Dairy heat exchanger meets tight spec for Burra Foods
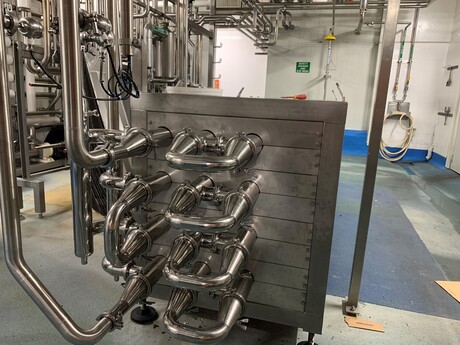
Burra Foods is a leading Australian dairy ingredient processor, producing value-added dairy products for the global food manufacturing market. An upgrade at their processing plant in Korumburra, Victoria, necessitated the use of a heat exchanger to warm frozen milk products, but existing building and infrastructure meant that the available space was severely limited.
The line in question produces skimmed milk concentrate and cream from frozen concentrates which are then thermalised and cooled to ambient processing temperatures. The required heat exchangers needed to raise the temperature of the product from -5 to 18°C prior to the final heater, which includes melting the frozen product. After this the product is then cooled from 10 to 5°C in the final cooler. Due to the consistency of the skimmed milk concentrate and cream the product is quite viscous, so the heat exchanger needed to resist fouling and provide good heat transfer performance, while also integrating with the plate heat exchangers used in the process in an extremely limited footprint.
The solution was an HRS MI Series corrugated tube heat exchanger, which provided the necessary heating and cooling requirements in the tight space available and also resulted in a small pressure drop, another important consideration for this installation. Following an initial enquiry at the end of 2019, the unit was installed in mid-2020, and it has exceeded performance expectations since final commissioning, with a production capacity of 5000 kg of product per hour.
“Other suppliers couldn’t match HRS’s offering in terms of tubular heat exchangers and the level of detail provided,” said Stuart Shattock, Process Engineering Manager at Burra Foods. “Once we placed the order, there was a slight delay due to COVID-19, but HRS managed to produce it as a rush order and the installation and commissioning was really smooth. In fact, they were able to accommodate a change to the process design partway through installation and make some improvements on the fly, which is great for a nimble and flexible food and beverage business like ourselves.
“There are two parts to the unit: the heater and the cooler. The heater has performed well and done exactly what we expected, while the cooler has actually done more than we expected. Overall, we are very happy with the product and the output from it.”
“HRS’s corrugated tube heat exchanger technology was required in order to prevent fouling from the thick cream element of the product,” added Chris Little, Australian Director at HRS Heat Exchangers. “The requirement for a heat exchanger with a small physical footprint meant that coming up with the final design was a challenge, but our engineering team rose to the occasion and provided a reliable solution that meets all of Burra Foods’ needs.”
Phone: 03 9489 1866
AchieVe PSA series power supplies
The AchieVe PSA series of switchmode power supplies offer basic DC power for general industrial...
Phoenix Contact Trio Power power supply
The third-generation Phoenix Contact Trio Power power supply is now available with a protective...
Phoenix Contact PTCB 48 VDC circuit breakers
The PTCB single-channel circuit breakers can now protect loads with a supply voltage of 48 VDC.