Compensating for grid fluctuations with bivalent furnaces
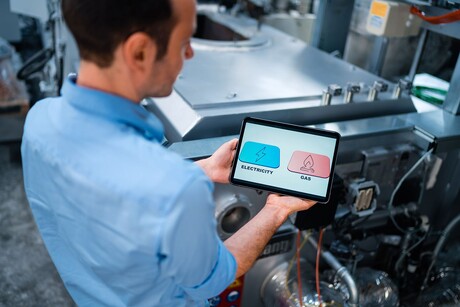
Due to the high energy consumption of melting and holding furnaces, the cost of the energy represents a significant cost factor in the production of castings. The price of electricity fluctuates significantly over the course of the day. This can be explained, for example, by the varying utilisation of the power grid or the volatile feed-in of energy from renewable resources. As a result, companies should design their energy consumption flexibly to operate their production processes as cost-efficiently as possible. Together with its partners, the Fraunhofer Institute for Manufacturing Engineering and Automation IPA is developing a bivalent furnace that enables dynamic switching between gas and electricity. This will ensure that operation is flexible in terms of the type of energy deployed, allowing energy to be used when it is most cost-efficient.
Pressure die-casting is one of the most efficient moulding processes — a single mould can be used to produce hundreds of thousands of castings. But like so many industrial processes, this production method is extremely energy-intensive, with crucible furnaces leading the charge in terms of considerable energy consumption. Such furnaces are used to melt metal ingots that are then pressed into a metallic mould at high pressure and speed.
The total energy consumption of light-metal foundries is accordingly high; in Germany, for example, it was recorded at 4.4 TWh by the German Federal Statistical Office in 2019. By designing a solution that renders production processes more flexible in terms of the energy used, the Fraunhofer Institute is aiming to help companies compensate for fluctuations in the power grid and reduce their production costs.
The Fraunhofer Institute for Manufacturing Engineering and Automation believes that bivalent furnace technology is the key to energy-flexible operation.
“Furnaces are typically operated using only one energy source — either fuels such as gas and oil or alternatively electricity. Bivalent crucible furnaces, however, can switch dynamically between electricity and gas during operation,” said Alexander Mages, a researcher at Fraunhofer IPA in Stuttgart. “It means that we can use different energy sources to cover the energy requirements of crucible furnaces in any operating state.”
Working with partners Hindenlang GmbH, Bark Magnesium GmbH and the Institute for Energy Efficiency in Production (EEP) at the University of Stuttgart, the research team has modelled various heating concepts, optimised plant designs through thermal simulations, and implemented the bivalent design into a crucible furnace. The crucible furnace forms part of a plant centre including punches, presses and CNC machines at Bark Magnesium’s die-casting foundry. Tested successfully in April 2023, it was commissioned in May to melt magnesium ingots.
Given that the melt has to be kept at a constant operating temperature, the researchers’ aim was to use energy flexibly, at ideal electricity prices, without having to interrupt the production process due to a changeover. This means that the bivalent furnace can be switched to gas operation when the electricity price is particularly high — for example, due to the regular increase of electricity consumption in the mornings or evenings. When prices are low, on the other hand, the system switches to electricity operation.
“An energy-flexible demand for electricity can contribute significantly to reorienting our electricity system toward renewable energy generation. Industrial companies account for 44% of our total electricity consumption,” Mages said.
Operators can switch manually between electricity and gas using the furnace control system or the furnace switches automatically via a signal issued by the control network. Likewise, the control network connection provides the option of switching after receiving a signal from the electricity supplier.
“By switching the energy source, the process start time does not have to be postponed to when electricity prices are low, nor do shifts have to be adapted to accommodate break times. These are common measures to achieve flexibility in terms of energy,” the researcher pointed out, explaining another advantage of the bivalent furnace.
A follow-up project aims to optimise the furnace, including its heating and network design. Using thermal measuring elements, the project partners are determining parameters such as temperature distribution in the furnace to draw conclusions about energy efficiency. They are also testing whether the furnace can be operated with hydrogen.
Mettler Toledo oxygen measurement guide
Mettler Toledo has produced a guide for the process industries that explains the measurement...
Mettler Toledo pH sensors operating guide
Mettler Toledo has released a booklet describing good operating procedures for pH sensors, aimed...
Honeywell Process Solutions LEAP project services
Honeywell Process Solutions has launched its LEAP project services (Lean Automation of Automation...