maintenance
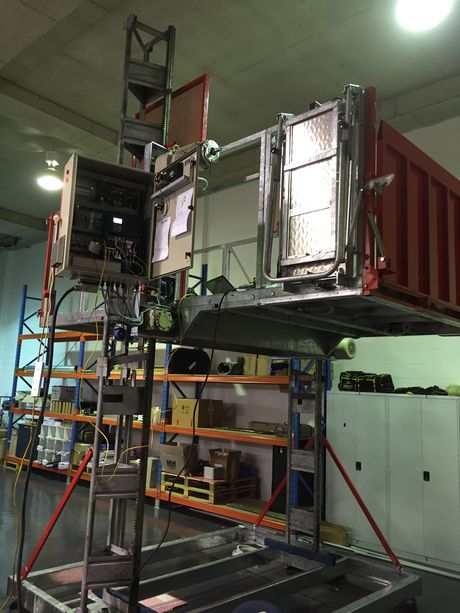
How do you lift a 2.5-tonne gondola, at various speeds, up a vertical hoist, and stop it at the right position, within ±2 mm accuracy?
This was the problem confronting Chris Probst, Omron’s product specialist for AC drives. The 2.0 by 4.5 m steel-framed gondola needed to be able to transport two people, with paints and other equipment, to the higher reaches of building walls for maintenance. It was supported at either end by stacking towers, which could be extended by adding prefabricated modules to increase the hoist travel. Both towers incorporated a rack that meshed into its own pinion, driven by separate motors on the gondola. The pinions were selected so that their size, relative to the rack, provided appropriate gearing for both the speed of the movement and the torque required.
Timing was crucial, as both pinions needed to rotate together to ensure the gondola was kept horizontal at all times. This was achieved by powering both motors from the same drive — an Omron 3G3RX vector control unit. The drive was rated at 18.5 kW and expressly oversized for the two 6 kW motors, to overcome losses and ensure sufficient current could be delivered.
As with any vertical lifting application, a mechanical holding brake was required to ensure the load did not drop when the motor stopped or was de-powered. Like a successful hill start in a manual automobile, the holding brake needed to be released at precisely the right moment. This is just after sufficient torque had been generated by the motor to hold the load and then start the movement.
Maximum torque is required at the start of an ascending movement, which works against gravity. Synchronous motors have great difficulty with this because they rely on rotational motion for mutual induction to generate torque. Higher specification drives can provide extra torque but require feedback through an additional encoder.
While the 3G3RX drive can also handle an external encoder, for closed-loop vector control, mounting one in this application would have been impractical. However, the drive supports two sensorless vector (SLV) control modes, which, as their name suggests, do not utilise external sensors. Standard SLV mode produces 200% of rated torque at 0.3 Hz output, while Zero-Hertz SLV mode produces 150% torque at standstill. This method uses pure flux current in the motor and has been patented. It was used here to enable zero speed load holding.
The lack of a feedback sensor for detecting actual rotation meant the drive needed to calculate optimum output via its built-in auto-tuning function. A series of motor parameters were entered into the drive, and auto-tuning was performed both with and without motor rotation.
Another challenge entirely was the descending movements. Gravity assists in these cases and the motor acts as a dynamo, regenerating energy back onto the drive’s DC bus. The drive, however, must maintain the required speed regardless. Whenever movements are fast or load inertia high, as in this application, the drive must dissipate surplus energy as heat in an external resistor.
“I can’t believe how smooth both the upward movements were in the 0 Hz domain and downward movements with regeneration,” said Probst. “Whereas previous systems resulted in jerky starts and inaccurate stopping, the 3G3RX drives effortlessly handle low-speed applications requiring high torque, such as elevators, hoists and cranes.”
Phone: 02 9878 6377
EXAIR ATEX cabinet cooler systems
EXAIR's ATEX Cabinet Cooler systems are designed to provide a solution for keeping electrical...
DEWESoft GridPhase phase identification system
GridPhase is a phase identification system designed to bring precision and efficiency to phase...
AchieVe PSA series power supplies
The AchieVe PSA series of switchmode power supplies offer basic DC power for general industrial...