Research project improves efficiency in industrial manufacturing
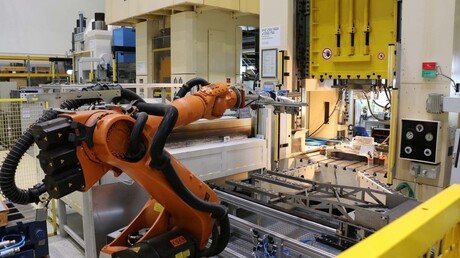
Across the world many manufacturing companies use large fleets of equipment and complex production facilities. Modern machines fitted with an extensive range of sensors supply an increasing amount of data, resulting in huge optimisation potential for production by means of data analysis using artificial intelligence (AI) and machine learning (ML). A consortium comprising several Fraunhofer institutes has been seeking to harness this previously untapped potential for the benefit of the industry.
As part of the four-year lighthouse project “ML4P — Machine Learning for Production” lead by the Fraunhofer Institute of Optronics, System Technologies and Image Exploitation IOSB, the consortium has created an efficient solution based on ML technologies that companies can use to optimise their production processes. ML4P uses a combined approach consisting of a scientifically based process model and software tools derived from this. The objective is to make production faster and more energy- and resource-efficient. The ML-based software suite can, for example, analyse machine data to discover hidden contexts and use these to optimise the manufacturing process. It is also capable of improving production on an ongoing basis thanks to its ability to learn. This is also beneficial for the quality of products.
However, the software is only one part of the ML4P approach — its process model acts as a key foundation.
“We don’t just pop up with a completed software solution for a company — instead, we guide them through the process model, taking a methodical, step-by-step approach,” said Christian Frey, Head of Systems for Measurement, Control and Diagnosis at Fraunhofer IOSB and ML4P project manager.
The first step is to analyse the current state of the production process. Based on the results, the experts identify potential areas for optimisation, set targets and develop a concept for implementing ML4P. In the next step, they examine whether the concept can actually be implemented with the available machinery and their data, and also how it lines up with the company’s objectives.
“The process model is divided into several phases that build upon one another. The decision as to whether a company actually opts for ML4P will only be taken when it is certain that the concept is viable, is easy to implement and economically reasonable,” said Lars Wessels, ML4P deputy project manager.
The following step involves transforming process data from the machinery into a comprehensive, digital information model. In this process, expert knowledge is just as important as the data. Engineers are actively involved and contribute their knowledge about all steps of the process, including the specific tasks and interactions of the machines. The expert knowledge is integrated into the ML4P pipeline, which learns a process model from machine data. Implementation and test operations follow afterwards. Eventually, the process model is deployed and daily production begins.
The software suite offers a range of tools for implementing ML-optimised production, including generic tools for typical tasks such as monitoring a machine’s operating state. These are compatible with a number of industrial communication interfaces such as OPC UA. Wherever possible, Fraunhofer researchers tried to avoid using proprietary software protocols, relying instead on established standards and programming interfaces.
Other strengths of this concept are its scalability and flexibility. Once put into operation, each module can be customised at any time and use the incoming new data to continuously update the process model and thus point out potential for further optimisation. New machinery can be integrated as can most older machines — even those that are 30 or 40 years old.
“It is not so much about the machine, but whether it can provide suitable data, for example if it is equipped with dedicated sensors,” Wessels said. Smaller companies can also apply ML4P, even if they only want to optimise specific parts of a manufacturing process.
“Many companies are still sceptical about the use of artificial intelligence or ML because they have not yet recognised the enormous potential that machine learning offers for production. However, the modular platform from Fraunhofer provides transparency, flexibility and scalability, thus reducing the barrier to entry,” Frey said.
The ML4P team has already tested the integrated concept across various fields of application. Solutions for hot sheet metal forming were developed at the Fraunhofer Institute for Machine Tools and Forming Technology IWU. The Fraunhofer Institute for Factory Operation and Automation IFF has optimised the production of membrane filters and the Fraunhofer Institute for Mechanics of Materials IWM has tested the software suite at a glass-bending plant. The software tools were continuously improved based on the experience gained during these field tests.
“We are very happy that the ambitious ML4P project has been successfully completed after four years of work,” Frey said. “For the first time, companies in the manufacturing industry have the opportunity to experience the full optimisation potential that machine learning can bring to production.”
Mettler Toledo oxygen measurement guide
Mettler Toledo has produced a guide for the process industries that explains the measurement...
Mettler Toledo pH sensors operating guide
Mettler Toledo has released a booklet describing good operating procedures for pH sensors, aimed...
Honeywell Process Solutions LEAP project services
Honeywell Process Solutions has launched its LEAP project services (Lean Automation of Automation...